Polymorphic uncertainty modeling of heterogeneous thermo-hydro-mechanical coupled systems under vague assumptions of parameter correlations
Abstract of the planned project content, taking into account the results from the first project phase
Over the past few decades, the digitization in the construction industry has been progressed considerably. It has been integrated into processes ranging from the design and planning stage to the lifetime monitoring and maintenance of structures. The increased automation and rationalization save costs and time, and they also improve the workspace safety. In comparison to conventional, i.e. mostly subtractive or forming, production methods, additive manufacturing techniques enable a design-driven manufacturing process so that structures with a high degree of complexity, design freedom and functionality can be produced. It is currently state of the art to further develop 3D printing techniques and to optimize them in order to obtain structures with well-defined properties and reliable behavior under loads.
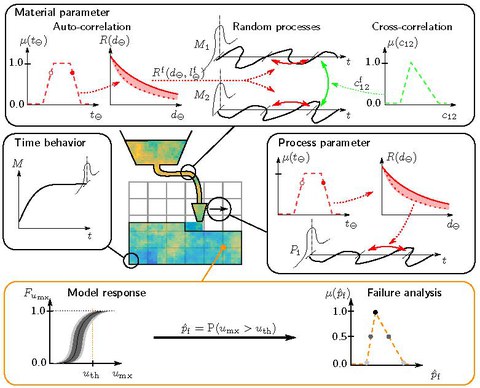
Principle scheme: finite element framework using an adaptive pseudo-density approach; failure analysis during the printing process; polymorphic uncertainty description of the model parameters: material parameter M1, M2, process parameter P1 and time behavior of material parameter M, the model response u is used for a fuzzy stochastic failure analysis
For most materials and printing techniques it is common, that uncertainties dominate the processes. For instance, during 3D extrusion printing of concrete, the viscosity of the pumped liquid concrete may change, affecting the geometry, the hardening and final properties of the structure. It should be accepted, that parameters during a process vary randomly, where however auto-correlations during the process are present. These correlations are however not fully known, motivating the application of fuzzy probability-based random variables. Furthermore, some input parameters of a model representing a 3D printing may exhibit cross-correlations with other parameters which should be accounted for. Again, for the point-wise cross-correlation parameters are vaguely know and have to be taking into account appropriately. Taking this together, the project results in a polymorphic uncertainty description of a transient finite element-based 3D printing process of concrete, where cross- and auto-correlated random processes are converted into cross-correlated random fields, namely the spatially and randomly varying material properties of the resulting structures.
Having a precise uncertainty description included in the model, this can be further taken for reliability analysis of the process, where different failure modes are to be considered (exceeding of strength, geometric requirements, buckling and layer interface strength).
Finally, the model can be used to steer a 3D printing process optimally under a rigorous consideration of all types of uncertainties.
Essential project goals and objectives
- Development of a general framework for FE-based 3D printing
- Study of the failure mechanisms in 3D printed concrete structures using appropriate material parameters and models
- Implementation of various failure mechanisms using a multi-level approach spanning from analytical approximation to non-linear simulation
- Development of a polymorphic uncertainty model describing various material and process parameters using fuzzy probability-based random processes and fields with vague auto- and cross-correlations
- Optimization of the extrusion process within a polymorphic uncertainty framework
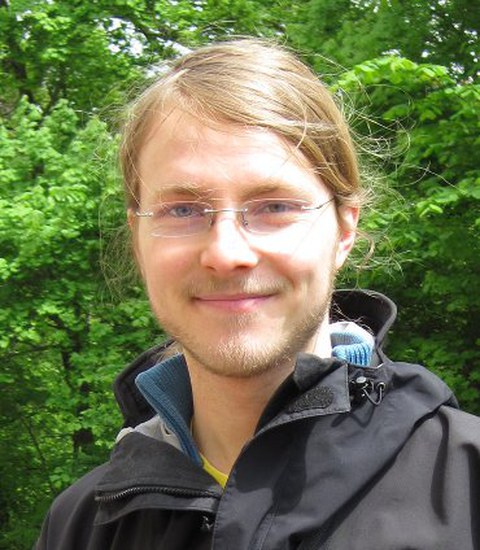
Hr. Schmidt
Dipl. Phys. Albrecht Schmidt
Bauhaus-Universität Weimar
Institut für Strukturmechanik