SPP1712 – Intrinsic hybrid composites for lightweight structures – Principles of manufacturing, characterisation and dimensioning
Development of the theoretical and technological principles for intrinsic thermoplastic-metal hollow structures with load-optimised multiscale form closure
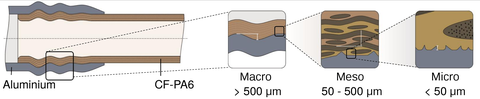
Hybrid metal-composite with hierarchical interface structure.
In contrast to conventional forming processes as adhesive and riveted technologies, approaches with a mechanical interlock between a metal element and fibre-reinforced polymers (FRP) are rarely investigated. A material- and production-oriented design of intrinsic hybrids is the basis for the development of innovative lightweight joints with a mixed-architecture. A mechanical interlock allows the application of extreme loads into rod-shaped and tubular FRP structures, for instance pressure tanks, axis structures, shaft drives and tensile bars. Contour joints are particularly suitable for carrying longitudinal forces and bending moments. Though, specifications for those joint technologies are still missing. The objective of subproject 5 within the Priority Programme (SPP) 1712 is therefore the development of the theoretical and technological principles for intrinsic thermoplastic-metal hollow structures with load-optimised multiscale form closure. At the Chair for Computational and Experimental Solid Mechanics the following scopes are investigated:
- Modelling and simulation of the hierarchical material and interface structure of hybrid composites
- Development of multiscale homogenisation methods for characterisation of effective interface properties
- Modelling of damage and failure behaviour of the FRP material and different interface profiles
- Implementation and parametrisation of macroscopic cohesive zone models with properties extracted from microscale simulations
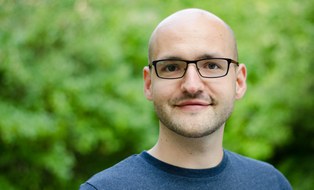
Dr.-Ing. Franz Hirsch
Send encrypted email via the SecureMail portal (for TUD external users only).
Chair of Computational and Experimental Solid Mechanics
Visiting address:
Zeunerbau, Room 356 George-Bähr-Straße 3c
01069 Dresden
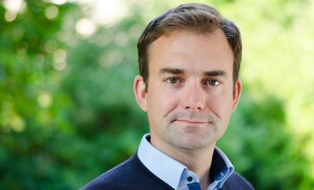
Professor for Computational and Experimental Solid Mechanics
NameProf. Dr.-Ing. habil. Markus Kästner
Send encrypted email via the SecureMail portal (for TUD external users only).
Chair of Computational and Experimental Solid Mechanics
Visiting address:
Zeunerbau, Room 353 George-Bähr-Straße 3c
01069 Dresden
Cooperations
DFG Priority Programme (SPP) 1712
Prof. Dr.-Ing. habil. Maik Gude, Institute of Lightweight Engineering and Polymer Technology (ILK), TU Dresden
Dr.-Ing. Roland Müller, Fraunhofer Institute for Machine Tools and Forming Technology, Chemnitz
PUPLICATIONS
Journals
- F. Hirsch, M. Kästner
Microscale simulation of adhesive and cohesive failure in rough interfaces.
Eng Fract Mech, 2017. [doi] - R. Kießling, J. Ihlemann, M. Pohl, M. Stommel, C. Dammann, R. Mahnken, M. Bobbert, G. Meschut, F. Hirsch, M. Kästner
On the Design, Characterization and Simulation of Hybrid Metal-Composite Interfaces
Appl. Comp. Mater., 23: 1-19, 2016. [doi] - R. Kießling, F. Hirsch, C. Dammann, M. Bobbert, M. Pohl, M. Kästner
Hybrid Metal-Composite Interfaces: Aspects of Design, Characterisation, and Simulation
Adv. Mat. Res., 1140: 255-263, 2016. [doi] - M. Kästner, S. Müller, F. Hirsch, J.-S. Pap, I. Jansen, V. Ulbricht
XFEM Modeling of Interface Failure in Adhesively Bonded Fiber-Reinforced Polymers
Adv. Eng. Mater., 18: 417–426, 2015. [doi]
Proceedings
- F. Hirsch, M. Kästner
Multiscale modelling and simulation of failure in metal-composite interfaces
Proc. ECCM17, 2016. - F. Hirsch, M. Kästner
Modelling and simulation of failure in rough multimaterial interfaces
Proc. Appl. Math. Mech., 16: 525-526. Wiley, 2016. [doi]
Talks
- F. Hirsch, M. Kästner
Numerical study of adhesive and cohesive failure of structured interfaces
GAMM 2017 , Weimar, 2017. - F. Hirsch, M. Kästner
Multiscale modelling and simulation of failure in metal-composite interfaces
ECCM17 , Munich, 2016. - F. Hirsch, M. Kästner
Modelling and simulation of failure in rough multimaterial interfaces
GAMM 2016 , Braunschweig, 2016.