ReHoAkt I
Inhaltsverzeichnis
Wichtige Daten im Überblick
Projekttitel: | ReHoAkt I – Regelbare FGL-Hochlastaktorik für die automatisierte Feinjustierung von Maschinenkomponenten und Großbauteilen |
---|---|
Laufzeit: | 05/2019 – 10/2020 |
Verbundvorhaben: | ja |
Teilprojekttitel: | FGL-Aktorsimulation, Messsystementwicklung und simulations-gestützte Ausrichtprozedurentwicklung für Großbauteile und Maschinenkomponenten |
Finanzierung: | PTJ, BMBF zwanzig20 |
Förderkennzeichen: | 03ZZ1040A |
Bearbeiter: | |
Kooperationspartner: |
Fraunhofer IWU LWW, TU Chemnitz Feinmechanisches Fertigungszentrum Glashütte GmbH FFZ Dr. Matzat & Co. GmbH A.S.T. – Angewandte System Technik GmbH, Mess- und Regeltechnik watttron GmbH |
Logline: | Entwicklung von Verfahren zur Feinjustage von Großbauteilen und Maschinenkomponenten mittels ebenfalls zu entwickelnden Formgedächtnis-Hochlast-Aktoren sowie unter Nutzung von strukturintegrierter Kraftmesstechnik. |
Zielstellung
Motivation
Sowohl bei der Montage und Inbetriebnahme als auch für den Betrieb von Werkzeugmaschinen (WZM) bestehen sehr hohe Anforderungen hinsichtlich der Vermessung und Ausrichtung bzw. Positionierung von Baugruppen, wie z. B. Führungen, Spindeln, Lagern und Antrieben. Auch die spanende Bearbeitung großer Werkstücke erfordert zeitintensive Ausrichtvorgänge. Insbesondere bei sehr präzisen und hochwertigen Großbauteilen wird teilweise mehr Zeit für das Ausrichten benötigt als für die Bearbeitung des Werkstücks selbst [1]. Bei der Feinjustierung von Maschinenkomponenten und Großbauteilen besteht zudem eine große Abhängigkeit von dem Fachwissen und den Fähigkeiten des Personals. Somit ergibt sich durch die Feinausrichtung von Maschinenkomponenten bei der Erstinbetriebnahme, beim Retrofit bzw. der Reparatur von Maschinen sowie bei der Feinjustierung großer Werkstücke ein hoher Wertschöpfungsanteil.
Lösungsansatz
Ziel des Vorhabens ist es, Justageprozesse von Werkstücken und Maschinenkomponenten mit Formgedächtnisaktorik zu automatisieren und damit deutlich zu verkürzen. Um eine zeit- und kosteneffiziente sowie bedienerunabhängigere Ausrichtung von Maschinenkomponenten und Großbauteilen zu erlauben, sind regelbare Hochlastaktoren auf Basis von Formgedächtnislegierungen (FGL) zu entwickeln und experimentell zu untersuchen (Basistechnologieentwicklung). Die im Verbundvorhaben entwickelte laufwagenintegrierte Kraftsensorik soll genutzt werden, um die PSF verspannungsarm auszurichten.
Herausforderungen
Die wissenschaftlich-technischen Herausforderungen lassen sich in zwei Schwerpunkte gliedern: die Aktorentwicklung und die Automatisierung von Justageprozessen.
- Im Bereich der Aktorentwicklung müssen Detaillösungen für FGL-Aktorik, Sensorik und Ansteuerung für die spezifischen Anforderungen der gewählten Beispielanwendungen erarbeitet werden. Dies umfasst die Auslegung, Gestaltung und Konstruktion aller relevanten Aktorbestandteile / -baugruppen. Insbesondere die Rückstellung des Aktors in seine Ausgangslage bzw. -länge stellt dabei auf Grund der hohen erforderlichen Kraft eine Herausforderung dar. Zudem erschwert das nichtlineare und hysteresebehaftete Umwandlungsverhalten des FG-Materials das Erreichen einer hohen Stellgenauigkeit.
- Kern des zweiten Schwerpunktes ist die Entwicklung von Methoden zur automatisierten Feinjustage von Profilschienenführungen mittels FGL-Hochlastaktoren sowie unter Nutzung strukturintegrierter Kraftmesstechnik. Erforderlich sind hierfür die modellbasierte Konzeptentwicklung, die messtechnisch gestützte Stellgrößenberechnung, die Erstellung der Aktoransteuerung sowie die Qualifizierung der Sensorsignale der laufwagenintegrierten Messtechnik auf Basis von Dehnmessstreifen.
Lösungsweg
Zur Definition der Anforderungen an den Aktor wurden experimentelle Voruntersuchungen durchgeführt. Hierfür wurde eine Versuchseinrichtung konstruiert und aufgebaut. Eine Kraftmessdose erfasste die beim Positionieren einer verschraubten Profilschiene auftretenden Stellkräfte. Variiert wurden dabei die Vormontagemomente der Schrauben, die Profilschienenbaugröße und die Oberflächengüte der Montagefläche.
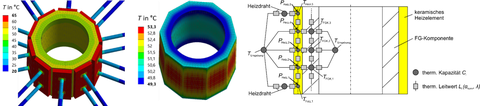
Abb. 1: FE-Simulation des hohlzylinderförmigen FG-Aktors mit Heizelementen und -drähten (links), zugehöriger Temperaturgradient im FG-Element (Mitte) und entsprechendes Netzwerkmodell (rechts)
Basierend auf den zuvor vom LWM ermittelten Anforderungen an Stellweg und Stellkraft erarbeitete der Projektpartner IWU ein Konzept eines FGL-Hochlast-Aktors. Die erreichbare Stelldynamik des thermisch aktivierten Aktors wird wesentlich von der Geometrie der Formgedächtniskomponente sowie deren thermischen Isolation bestimmt. Zur Auslegung und Dimensionierung der Geometrien erstellte das LWM ein Wärmeleitungsmodell. Als Ansatz wurde die Finite-Differenzen-Methode gewählt. Mit diesem Ansatz und einer geeigneten örtlichen Modell-Diskretisierung konnten die Voraussetzungen für eine recheneffiziente und echtzeitfähige Implementierung bei der späteren Verwendung in einer modellbasierten Steuerung geschaffen werden. Das Modell wurde an Hand thermografischer Untersuchungen parametriert.
Außerdem wurden unter Verwendung dieses Modells zwei Konzepte zur Erzeugung verschieden großer Aktor-Stellwege verglichen. Ein monolithischer Aufbau der Formgedächtniskomponenten (FGK) erfordert eine höhere Regelgenauigkeit der Temperatur der eingesetzten Heizelemente. Dafür ist dieser wesentlich kleiner als ein geteilter Aufbau aus einzelnen diskret aktivierbaren Elementen, welcher eine ausreichend gute thermische Isolation zwischen den einzelnen Elementen erfordert. Durch die zusätzlichen Isolationsschichten ist der Aufbau zudem deutlich nachgiebiger.
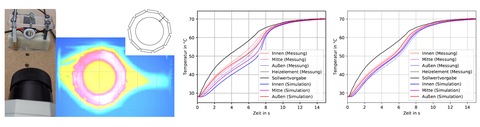
Abb. 2: Abgleich des thermischen Verhaltens der FG-Komponente: Messaufbau und Thermobild (links) sowie Temperaturverläufe über dem Querschnitt vor (Mitte) und nach dem Modellabgleich (rechts)
Neben der Mechanik und den Stellgliedern ist die Steuerung ein wesentlicher Bestandteil regelbarer Aktoren. Die Formgedächtnislegierung weist mit ihrem hysteresebehafteten, stark nichtlinearen Verhalten ungünstige Eigenschaften für das Erreichen der angestrebten Aktor-Stellgenauigkeit mit konventioneller Regelungstechnik auf. Daher verfolgte das LWM den Ansatz einer modellbasierten Steuerung. Hierfür wurde ein Materialmodell erstellt, welches die Hysterese der Phasenumwandlung des Gefüges durch ein Modell mit Preisach-Gedächtnis abbildet. Das Modell berücksichtigt außerdem die Abhängigkeit diverser Materialparameter von den Zustandsgrößen der Legierung. Es wurde mittels Versuchsdaten verschiedener werkstoffwissenschaftlicher Untersuchungen des Partners LWW parametriert. Anschließend wurde das Materialmodell mit dem oben beschriebenen Wärmeleitungsmodell und einem mechanischen Modell gekoppelt, um die bestehenden Wechselwirkungen abbilden zu können.
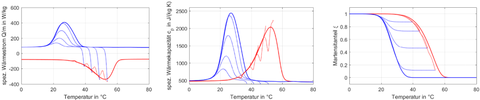
Abb. 3: Wärmestrommessung (links) und daraus berechnete Wärmekapazität (Mitte) sowie mittels Materialmodell berechneter Martensitgehalt (rechts) für unterschiedliche Hystereseschleifen
Mit dem Ziel, die erreichbare Stellgenauigkeit des Aktors zu verbessern, befasste sich das LWM mit Möglichkeiten zur wirkstellennahen Erfassung seiner Stellbewegung. Auf Grund der thermischen Aktivierung der FGL war eine relevante Temperaturerhöhung im Sensor zu erwarten. Starke Temperaturänderungen wirken sich ohne geeignete Gegenmaßnahmen zumeist negativ auf die Messgenauigkeit von Positionssensoren aus. Zur Abschätzung des Einflusses wurde eine simulationsbasierte Untersuchung der Temperaturentwicklung durchgeführt.
Für das verspannungsarme Ausrichten entwickelte der Projektpartner A.S.T. GmbH eine laufwagenintegrierte Kraftmesstechnik. Zur Unterstützung des Partners bei deren Auslegung wurden die wichtigsten Anforderungen aus den vorgesehenen Einsatzfällen der Sensorik abgeleitet. Daneben erstellte das LWM Möglichkeiten, um die durch den Partner A.S.T. GmbH aufgebaute Kraftmesstechnik über die Verwendung während der Montage der Profilschienen hinaus auch während des Betriebs der Vorschubachse zu nutzen.
Zur Entwicklung der Ausrichtverfahren wurden verschiedene Ansätze konzipiert und hinsichtlich ihres technischen Aufwandes, des erreichbaren Automatisierungsgrades sowie der Stellgenauigkeit verglichen. Zur Abschätzung der erreichbaren Stellgenauigkeit wurden Simulationsmodelle in der Multi-Domain-Umgebung Simulink® erstellt und mit diesen Stell- und Ausrichtvorgänge simuliert.
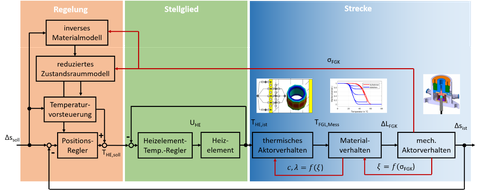
Abb. 4: Blockschaltbild mit dem Regelungskonzept unter Berücksichtigung der Streckencharakteristik
Die Ausrichtverfahren sollten das zuvor entwickelte FGL-Aktor-Konzept nutzen, um die Stellbewegung zu erzeugen. Für die Erstellung der notwendigen Mechanik wurde ein systematischer Konstruktionsprozess durchlaufen. Dabei mussten insbesondere die beengte Einbausituation sowie die Empfindlichkeit der Formgedächtniskomponente gegenüber ungleichmäßiger Belastung beachtet werden. Für die Führung der Stellbewegung wurden verschiedene Prinzipien verglichen. Es konnte keine eindeutige Vorzugslösung identifiziert werden. Daher wurden schließlich zwei Varianten konstruiert. Die Geometrie dieser Ausrichtmodule wurde mittels der Methode der finiten Elemente untersucht. Ziel war es, einen guten Kompromiss zwischen Steifigkeit und Größe zu ermitteln.
Ergebnisse
Mit Abschluss des Projektes liegt ein zusammen mit den Projektpartnern entwickelter Prototyp eines FG-Hochlast-Aktors vor. Der Prototyp erfüllt die gestellten Anforderungen an Hub (>200 µm) und Stellkraft (>10 kN) und ist hinsichtlich seiner Stelldynamik optimiert. Für dessen Ansteuerung ist ein Konzept für eine modellbasierte Regelung vorhanden, welches auf umfangreichen und abgeglichenen Thermik-, Material- und Mechanikmodellen basiert.
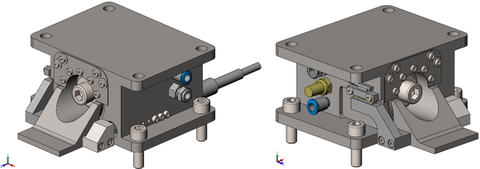
Abb. 5: Hochlast-Aktor Prototyp 1; links: Perspektive von rechts; rechts: Perspektive von links
Zudem stehen im Ergebnis des Projektes dem LWM mehrere Verfahren sowohl für das geometrische als auch für das verspannungsarme Ausrichten der Profilschienenführungen von Vorschubachsen zur Verfügung. Die Verfahrensvarianten unterscheiden sich bezüglich der Art und Menge der erforderlichen Vorrichtungen, den Anforderungen an die Einbauumgebung zur Montage der dieser Vorrichtungen sowie dem durch ihnen erreichbaren Grad der Automatisierung.
Zur Erzeugung der Stellbewegung sehen die Verfahren ein Ausrichtmodul vor, welches das zuvor entwickelte FG-Hochlast-Aktor-Konzept integriert. Mit Abschluss des Projektes liegen zwei Konstruktionen des Ausrichtmoduls vor (vgl. Abb. 5 und Abb. 6). Sie sind durch eine geeignete Geometrie und auf Grund der mit ihnen erzeugbaren Kräfte für das Ausrichten von drei Profilschienenbaugrößen einsetzbar. Weiterhin wurde der günstigste Ort zur Stellwegerfassung identifiziert, um Messfehler in Folge last- und temperaturbedingter Verformung zu reduzieren. Die Abmessungen der ersten Variante des Ausrichtmodules betragen 118x60x134 mm³, die der zweiten Variante 118x80x189,5 mm³.
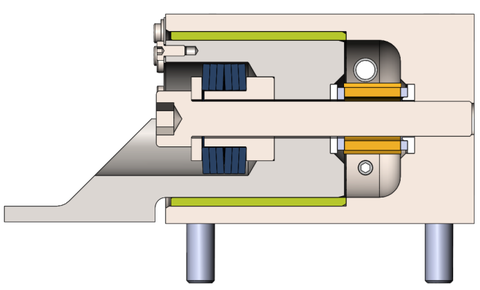
Abb. 6: Schnittansicht Hochlast-Aktor Prototyp 1 (von rechts) mit Formgedächtniskomponente (orange), Tellerfedern (blau) und Gleitlager (grün)
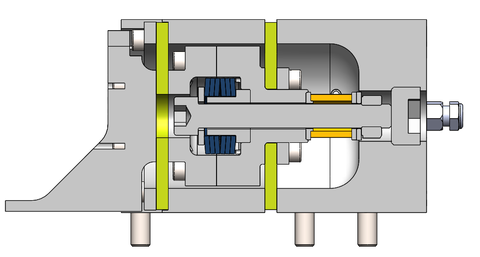
Abb. 7: Schnittansicht Hochlast-Aktor Prototyp 2 (von rechts) mit Formgedächtniskomponente (orange), Tellerfedern (blau) und Membranfedern als Lager (grün)
Für die Nachnutzung der Kraftmesstechnik wurden die Prozesslastberechnung sowie die Überwachung möglicher Schädigungen der Profilschienenführung als attraktive und umsetzbare Anwendungen identifiziert.
Veröffentlichungen
[1] Bimatec, S. : Vollintegriertes 3D-Vermessungssystem. In: MAV: Innovation in der spanenden Fertigung (2015), Nr. 6, S. 112
Kontakt
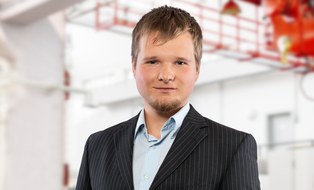
Wissenschaftlicher Mitarbeiter
NameHerr Dipl.-Ing. Ludwig Leser
Antriebs- und Steuerungstechnik
Eine verschlüsselte E-Mail über das SecureMail-Portal versenden (nur für TUD-externe Personen).
Professur für Werkzeugmaschinenentwicklung und adaptive Steuerungen
Professur für Werkzeugmaschinenentwicklung und adaptive Steuerungen
Besuchsadresse:
Kutzbach-Bau, Raum 203 Helmholtzstraße 7a
01069 Dresden