Building design
Table of contents
(Text by David Sandmann and Silke Scheerer)
The CUBE
The research building with a floor area of 24.1 m × 7.8 m consists of three main parts: the BOX, the two TWIST elements including cantilevered wings and a steel and glass façade.
The TWIST shells made of almost white carbon-reinforced concrete, which are up to 6.8 m high and 32.0 m long and constructed using the in-situ concrete method, are decisive for the design. Thand twisted in ree TWIST shells are geometrically identical. Together with the continuous rooflight, they form the roof and also parts of the outer shell due to their twisting from horizontal to vertical. The wings reach approx. 8.0 m beyond the base of the building and are only 6.0 cm thick at their outer ends.
The TWIST shells surround the cuboid, two-storey (semi-)prefabricated BOX complex made of dark-colored carbon-reinforced concrete. The BOX is approximately 10.7 m long, 4.9 m wide and 6.8 m high. It consists of 25 semi-precast walls, ten parapet elements, nine hollow-core precast ceilings and two stairs. The components were joined together on site using in-situ concrete to form a load-bearing structure.
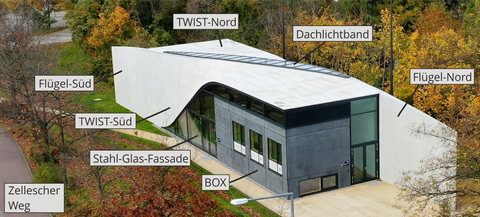
Main structural parts of the CUBE
A particular challenge was the submission of planning that could be approved, as there were no valid standards or approvals for almost all components and many materials, or there were significant deviations from already approved products or types of construction. For these construction products and technologies, approvals in individual cases (in German: Zustimmung im Einzelfall, ZiE) and project-related type approvals (in German: vorhabenbezogene Bauartgenehmigungen, vBG) had to be obtained from the State Office for Building Technology (Leipzig) in accordance with the Saxon Building Code.
BOX building section
The BOX demonstrates the general suitability of carbon-reinforced concrete for prefabricated construction. With a traditional building concept of flat load-bearing elements, a classic assembly construction method with prefabrication, transport and construction site processes was realized. The aim was to achieve resource-efficient, economical, simple and efficient construction.
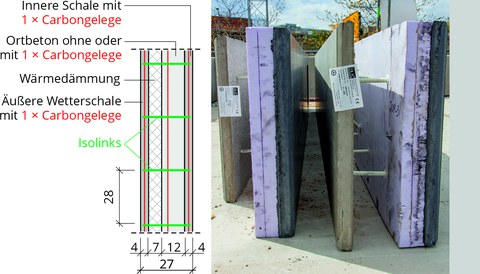
Basic wall construction (left) and semi-finished parts before assembly (right)
The building is founded on thermally insulated strip foundations and base slabs. For the BOX walls, semi-finished parts were produced as double wall elements with internal thermal insulation. The 4 cm thick, carbon-fiber reinforced outer and inner concrete shells are connected with GRP anchors. The wall core consists of a 7.0 cm thick high-performance aerogel insulation layer on the outer shell and a 12 cm thick filler concrete layer made of normal concrete C35/45.
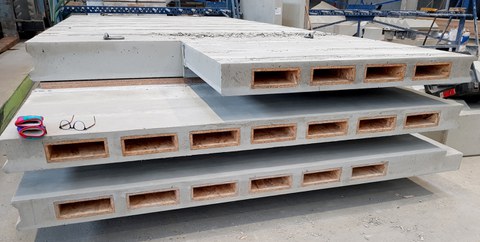
Hollow core slabs of the BOX building section in the concrete plant
The 4.5 m long and up to 2.6 m wide floor slabs are single-axis, fully prefabricated elements. To save material and weight, the planning team opted for a hollow cross-section. The cavities were realized with OSB panels. From a structural point of view, this resulted in multiple, adjacent double-T cross-sections with a construction height of 25.0 cm, composed of slender, carbon-fiber reinforced, horizontal chords just 3.0 cm thick and unreinforced, 6.0 cm thin webs. Compared to a solid concrete slab, more than 50 % concrete could be saved.
As with the walls, a square carbon fiber grid with a reinforcement cross-sectional area of 95 mm²/m and a design tensile strength of 1600 MPa in the main load direction was selected as the single-layer main reinforcement for the BOX ceilings. Compressive strength class C50/60 was selected for the structural concrete.
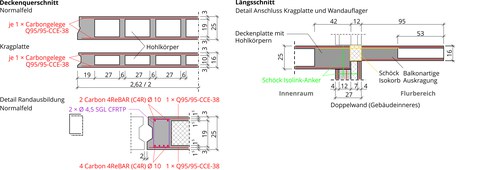
Basic wall construction (left) and semi-finished parts before assembly (right)
The ceiling slabs were connected to each other using joint locks. The floor joints were filled with concrete on site after installation.
TWIST shells
The aim of the concept design by architect Prof. Gunther Henn was to show that carbon-reinforced concrete can be used to build statically efficient and at the same time aesthetically sophisticated and geometrically diverse buildings. The elegantly swinging, playfully twisting TWIST shells with ruled surface geometry rest on a steel column and beam construction or directly on foundations. They form both the horizontal and the vertical space closure of the building and surround the BOX.
The multi-layered cross-section of the TWIST elements is similar to that of the ceilings of the BOX. However, there are no real cavities. Instead, EPS insulation blocks were integrated in order to achieve a load-bearing and at the same time thermally insulating roof-wall construction with as little concrete as possible, which is permanently waterproof and weather-resistant. The overall structure is 44.0 cm high and has three main components: a 25.0 cm thick load-bearing shell, a 15.0 cm thick sealing and insulation layer, and a 4.0 cm thick weather shell as roof cladding and weather protection.
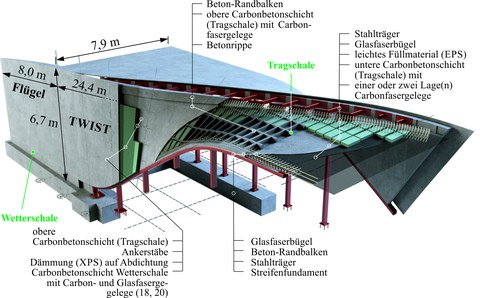
Configuration of the TWIST carbon-reinforced concrete shells
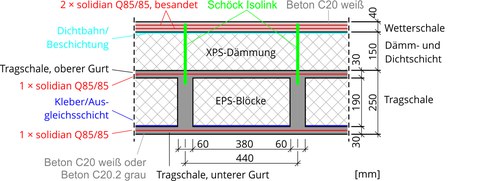
TWIST shell: standard cross-section in longitudinal direction at the time of the ZiE application, load-bearing shell with one layer of carbon-fiber textile
The upper and lower chords of the load-bearing shell are each 3.0 cm thick and reinforced with a single layer of a square carbon fiber grid with a cross-sectional area of 85 mm²/m. In areas of higher bending stress, two layers of the carbon fiber mesh were installed and the chord thickness was increased to 4.0 cm. The chords are connected via 19 cm high unreinforced concrete webs. EPS insulation blocks are arranged in between. These blocks were 3D-milled in accordance with the planning. The blocks' edges were angled to minimize local stress peaks in the areas where the webs connect to the chords. The edges of the load-bearing shell were formed by stiffening edge beams, which were reinforced with non-metallic longitudinal bars and stirrups.
Bituminous waterproofing and a layer of XPS insulation were applied to the load-bearing shell. The final, 4.0 cm thick concrete weather shell, which was reinforced with two layers of the carbon reinforcement, was connected to the load-bearing shell with GRP pins. In order to improve the bond between the textile fiber reinforcement and the concrete while minimizing the expected crack widths and spacing, the carbon reinforcement was additionally sanded. Furthermore, a constructive protective reinforcement made of a glass mesh fabric was installed 5 mm below the surface of the weather shell.
The TWIST shells end with 8 m long wing walls that project beyond the building. They were designed in a similar way to the load-bearing shells of the TWIST. Their thickness decreases from 44.0 cm at the TWIST connections to 6.0 cm at the free ends.
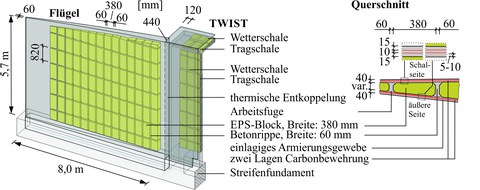
Structure of the wings: 3D view (left) and schematic cross section (right)
The two TWIST elements were produced using the wet spraying method against a one-sided timber formwork made of segmented and lined-up multi-layer panels in accordance with the mathematical set of straight lines that defined the curvature and shape of the control surface. The shotcrete C50/60 with a maximum grain size of 2 mm had to meet the highest exposed concrete quality standards, e.g. with regard to offsets at construction joints, porosity, and uniformity of color. The outer side was smoothed by hand. Finally, the surface was given graffiti protection as impregnation.
Further information
BUST special issue on the CUBE, initiated by Manfred Curbach and Michael Frenzel, edited by Michael Frenzel and Silke Scheerer; published in: Beton- und Stahlbetonbau 118 (2023) S2 CUBE Das Carbonbetongebäude (selection):
- Kupke, M.: CUBE Projektvorstellung. 13–21 – https://doi.org/10.1002/best.202200125
- Frenzel, M.; Scheerer, S.; Schmidt, A.: Übersicht über die im CUBE verwendeten Materialien. 25–36 – https://doi.org/10.1002/best.202200125
- Ritter, H.; Frenzel, M.; Scheerer, S.: Statisch-konstruktive Durchbildung des Gebäudeteils BOX – Herausforderung aus planerischer Sicht. 42–48 – https://doi.org/10.1002/best.202200126
- Frenzel, M.; Schmidt, A.; Scheerer, S.: ZiE für Carbonbetonbauteile in Halbfertigteil- und Fertigteilbauweise im Gebäudeteil BOX des CUBE. 49–56 – https://doi.org/10.1002/best.202200105
- Vakaliuk, I.: Modellierung der TWIST-Schale des CUBE. 66–70 – https://doi.org/10.1002/best.202200104
- Zavadski, V.; Frenzel, M.: Aufbau, Bemessung und Planung der TWIST-Carbonbetonschalen. 71–81 – https://doi.org/10.1002/best.202300009
- Schmidt, A.; Frenzel, M.; Scheerer, S.: Schwinduntersuchungen zu einer fugenlosen 24,4 m langen Carbonbetonschale – ZiE TWIST. 82–91 – https://doi.org/10.1002/best.202200124
- Jesse, F.: Herstellung und Errichtung – TWIST. 109–119 – https://doi.org/10.1002/best.202200096