Forschungsfeld "Schädigungs- und Bruchmechanik"
In den meisten Fällen versagen Bauwerke, Bauteile und Materialien aufgrund von schädigungs- und bruchmechanischen Vorgängen. Dennoch reagieren die meisten Materialien sehr unterschiedlich in ihrem Bruchverhalten. Um Vorhersagen treffen zu können, wann und unter welchen statischen oder zyklischen Beanspruchungen ein Material versagt, sind präzise Modelle und entsprechende numerische Methoden erforderlich. Basierend auf der eXtended Finite Element Methode (XFEM) und geeigneten Materialmodellen werden in diesem Forschungsfeld Methoden entwickelt, um effizient und genau berechnen zu können, wann und wie moderne Materialien brechen.
Forschungsprojekte
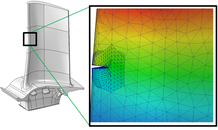
Ansprechpartner:
Jian Sun
Kooperationspartner:
Institut für Kontinuumsmechanik (IKM), Leibniz-Universität Hannover
Abstrakt:
Viele sehr teure Bauteile und Komponenten, wie z.B. Turbinenschaufeln von Flugtriebwerken oder Dieselmotoren von Schiffen oder Lokomotiven sind thermomechanisch sehr stark beansprucht. Im Fall eines Schadens ist aufgrund der Kosten und aufgrund von Umweltaspekten eine Regeneration oft sinnvoll. Diese Regeneration kann Einfluss auf die erneute Rissentstehung und damit die Restlebensdauer des Bauteils haben. Im Teilprojekt C5 des SFB 871 wird ein räumliches und zeitliches Mehrskalenmodell zur Berechnung der Restlebensdauer thermomechanisch hoch beanspruchter Komponenten entwickelt. Die Rissfortschrittsberechnunug im 3D basiert dabei auf der eXtended Finite Element Methode in Kombination mit der Multiskalen-Projektionsmethode. Aufgrund thermischer Dehnungen sowie zyklischer Beanspruchung ist dabei Rissflankenkontakt mit Wärmeübergang zu berücksichtigen. Rissfortschritt wird mit Hilfe eines auf nichtlokaler Schädigung basierenden Rissfortschrittskriteriums berücksichtigt. Am Beispiel von Verdichterblisks und Turbinenschaufeln, die sehr große Temperaturgradienten aufweisen, wird der Einfluss der gekoppelten thermomechanischen Beanspruchung auf den Rissfortschritt demonstriert. In Kooperation mit vielen anderen Teilprojekten des SFB 871 werden hierfür realistische Randbedingungen verwendet und die Ergebnisse aus den numerischen Untersuchungen mit experimentell gewonnenen Ergebnissen validiert.
Ansprechpartner:
Rohan Patel
Kooperationspartner:
Institut für Kontinuumsmechanik (IKM), Leibniz-Universität Hannover
Abstrakt:
Hochfeste Betone zeichnen sich gegenüber normalfesten Betonen durch ihr dichteres Gefüge aus. Das Materialverhalten hochfester Betone bei monoton steigender Belastung unterscheidet sich deutlich von dem normalfester Betone und wird hauptsächlich durch die optimierten Eigenschaften der Zement- bzw. Bindemittelmatrix und der Kontaktzone beeinflusst. Hinsichtlich des Ermüdungsverhaltens hochfester und normalfester Betone ist jedoch bisher nicht geklärt, inwieweit sich die Schädigungsprozesse aufgrund ihres unterschiedlichen Gefüges unterscheiden.
Im Rahmen dieses Gemeinschaftsprojektes zusammen mit Dr.-Ing. Nadja Oneschkow, Institut für Baustoffe, Leibniz Universität Hannover, werden die Degradationsmechanismen hochfester Betone unter zyklischer Beanspruchung grundlegend untersucht, beschrieben und modelliert. Hierbei werden insbesondere auch die Entstehung und Fortentwicklung von Rissen in den unterschiedlichen Phasen des Degradationsprozesses betrachtet. Mithilfe eines stufenweisen Vorgehens werden die Einflüsse ausgewählter betontechnologischer Maßnahmen zur Herstellung hochfester Betone auf das Ermüdungsverhalten systematisch untersucht. Die Degradationsmechanismen werden anhand verschiedener Schädigungsindikatoren erfasst sowie Unterschiede herausgearbeitet und quantifiziert, wobei die Anwendung der Schädigungsindikatoren gleichsam im Hinblick auf ein Experimental-Virtual-Lab untersucht und beurteilt wird. Ergänzend werden hochauflösende, bildgebende Verfahren eingesetzt und so Risszustände beobachtet und den Entwicklungen der Schädigungsindikatoren im Ermüdungsprozess zugeordnet. Methodisch sind in diesem Gemeinschaftsprojekt ein experimentell/baustoffliches und ein theoretisch/numerisches Teilprojekt vorgesehen, die in einer engen sowohl inhaltlichen als auch methodischen Vernetzung arbeiten. Zu den auf sehr kleinen Skalenebenen ablaufenden, allerdings nur auf höheren Skalenebenen im Experiment beobachtbaren Schädigungsprozessen, sollen Erkenntnisse ermittelt werden, indem durch eine skalenübergreifende Modellierung, die anhand der Experimente kalibriert wird, Rückschlüsse auf Prozesse in den kleinen Skalenebenen gezogen werden. Hierfür wird am Institut für Kontinuumsmechanik die Multiskalen-Projektionsmethode in Kombination mit der XFEM und mit nichtlokaler Schädigung zur Berechnung der Rissentstehung und des dynamischen Rissfortschritts auf mehreren Skalen eingesetzt. Aus der engen Zusammenarbeit zwischen dem Institut für Baustoffe und dem Institut für Mechanik und Flächentragwerke und der hieraus resultierenden engen Vernetzung von Experiment und Berechnung werden Komponenten eines Experimental-Virtual-Labs (EVL) entwickelt und erprobt.
Ansprechpartner:
Alina Juan-Lien Ramirez
Abstrakt:
Die durch Strömung induzierte Entstehung von Rissen und Klüften in Felsgestein ist ein Prozess mit großer Relevanz für geotechnische Anwendungen, wie etwa bei der geothermischen Energiegewinnung („fracking“) oder bei der Erdölgewinnung. Das Verständnis, wie Risse und Klüfte durch Strömung entstehen können ist ebenfalls wichtig für die Risikobewertung von Küstenbauwerken. In diesem Projekt soll der Zusammenhang zwischen der Strömung eines Fluids, das unter hohem Druck in ein Material injiziert wird, und den entstehenden Rissmustern untersucht werden. Dabei soll die Rückkopplung der Prozesse berücksichtigt werden. Zu diesem Zweck soll ein numerisches Modell erstellt werden, das die Strömung und Rissbildung gekoppelt beschreibt und das mit den kompexen entstehenden Strukturen von Klüfen und Rissen adäquat umgehen kann. Das Modell soll andererseits die Gleichungen möglichst effizient lösen. Zu diesem Zweck wird die erweiterte Finite Elemente Methode (XFEM) verwendet.
Ansprechpartner:
Tengfei Lyu, Shahbaz Ahmed
Kooperationspartner:
Institut für Kontinuumsmechanik (IKM), Leibniz-Universität Hannover
Abstrakt:
Während der Umformung von Metallen werden erhebliche Mengen mechanischer Arbeit aufgrund großer plastischer Deformationen dissipiert. Der resultierende Temperaturanstieg führt zu thermischen Dehnungen und einer möglichen Änderung der Materialeigenschaften, die das mechanische Verhalten während der Umformung sowie die Geometrie des umgeformten Körpers beeinflussen kann. Aus diesem Grund ist es wichtig, thermische Effekte und Wärmeleitung in der Materialmodellierung der polykristallinen Mikrostruktur des betrachteten Metalls zu berücksichtigen. Das resultierende thermomechanische Problem zeigt eine starke Kopplung, da auf der einen Seite durch mechanische Dissipation Wärme entsteht, auf der anderen Seite die mechanischen Eigenschaften aber auch von der Temperatur abhängen können und auch große thermische Dehnungen auftreten können. Experimentell kann der Temperatureinfluss ermittelt werden indem Umformversuche an Materialproben bei unterschiedlichen Temperaturen durchgeführt werden. Die Ergebnisse können für die Modellierung des thermomechanischen Materialverhaltens auf der Mikrostrukturebene genutzt werden. Über Homogenisierungsverfahren werden hierdurch die makroskopischen Eigenschaften ermittelt und das effektive Materialmodell, das in Förderperiode 1 des SFB TR73 entwickelt wurde, erweitert.
Ein weiterer kritischer Effekt, der während der Umformung auftreten kann, ist die Initiierung und der Fortschritt von Mikrorissen. Dieser Effekt führt zu einer Reduktion der Steifigkeit oder sogar zum Versagen des Bauteils. Daher ist es sehr wichtig, die Degradationseffekte in der polykristallinen Mikrostruktur zu untersuchen. Ein nichtlokales Schädigungsmodell kann dabei genutzt werden, um die Effekte von Mikrorissen abzubilden. Für Rissfortschrittsberechnungen werden existierende Modelle um nichtlineares, anisotropes und inelastisches Materialverhalten erweitert. Insbesondere für den Fall eines Risswachstums über bzw. entlang von Korngrenzen müssen Rissfortschrittskriterien entwickelt werden. Für den Fall stabilen Risswachstums können repräsentative Volumenelemente genutzt werden um ein effektives, mikromechanisch motiviertes Spannungs-Dehnungsverhalten zu erhalten. Über diese Vorgehensweise kann das Materialmodell, das in Förderperiode 1 des SFB TR73 gewonnen wurde, erweitert werden. Dabei ist es wichtig, die Entfestigung des Materials über ein nichtlokales Schädigungsmodell abzubilden. In einem letzten Schritt werden die beiden Ansätze dieses Projektes kombiniert, um das thermomechanische Verhalten inklusive Schädigung abbilden zu können.
Ansprechpartner:
Martina Baldrich, Felix Töller
Kooperationspartner:
Institut für Kontinuumsmechanik (IKM), Leibniz-Universität Hannover
Abstrakt:
Ziel des Sonderforschungsbereichs SFB 1153 „Tailored Forming“ ist das Potential einer neuen Fertigungstechnologie, dem „Tailored Forming“, für hybride Umformbauteile zu eröffnen. Im Gegensatz zu etablierten Fertigungsprozessen für hybride Bauteile, in denen das Fügen entweder während oder im letzten Schritt der Prozesskette erfolgt, werden beim „Tailored Forming“ zu Beginn des Fertigungsprozesses die aus unterschiedlichen Materialien bestehenden Halbzeuge gefügt und anschließend gemeinsam umgeformt. Der kontrollierte Materialfluss während der Umformung ermöglicht neue Designs für die Fügezone, die in herkömmlichen Herstellungsverfahren nicht möglich wären. Außerdem kann in Abhängigkeit der Materialkombination der thermomechanische Umformprozess für eine verbesserte Fügequalität sorgen.
Ziel des Teilprojekts C4 innerhalb des SFB 1153 ist die multiphysikalische Modellierung und Simulation des Mikrostrukturverhaltens der Fügezone während des Umformprozesses und die Beschreibung der makroskopischen, effektiven thermomechanischen Eigenschaften der Fügezone während und nach der Umformung. Das im Projekt entwickelte makroskopische Materialmodell und die hierfür gewonnenen Materialparameter werden von anderen Teilprojekten im SFB für weitere Umformsimulationen genutzt. Eine Herausforderung für die Modellierung und Simulation der Mikrostruktur der Fügezone ist das teilweise sehr unterschiedliche Materialverhalten der Fügepartner. In der Fügezone finden während des Fügens, der Umformung und einer anschließenden Wärmebehandlung sehr komplexe, stark gekoppelte thermochemomechanische Prozesse statt. Diffusion spielt eine wichtige Rolle für die Kohäsion der Materialien. Dieses komplexe Materialverhalten muss auf der Mikroebene modelliert und simuliert werden. Ein zweites Ziel des Teilprojekts ist die Vorhersage von Eigenspannungen nach der Umformung speziell in der Nähe der Zwischenschicht aber auch nahe der Oberflächen. In Kooperation mit vielen anderen Teilprojekten des SFB findet eine Validierung der Modellierung statt. Andere Teilprojekte nutzen im Gegenzug die entwickelten Modelle für makroskopische Umformsimulationen.
Weitere Forschungsfelder:
"Mulitphysikalische Materialmodellierung auf mehreren Skalen"