Numerical and experimental analysis of permeation and cracking behavior of fiber-reinforced plastic composites with thermoplastic matrix system
In order to limit man-made climate change, achieving greenhouse gas neutrality in Germany by 2045 is essential. Hydrogen plays a key role in the upcoming technological change in almost all scenarios as a versatile and - if produced with renewable energies - environmentally friendly energy carrier. As a storage medium, it is characterized by a high gravimetric energy density compared to lithium-ion batteries. This means that even energy-intensive mobility applications can be designed in a climate-friendly way and implemented without emissions. If the basic system architecture of vehicles or aircraft with green hydrogen as a CO2-neutral energy carrier is to be maintained in the mobility sector, installation space must be used much more efficiently in order to maintain the previous performance data. Among the available storage systems for hydrogen, pressurized storage systems represent a promising technology for mobile applications due to their advanced maturity, simpler handling and comparatively high storage density.
For developing linerless hydrogen pressure tanks, the overall objective of the project is the qualitative and quantitative analysis of the permeation behavior of continuous reinforced textile composites with thermoplastic matrix such as scrim and braided composites. Gas permeation through FRP is mainly favored by crack networks. The influence of these cracks on composite permeability will be investigated using carbon fiber reinforced polyamide 6. For this purpose, experimental methods in the field of CT imaging analysis as well as numerical crack modeling using the phase field method will be further developed and applied to the analysis of crack patterns. In this sense, the term crack pattern includes the arrangement of different single cracks up to branched and connected crack paths. Models for crack prediction, quantification and classification are developed, validated and provided for future permeation assessment of textile architectures. Furthermore, the influence of opened cracks is investigated in in-situ permeation tests and a numerical permeation model is derived. A sound understanding of the relationships between crack and permeation phenomena for composites with textile reinforcement architectures will be generated to provide the basis for successful design and layout of linerless space-efficient pressure tanks and pipelines.
Cooperation
Contacts
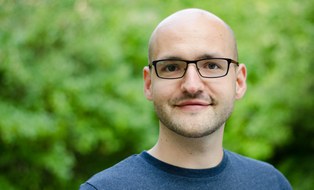
Dr.-Ing. Franz Hirsch
Send encrypted email via the SecureMail portal (for TUD external users only).
Chair of Computational and Experimental Solid Mechanics
Visiting address:
Zeunerbau, Room 356 George-Bähr-Straße 3c
01069 Dresden
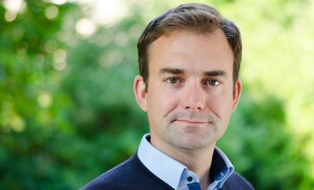
Professor for Computational and Experimental Solid Mechanics
NameProf. Dr.-Ing. habil. Markus Kästner
Send encrypted email via the SecureMail portal (for TUD external users only).
Chair of Computational and Experimental Solid Mechanics
Visiting address:
Zeunerbau, Room 353 George-Bähr-Straße 3c
01069 Dresden