Increase in static friction of clamping discs (rotary table clamping)
Table of contents
Important data at a glance
Project titel: | Increase in static friction of clamping discs (rotary table clamping) |
---|---|
Duration: | 10/2019 – 06/2022 |
Collaborative project: | yes |
Funding: |
Förderung der Industriellen Gemeinschaftsförderung |
Funding code: | IGF 20 839 BR |
Processor / Contact person: | Dipl.-Ing. Richard Zschech |
Cooperation: | VDW – AK 5, Fraunhofer-Institut für Werkzeugmaschinen und Umformtechnik IWU |
Logline: | Together with the Fraunhofer IWU, an attempt is being made to increase the static friction values of clamping discs through targeted surface manipulation and design. |
Objective
Motivation
For the multi-sided, 4- and 5-axis, machining of workpieces, rotary tables are usually used (see Fig. 1, left). These allow the workpieces to be continuously rotated or, in conjunction with a swivel axis, to be rotated and swiveled and thus to perform interpolating machining in the available spatial degrees of freedom of movement. However, the feed forces and torques that can be realized in this process are limited by the drive systems used for the rotary tables. For heavy-duty machining in combination with swivel axes and to meet safety requirements, rotary tables have clamping units. These prevent the table from rotating even under the highest process loads by means of frictional clamping and also enable emergency braking in the event of a fault.
Solution approach
Due to increased demands on machine tools, leading equipment manufacturers require innovations in the design of current clamping systems to improve system characteristics at neutral or reduced manufacturing costs. The aim of the project is to achieve a further increase in static shear forces in general and, in particular, in clamping torques on rotary tables of machine tools by increasing the attainable coefficient of static friction μ0 and by minimizing the coefficient of friction window (variation in the coefficient of static friction μ0).
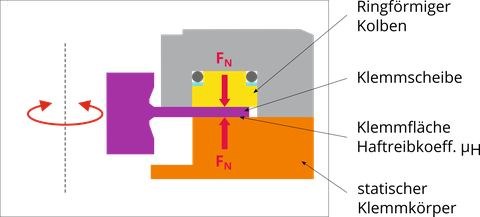
Fig. 1: Schematic structure of a rotary table clamping system
Solution
The approach in the project is divided into two pillars - the consideration of the static friction effective area (here model area 30 mm x 30 mm) and the consideration of the overall clamping unit system (in the equivalence test rig) - with both pillars interacting closely. The project aims at a broad simulative and experimental evaluation of the developed technologies to increase the static friction coefficient and performs iterative optimizations. Using simulation-based methods, new material and surface combinations for targeted friction coefficient increase are investigated (WP1.1) and qualified in terms of manufacturing technology (WP1.2). On the basis of the extensive provision of samples of the newly developed model surfaces, basic tribological investigations (WP1.3) and endurance tests (WP2.3) will then be carried out for selected friction pairings. The latter are additionally optimized in each case with regard to their macro shape and in particular the contact ratio with the models developed in WP2.1 (WP2.2). Based on the results obtained at the equivalence test stand (WP2.3), these simulation models will be further developed and improved (WP2.1). An economic feasibility study (AP3) shows the potential of an industrial implementation.
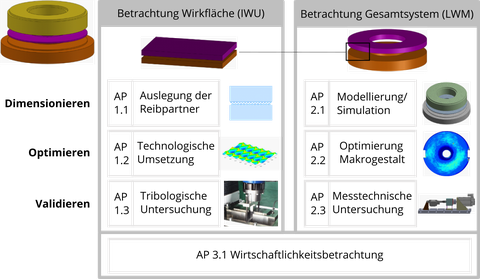
Fig. 2: Project structure
Built-up trainer
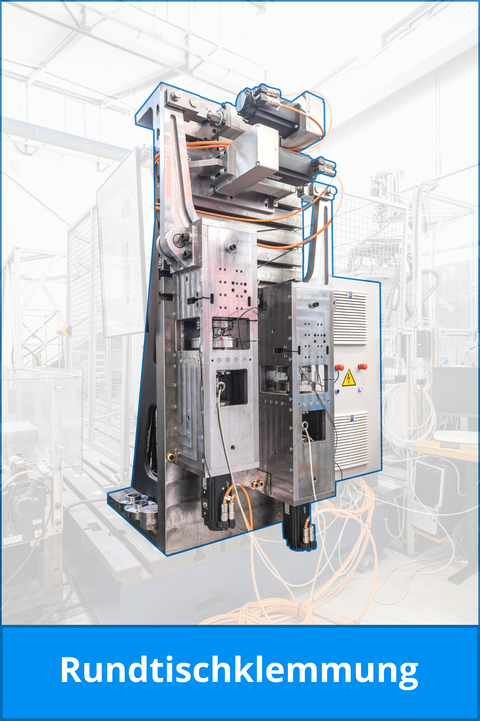
Fig. 3: Built-up trainer with two test objects
Real test site
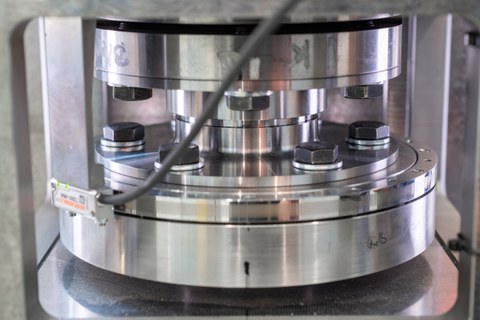
Fig. 4: Real effective site with two clamped specimens in engagement
Functionality
Vid. 1: Schematic diagram of a typical measurement cycle © LWM / TU Dresden
Trainer in action
Vid. 2: Real-time recording of the real test rig during a typical measurement cycle © LWM / TU Dresden
Contact
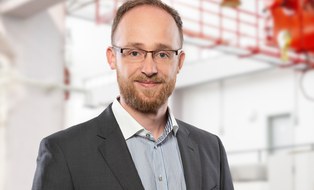
Research associate
NameMr Dipl.-Wirt.-Ing. (BA), Dipl.-Ing. Richard Zschech
Control and Feedback Control Systems
Send encrypted email via the SecureMail portal (for TUD external users only).
Chair of Machine Tools Development and Adaptive Controls
Visiting address:
Kutzbach-Bau, Room 203 Helmholtzstraße 7a
01069 Dresden