Development of the induction sealing technology for food packaging
For joining thin packaging materials, heating by thermal contact is the most commonly used process (heat conductive sealing). In this process, heat is transferred into the packaging material from outside via sealing jaws. This technique requires a high energy input. Furthermore, the required high thermal mass of the sealing jaws causes a slow control behavior in relation to the cycle times.
A large number of packaging, such as coffee packaging, has an induction-capable layer due to its multi-layer structure. This circumstance is used to establish a new type of technology in food technology and similar industries. Induction sealing is to be developed for packaging materials with a corresponding composite structure. Inductive heating and sealing has several advantages, in particular
- much higher energy efficiency compared to heat contact sealing
- Targeted, effective heat input close to the point of action
- Product protection through targeted, low heat input
- short control cycles
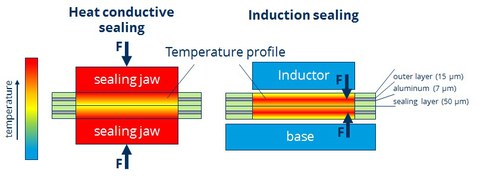
Heat conductive sealing and induction sealing in comparison
For the sealing of food packaging, the dynamics of inductive heating of thin layers as well as the effective energy input close to the point of application place new demands on the packaging material. In order to develop a sealing process without damaging the packaging material or the packaged goods, the interaction of the heating of the induction layer and the sealing layer as well as the possibilities to apply the necessary sealing force have to be investigated.
The aim of the project is the development of an induction sealing technology for the food packaging sector, an associated air-cooled inductor including frequency generator with an adapted power range below 1 kW and an effective frequency range above 1 MHz, as well as the investigation of the process parameters with regard to quality-conforming seals.
Project funding:
The cooperation project ZF4100941WZ9 is part of the program "Zentrales Innovationsprogramm Mittelstand (ZIM)”.
Project duration: 07/2019 – 08/2021
Project management and contact:
Project leader: Prof. Majschak
Project manager: Jürgen Oberer
Cooperation partner: Steremat Induktion GmbH