Model-based Motion Planning
Table of contents
Important data at a glance
Project titel: | Basics for the efficient use of multi-axis interpolating servo drives in processing machines |
---|---|
Duration: | 10/2010 – 06/2013, 01/2015 – 06/2017, 10/2018 – 09/2020 |
Collaborative project: | yes |
Funding: | DFG #182157057 |
Processor / Contact person: |
Dipl.-Ing. Olaf Holowenko former processors: Dr.-Ing. Bernd Kauschinger ; Dr.-Ing. Andreas Mühl |
Cooperation: |
Institute of Natural Materials Technology, Processing Machines and Processing Technology (VAT) Prof. Dr.-Ing. Jens-Peter Majschak |
Logline: | Disturbing effects (e.g. vibrations), which depend on the operating speed of the tool, occur repeatedly on machines. In the project, an approach was developed with which these effects could be partially controlled and the operating speeds in several example processes could be significantly increased. |
Problem and Objectives
Processing machines are used for the automated production of mass consumer goods. From an economic point of view, this requires an increase in product output with simultaneous individualization of production. These demands are often met by, on the one hand, increasing the work output rate through efficient use of the machine. On the other hand, the use of servo drives replaces conventional mechanical solutions with easily adaptable and quickly replaceable motion control solutions. The associated reduction in unproductive downtime can increase overall availability.
By increasing the output rate, serveral machine and process behavior as well as their interaction limit the maximum performance of the processing machine, illustrated in Fig. 1 (described in detail in [GKH13]). This often leads to undesirable effects such as unstable processes, decreasing product quality, increased energy consumption, noise, or vibrations. As a result, the increase in the output rate is basically limited to a narrow process window in which the given requirements are met.
In the project, handeling this effects was investigated using the example of conveying small-sized goods like chocolate bars from one rest position to another. Fig. 1 shows a schematic sketch of the transport mechanism used. The working tool, which is designed as a gripper, is moved by a two-dimensional, servo-driven, non-linear kinematics. In each motion cycle, the gripper moves the products from one rest position to the next, in which further processing steps can be carried out (e.g. packaging the bar).
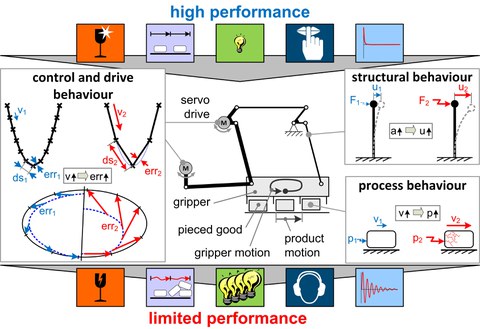
Fig. 1: Reasons for the limited output of processing machines
The following two videos use the example of a conventional bar transportation process to show how the process behavior changes when the operating speed is increased. While the bar is correctly positioned when executed at 1 Hz, execution at 2 Hz is not possible due to the excessive deceleration of the gripper and the associated uncontrolled sliding product.
Vid. 1: Conventional motion approach at 1 Hz (successful)
Vid. 2: Conventional motion approach at 2 Hz (not successful)
In principle, two approaches appear to be suitable for reducing disturbing effects:
- Adaptation of the motion specification to the behavior of the machine by taking relevant, output-rate-dependent effects into account in the motion design.
- Behavior-optimized system design in such a way that the effect of relevant, output-rate-dependent effects is reduced, e.g. by optimizing the structure (e.g. lightweight construction, mass balancing), the motion control, or the process.
These approaches not only allow increasing the operating speed of the conventional process solution, they also form a basis for developing alternative process solutions with which an even higher performance potential can be achieved.
Operating-Speed-Dependent Motion Processing Approach
An approach was developed and verified which is based on three basic ideas (see Fig. 2). The aim is to increase the output rate and thus increase the productivity of the processing machine by exploiting previously unused potential of servo drives.
- Use of extended behavioral models in the design and optimization of the tools motion. For this purpose, the concept of a novel model-based optimization approach was developed and exemplarily implemented at the Chair of Processing Machines and Processing Technology (VM/VAT). In the approach, the operating speed dependent system behavior is modeled. This is particulary importend for ability to increase the operating speed.
- The motion profiles optimized for selected output rates are combined into a characteristic map of operating-speed-dependent motion profiles. When executing one operating speed, an optimal suitable motion profile is calculated and processed. This takes advantage of the fact that with modern servo drives, it is very easy to vary the motion specifications even during operation.
- Since such an approach has not been pursued in conventional motion control systems so far, the required extended control functionalities have been developed and verified. This was the focus of work at the Institute of Machine Tools and Control Engineering (IWM).
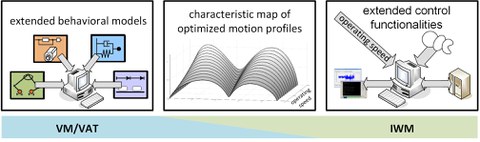
Fig. 2: Basic idea of the novel motion processing approach for the implementation of model-based motion planning
Results and Verification
Processing output-rate-dependent motion profiles
The advantage of output-rate-dependent motion specifications was demonstrated using the example of the grippers positioning error [HKI17]. If a positioning error of the gripper (measured at the motor shaft) of 35 µm is allowed within the overall motion, an output rate of 1.4 Hz is permissible in the conventional process (Fig. 3). By using further, optimized motion specifications, the permissible output rate could be increased by 171 % to 3.8 Hz.
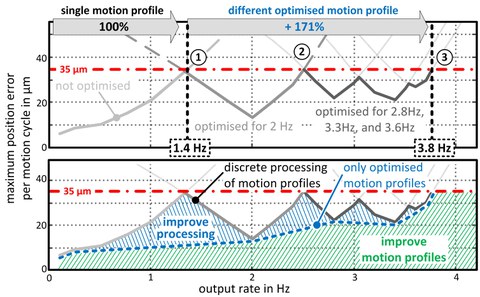
Fig. 3: Output increase of 171% with output-rate-dependent motion profiles [HKI17]
It was experimentally proven that the accuracy can be significantly increased with little effort by improving the execution of the characteristic map of operating-speed-dependent motion profiles. When using linear interpolation between neighboring motion presets, an accuracy increase of 31% could be achieved, Fig. 4.
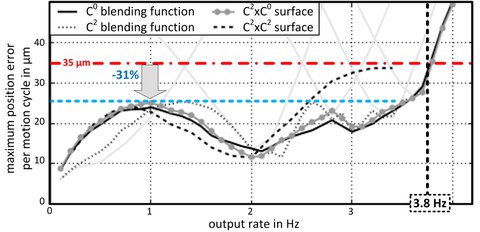
Fig. 4: Improvement of motion accuracy by 31% through continuous processing [HKI17]
Synthesis and application of optimized motion profiles
For the practical implementation of output-rate-dependent motion profiles, the conventional transportation approach (see Vid. 1) was modified in such a way that the product is accelerated by one tine of the gripper. At t1, the gripper decelerates and the product detaches from the comb and slides freely over the ground. Finally, the comb is accelerated again (t2) and the second tine catches the product (t3) and decelerates it to the final position [TSM+18a], Vid. 3.
Vid. 3: Novel model-based motion approach for the product transport at 3 Hz
To implement this transport approach, optimal trajectories must be calculated for each output rate, taking into account the process behavior. For this purpose, a template of the velocity profile (see Fig. 5, a) was designed. Its free parameters were determined within the optimization for the process behavior of the given operating speed.
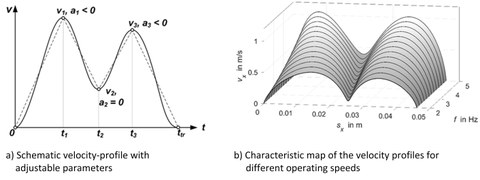
Figure 5: a) Calculation of the velocity profile for the transport phase and b) characteristic map of operating-speed-dependent motion profiles. Adapted from [TSM+18a]
Using this motion specification, the machine speed has been increased up to 5 Hz (see Vid. 4 and 5).
Vid. 4: Novel model-based motion approach at 5 Hz
Vid. 5: Novel model-based motion approach at 5 Hz (real time)
Experimentally, it has been investigated which processing strategy should be used when implementing the optimized motions. Therefore, different strategies were implemented with the same characteristic map of operating-speed-dependent motion profiles. The products positioning error of less than 0.5mm was used as the quality criterion that must be met (see Fig. 6). It becomes clear that the continuous processing provides better results by up to 84% compared to the discrete processing. Using the novel approach, the positioning error never exceeds 0.5mm in the operating speed range between 2Hz and 5Hz.

Fig. 6: Measurements of the positioning error of the workpiece for different processing strategies. Shown are the measuring results from [TSM+18b], Figure 11 and 12.
Further Control Functionality
To monitor the process at high operating speeds and avoid collisions, additional process control functions were implemented and evaluated. On the one hand, a position control of the piece goods was implemented using photogrammetric measurements (see Vid. 6). Here, markers are used to detect the position of the product at its rest positions. In case of a deviation, an emergency stop is executed.
Due to the high measurement effort as well as the high costs of high-speed cameras, a simpler solution of process control was implemented for the purpose of comparison. In this solution, much cheaper photoelectic sensors have been used to mointor the target position of the products (see Vid. 7).
This approach works just as robustly and quickly as photogrammetric measurement and is comparatively less expensive. On the other hand, it has disadvanteges concerning its fixed position in the machine. Changing the location the location to be monitored always involves a mechanical change and corresponding intervention.
Publications
[HDM11] Holzweißig, J. ; Döring, M. ; Majschak, J.-P. : Simulation und modellbasierte Optimierung von Bewegungsvorgaben zum Transport granulatgefüllter Behälter in Verarbeitungsmaschinen. Vortrag zur VDI/VDE-Tagung Antriebssysteme 2011. Nürtingen 09/2011, S. 171–182
[DTM12] Döring, M. ; Tietze, S. ; Majschak, J.-P. : Methodenvergleich zum Bewegungsdesign in schnelllaufenden Verarbeitungsmaschinen am Beispiel eines Siegelbackenantriebes mit elastischer Antriebsanbindung. Vortrag zur 16. VDI-Getriebetagung Bewegungstechnik 2012. Nürtingen 09/2012, S. 115–131
[DMHG12] Döring, M. ; Majschak, J.-P. ; Holowenko, O. ; Großmann, K. : Grundlagenunter-suchung zur modellbasierten Bewegungsplanung. In: Tagungsband Fachtagung Verarbeitungsmaschinen und Verpackungstechnik VVD 2012, Dresden. Tagungsband VVD2012 Praxis trifft Wissenschaft. Selbstverlag der TU Dresden 2012, S. 135–148
[DM13] Döring, M. ; Majschak, J.-P. : Berechnung von Bewegungsvorgaben unter Beachtung der Prozessdynamik am Beispiel des schnelllaufenden Transports von kleinformatigen Stückgütern. Vortrag zum 10. Kolloquium Getriebetechnik 2013. Ilmenau 09/2013, S. 187–200
[GKH12] Großmann, K. ; Kauschinger, B. ; Holowenko, O. : Hochdynamische Bahnvorgaben an Verarbeitungsmaschinen effizient abarbeiten. In: Tagungsband sps ipc drives, VDE Verlag, Berlin, Offenbach, 2012, S. 205–214
[GKH13] Großmann, K. ; Kauschinger, B. ; Holowenko, O. : Effiziente Abarbeitung hoch dynamischer Bewegungen. Teil 1: Umsetzung eines Steuerungsansatzes zur effizienten Abarbeitung taktratenabhängiger Bewegungen an Verarbeitungsmaschinen, In: ZWF 108 (2013), Nr. 7–8, S. 498–503, DOI: 10.3139/104.110972
[GKRH13] Großmann, K. ; Kauschinger, B. ; Riedel, M. ; Holowenko, O. : Effiziente Abarbeitung hoch dynamischer Bewegungen. Teil 2: Vorteile und Grenzen beim Einsatz takt-ratenabhängiger Bewegungen an Verarbeitungsmaschinen, In: ZWF 108 (2013), Nr. 9, S. 664–669, DOI: 10.3139/104.110997
[GHR15] Großmann, K. ; Holowenko, O. ; Riedel, M. : Photogrammetrische Bahnvermessung an einer schnelllaufenden Verarbeitungsmaschine. In: Tagungsband der Fachtagung Verarbeitungsmaschinen und Verpackungstechnik VVD 2015 – Praxis trifft Wissenschaft. – ISBN 978-3-86780-430-1, 2015, S. 145–158
[GT17] Golle, C. ; Troll, C. : Mehrkörpersimulation eines ebenen Koppelgetriebes mittels Matlab/ADAMS-Co-Simulation. In: Tagunsband SAXSIM –SAXON SIMULATION MEETING. – ISBN 978-3-96100-011-1, 2017
[HKI17] Holowenko, O. ; Kauschinger, B. ; Ihlenfeldt, S. : Increasing the Performance of Processing Machines by Executing Output Rate Dependent Motion Profiles. In: International Journal of Automation Technology 11 (2017), Nr. 2, S. 165–170, DOI: 10.20965/ijat.2017.p0165
[TSM+18a] Troll, C. ; Schebitz, B. ; Majschak, J.-P. ; Döring, M. ; Holowenko, O. ; Ihlenfeldt, S. : Commissioning new Applications on Processing Machines. Part I: Process Modelling. In: Advances in Mechanical Engineering 10 (2018), Nr. 2, S. 1–12, DOI: 10.1177/1687814018754953
[TSM+18b] Troll, C. ; Schebitz, B. ; Majschak, J.-P. ; Döring, M. ; Holowenko, O. ; Ihlenfeldt, S. : ommissioning new Applications on Processing Machines. Part II: Implementation. In: Advances in Mechanical Engineering 10 (2018), Nr. 2, S. 1–11, DOI: 10.1177/1687814018754955
[TMHI19] Troll, C. ; Majschak, J.-P. ; Holowenko, O. ; Ihlenfeldt, S. : Anwendung prozessorientierter und taktratenabhängiger Bewegungen in Verarbeitungsmaschinen. In: Gössner, S. (Hrsg.): 13. Kolloquium Getriebetechnik. Berlin : Logos Verlag, 2019. – ISBN 978-3-8325-4979-4, S. 249–268 Volltext
[HDI20] Holowenko, O. ; Drowatzky, L. ; Ihlenfeldt, S. : Performance Evaluation of Offline Motion Preparation Approaches on the Example of a Non-Linear Kinematics. In: Applied Sciences 10 (2020), Nr. 22, 8014, DOI: 10.3390/app10228014
[HTIM21a] Holowenko, O. ; Troll, C. ; Ihlenfeldt, S. ; Majschak, J.-P. : A Novel Adaptive Interpolation Approach for the Implementation of Operating-Speed-Dependent Motion Profiles in Processing Machines. In: Engineering Science and Technology, an International Journal 24 (2021), Nr. 6, S. 1308–1317 DOI: 10.1016/j.jestch.2021.03.007
[HTIM21b] Holowenko, O. ; Troll, C. ; Ihlenfeldt, S. ; Majschak, J.-P. : Combining the Advantages of Different Processing Solutions Using a Novel Motion Processing Approach. In: Applied Sciences 11 (2021), Nr. 21, 10238 DOI: 10.3390/app112110238
Contact
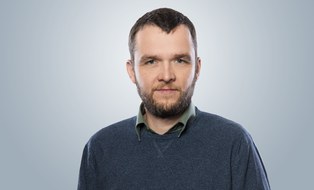
PhD candidate
NameMr Dipl.-Ing. Olaf Holowenko
Process Informatics and Machine Data Analysis
Send encrypted email via the SecureMail portal (for TUD external users only).
Chair of Machine Tools Development and Adaptive Controls
Visiting address:
Kutzbach-Bau, Room E6 Helmholtzstraße 7a
01069 Dresden