Research Field "Multiphysical Material Modelling on Multiple Scales"
The description of the multiphysical behaviour of micro-heterogeneous material in general is based on phenomenological modells obtained from experimental observations on the microscale and continuum mechanical considerations. An example is the thermomechanically strongly coupled behaviour of dual phase steels under large plastic deformations. In most cases the goal is to predict the macroscopic behaviour of the micro heterogeneous material or the material behaviour across the scales. To do that, different computational multiscale methods are used and developed at the institute.
Research Projects
Contact:
Tengfei Lyu, Shahbaz Ahmed
Cooperation Partner:
Institut für Kontinuumsmechanik (IKM), Leibniz-Universität Hannover
Abstract:
In metal forming processes a large amount of mechanical work is dissipated due to large plastic deformations. The accompanying temperature rise leads to thermal strains and a change in the material behaviour which can influence the mechanical behaviour during the forming process and the final shape of the part. For this reason it is important to consider temperature effects and heat conduction in the material modelling of the polycrystalline microstructure. The resulting thermomechanical problem exhibits a strong coupling since on the one hand through mechanical deformation heat sources are introduced and on the other hand material parameters may depend on the temperature and also large thermal strains can emerge. Experimentally the temperature influence can be analysed by performing experiments with material specimens at different temperatures. The results can be used to develop a thermomechanical material model for the microstructure. By using homogenisation techniques the macroscopic effective material model developed in period 1 of the CRC/TR73 is extended by temperature effects.
Another critical effect occurring during the forming process is the initiation and propagation of microcracks. This effect leads to a stiffness reduction or even to failure of the entire structure. Therefore it is essential to study the degradation mechanisms of the crystallographic microstructure. A nonlocal damage model is used to account for microcracks. For propagating the crack existing models are extended to nonlinear anisotropic and inelastic materials. Especially a criterion has to be found when cracks collide with grain boundaries. For the case of stable crack growth with a statistical simulation series a representative volume element can be found. This is used to produce a micromechanically motivated stress strain relationship by a homogenisation procedure. With this material response the effective material model of period 1 of the CRC/TR73 is extended. Here it is important to capture the softening effects with a nonlocal damage model. In a last step the two approaches are combined for the construction of a material model capturing thermomechanical effects and cracks on the microstructural level.
Contact:
Samira Hosseini
Cooperation Partner:
Institut für Kontinuumsmechanik (IKM), Leibniz-Universität Hannover
Abstract:
Fiber reinforced plastics are widely used in advanced structures such as aerospace industry, energy and automotive industries. Their advantages over conventional materials are, among others, their higher strength- and stiffness- to- weight ratio, high corrosion resistance and adjustable mechanical properties. However, their application is limited due to different failure mechanisms such as matrix shear failure, delamination, fiber crushing and most importantly, fiber bucking (kinking) under compressive loads. In unidirectional fiber reinforced composites, fiber kinking is known as the most significant failure mechanism since it could lead to abrupt instability of the material and a drop of the load carrying capacity of the structure. Therefore, predicting the compressive strength of the structure depends on predicting the stress state at which fiber kinking happens.
Due to the difference between the size of the engineering component and the microstructure where the fiber kinking happens, using multiscale strategies is necessary. However, fiber kinking is a localised phenomenon, which makes the multiscale methods based on the global-local analysis preferable over homogenisation techniques (based on RVEs) for making an admissible prediction of the failure behaviour.
Hence, the Multiscale Projection Method, which has already been developed for multiscale fracture mechanics, is adapted for fiber kinking problems. In this model we define a small fine scale area in which the microstructure of the composite material (fiber, matrix and their interface) is explicitly represented. The boundary condition for the fine scale computations is applied from the coarse scale solution as displacement values interpolated on the fine scale boundary nodes. The stress and material tangent are projected back from the fine scale to the coarse scale. The debonding between fiber and matrix is simulated using a geometrically nonlinear cohesive element which is compatible with the large rotations happening due to buckling of fibers.
The location of fine scale domain where the fiber kinking is supposed to happen is detected automatically using a proper kinking criterion.
Contact:
Martina Baldrich, Felix Töller
Cooperation Partner:
Institut für Kontinuumsmechanik (IKM), Leibniz-Universität Hannover
Abstract:
The overall objective of the collaborative research center "Tailored Forming" (CRC 1153) is to open up the potential for hybrid solid components on the basis of a new tailored manufacturing process using joined semi-finished products. In contrast to existing manufacturing and production processes of hybrid components, in which the joining process takes place during forming or at the end of the production chain, the tailored semi-finished products used in the CRC 1153 are joined before the forming process. Compared to the existing manufacturing process, the simple geometry of semi-finished products facilitates the handling and the reliable production of a material joining zone. The controlled material flow during the subsequent forming process also opens up completely new design possibilities of the resulting joining zone geometry, which cannot be created by conventional joining techniques. In addition, depending on the material combination, the (thermo-mechanical) forming process is expected to improve the joining quality. Based on different metallic materials it should thus be possible in the future to produce complex high-performance components which are not yet producible according to the current state of the art. The precedent joining process also results in manufacturing advantages. By means of the geometric adjustment of the joined semi-finished products to the final component a predistribution of the material is possible. As a result, the material flow and the process-related burr can be significantly reduced.
The topic of project C4 is the multiphysical modelling and simulation of the microstructural behaviour of the joining zone during the tailored forming process. The goal is the determination of the macroscopic, effective, thermomechanical properties of joining zones during and after forming. The macroscopic material model which is developed here as well as the respective material parameters will be used by other projects within the collaborative research center e.g. for macroscopic forming simulations. One of the difficulties in modelling and simulating the microstructure of joining zones of different materials is the possibly very different behaviour of the joint materials. The joining zones sustain rather complex, strongly coupled mechanical, thermal and chemical influences during the joining and forming processes as well as during heat treatment. Diffusion plays an important role for the cohesion of the materials. On the microstructural level the polycrystalline material of the joining zone is modelled. The model will be able to capture the contact and diffusion processes during joining, the thermal and mechanical properties during forming as well as the material behaviour during heat treatment which is responsible for calibrating material properties. A second goal of the material modelling and simulation is the prediction of the material behaviour and of eigenstresses after forming and in the vicinity of joint surfaces as well as close to machined surfaces. In close collaboration with other projects of the CRC 1153 the material models for the microstructure as well as the macroscopic material models will be validated. On the macroscopic level the material models will be used in a couple of other cooperating projects for forming simulations.
Abstract:
The aim of this work is the development of mechanical models on a mesoscopic level for the analytical description of the material properties of textile reinforced concrete (TRC). For the modelling of the heterogeneous structure of TRC the concept of representative volume elements (RVE) is used. RVEs are representative for the mesoscopic structure. The overall material behaviour on the macroscopic level is obtained by means of homogenisation of the heterogeneous material behaviour on the mesoscopic level.
Based on the micro mechanical solution of the elastic field of an ellipsoidal inclusion according to Eshelby a model for the determination of the material behaviour for multi-directional reinforced finegrained concrete is developed. An effective field approximation considers the interaction of the differentially orientated reinforcements in an averaged sense. Microcracks are included by additional strains in the representative volume element. The average interaction between the microcracks and the reinforcements is considered by an effective field approximation.
As a criteria for the initiation of the macro cracking a critical microcrack density parameter is implemented in the mechanical model. The microcracks accumulate to macrocracks if the microcrack density parameter in the RVE exceeds this critical value. For the mechanical modelling of the bond behaviour between roving and matrix after macro cracking a multiple linear shear stress-slip relation is used. This shear stress-slip relation considers adhesion, damage and failure of the interface between roving and matrix. Hence experimentally measured pullout force-displacement curves can be simulated realistically.
References:
Richter, Mike: Entwicklung mechanischer Modelle zur analytischen Beschreibung der Materialeigenschaften von textilbewehrtem Feinbeton. Dissertation, Institut für Mechanik und Flächentragwerke, Technische Universität Dresden, 2005
Richter, Mike; Zastrau, Bernd: On the Nonlinear Elastic Properties of Textile Reinforced Concrete under Tensile Loading Including Damage and Cracking. Materials Science and Engineering A (422), 2006, S. 278--284
DFG (Deutsche Forschungsgemeinschaft), Sonderforschungsbereich 528: Textile Bewehrungen zur bautechnischen Verstärkung und Instandsetzung
Teilprojekt B6: Übertragungsverhalten von Roving zu Roving und Endverankerung textiler Strukturen
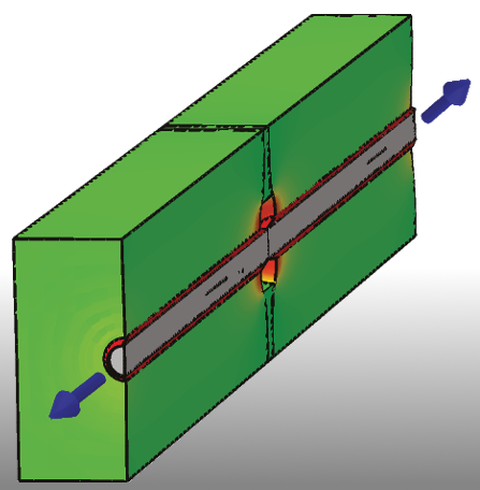
Übertragungsverhalten von Roving zu Roving und Endverankerung textiler Strukturen
Abstract:
The continuum mechanics analysis of load transfer mechanisms between the individual fibers and the matrix and their influence on the overall behavior of textile reinforced concrete (TRC), in addition to determining the required anchoring end lengths of the textile reinforcement. Moreover, the stress transfer and the damage mechanisms in the areas of the overlapping lengths of the fibers are investigated. The analysis of the stress transfers and the damage mechanisms are carried out by means of the continuum mechanics analysis, the numerical simulations, and the fracture mechanics approaches.
Further information can be found in the detailed description
Abstract:
Scope of this work is a unified differential geometric representation of continuum theories and their numerical solution. In course of time and for different reasons, a wealth of continuum theories have been developed that are more or less extensive generalizations compared to classical continuum theories, like, e.g., the theory of elasticity with its three displacement degrees of freedom. By way of example, the Cosserat continuum theory is stated that has besides the three displacement degrees of freedom additionally three rotational degrees of freedom. The theoretical formulation and unification of existing continuum theories are to the fore here, whereby a geometrical approach, i.e., differential geometry, is preferred. The true potential of a continuum theory is revealed by is application, i.e., by the numerical simulation of real problems. This gives reasons, why the numerical solution accomplished here by the finite element method – also in the interaction with the development of the continuum theories – plays an important role.
DFG (Deutsche Forschungsgemeinschaft), Sonderforschungsbereich 528: Textile Bewehrungen zur bautechnischen Verstärkung und Instandsetzung
Teilprojekt A3: Entwicklung konstitutiver Gesetze für Feinbeton mit textiler Bewehrung
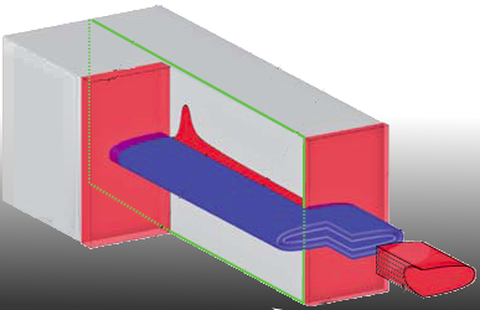
Entwicklung konstitutiver Gesetze für Feinbeton mit textiler Bewehrung
Abstrakt:
Zur mechanischen Beschreibung des Verhaltens des Verbundwerkstoffes Textilbeton ist die Kenntnis der wichtigsten Tragmechanismen nötig. Durch die Bewehrung des spröden Betons mit Endlosfasern (Glas, Carbon, Aramid, ...) wird weniger eine Erhöhung der Steifigkeit des Verbundwerkstoffes erreicht, als vielmehr eine Quasiduktilität erzielt. Dies ist hauptsächlich auf das sukzessiv versagende Interface zwischen Faser und Matrix während der Rissbildung des Betons. Die Beschreibung des Verbundes zwischen Beton und Faserbewehrung ist somit besonders bedeutsam. Mit der Kenntnis der Schubspannungstransfermechanismen und der Versagenskriterien der Einzelwerkstoffe Beton und Faserbewehrung ist unter anderem die Vorhersage von Rissabständen, Rissbreiten, Übertragungslängen und Verankerungslängen im Textilbeton möglich. Ziel des Forschungsvorhabens war es, aus der Kenntnis der Einzelwerkstoffe unter Hinzunahme der Eigenschaften des Verbundes und der Verlegeart der textilen Bewehrung Aussagen sowohl über die Steifigkeitsentwicklung infolge Schädigung des Gesamtmaterials als auch über die Bruchlasten und Versagensformen zu treffen. Diese Kenntnis über das Materialverhalten dient sowohl der Erklärung des Bauteilversagens in bereits durchgeführten Versuchen als auch der Prognose von Versuchsergebnissen.
Umfangreiche Beschreibung der Projektergebnisse in der Detailbeschreibung
Referenzen:
Beyer, F.; Zastrau, B. W. [2012], "Teilprojekt A3: Konstitutive Gesetze", Curbach, M.; Ortlepp, R. (Hrsg.): Sonderforschungsbereich 528 - Textile Bewehrungen zur bautechnischen Versẗärkung und Instandsetzung – Abschlussbericht (gekürzte Fassung), S. 67-73
weitere Referenzen in der Detailbeschreibung
Abstract:
The production of thermally toughened glass often results in the breaking off of the previously cut glass edges or a displacement in laminated glass panes. This results in insufficient optical quality of the glass edge. Perfectly flat surfaces can be formed due to subsequently regrinding of the glass edges, but this process also decreases the thermally induced residual compressive stress. The reduction of strength can only be compensated by an increased edge quality with smaller surface defects.
The aim of the cooperation project is to develop a grinding process that ensures the strength of thermally toughened (tempered) glass. The mechanical modeling and numerical simulation of the structural behavior is done at the Institute of Mechanics. In particular, the material removal at the glass edges due to grinding and its influence on the strength is examined. A numerical simulation considering the quantity of prestressing and the surface damage should allow a mathematical evaluation of the mechanical behavior of tempered glasses with reground edges.
link to research field "Damage and Fracture Mechanics"
link to research field "Numerical Methods"