Design and Evaluation of Intermodular Safety Strategies for Modular Plants Plants
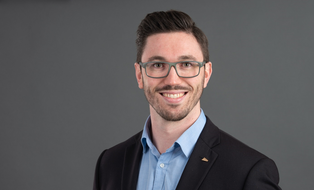
Doctoral researcher
NameFlorian Pelzer M.Sc.
Send encrypted email via the SecureMail portal (for TUD external users only).
Research Training Group 2323
Research Training Group 2323
Visiting address:
Institutsgebäude S7A
Raum / Room 205
Georg-Schumann-Str. 7a
01187 Dresden
Supervisor: Prof. Leon Urbas |
Challenge
Modular plants are the process industry's answer to the increasing volatility of the market and the resulting need for shorter time-to-market and greater product customization. The decisive characteristic of a modular plant is its flexible adaptability to different market situations. There are basically two strategies available for this: The far-reaching adaptation of the production characteristics by exchanging modules or the more finely tuned adaptation of the production characteristics by exchanging a sub-module. Both approaches have their advantages and disadvantages. From the perspective of plant safety, both interventions represent a potential source of risks for humans, environment and the plant, since dangerous alternating effects between process and equipment can occur. The challenges that arise from the pairing of functional safety and modular process plants can be summarized as follows: The policies, procedures, technologies, and competencies developed and established for conventional process plants are not able to adequately address and mitigate the risks of the highly variable modular equipment in the process industry.
Research Approach
In this research, I therefore investigate the adaptation of modular process plants by adapting or replacing process modules from a functional safety perspective. To this end, the following research items are adressed:
Adapted workflows for engineering safety systems in Modular Analgene are developed,
An architectural concept for the installation of safety systems on modules and in the process plant will be developed,
A reference implementation by the construction of a process plant is created to finally
To study the operator activities during the adaptation and replacement of modules and sub-modules and to identify necessary competencies and training.
By this research the functional safety of modular plants should be ensured without having to compromise on plant flexibility. In order to enable a smooth safety-related interconnection of several process modules from different manufacturers, an engineering workflow is developed for the plant and module engineering (01). Requirements for the architecture of intra- and intermodular Safety Systems can be derived from this. Distributed safety systems of process modules (intramodular safety system) should be interconnected by an safety orchestration (intermodular safety system) for intermodular risk control (02). In order to test the feasibility of the safety strategies on the one hand and to carry out in situ operator studies on the other, a demonstration plant was developed to implement the concepts in accordance with the specifications of VDI2776 (03). In the last work package, this demonstration plant was used to observe the safety-related tasks of operators during the exchange and to derive conducive design measures (04).
Effect of the research for Industrial Application
Plant operators are provided with methods and concepts for implementing functional safety, which can be used to efficiently adapt decentralized safety systems to prevailing process requirements. Based on the safety workflow, engineers and operators can be trained to meet the requirements of the new task and work environment.
Personal Motivation of Florian Pelzer to Adress this Topic
Personally, I see functional safety less as a game changer and more as an enabler of flexible production. The spectrum of possible module combinations and processes is expanded by appropriate safety concepts. In my opinion, the sophisticated adaptation of established procedures is to be understood as a critical success factor of modular automation.