SPP2013 - Targeted use of Forming Induced Internal Stresses in Metal Components
Experimental Characterization and numerical analysis of the beneficial influence of internal stresses on the fatigue behaviour of transversely rolled components
Forming manufacturing processes are a material-efficient alternative to machining manufacturing. During forming, internal stresses are induced. Since those might lead to damage in the components, internal stresses have been avoided where possible until now. In the DFG Priority Programme 2013, now benefits of internal stresses concerning material behaviour are to be investigated and specifically induced.
This subproject focusses on the generation of internal stresses in transversely rolled components in order to enhance their fatigue behaviour. During the first phase of the programme, the relations between forming process, induced internal stresses and fatigue behaviour are studied.
Main objectives of the project are:
-
Characterisation of the mechanical behaviour and analysis of the initial state of the semi-finished products
-
Development of efficient mechancial models to simulate the formation of internal stresses during the forming process
-
Differentiation between the effects of the internal stresses and material and surface transformations on the enhancement of the fatigue behaviour
-
Development of numerical models to simulate crack initiation, internal stress relaxation and crack propagation under cyclic loads
As a first step, a phase-field model for fatigue crack propagation is developed.
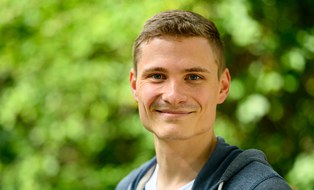
Dipl.-Ing. Tom Schneider
Send encrypted email via the SecureMail portal (for TUD external users only).
Chair of Computational and Experimental Solid Mechanics
Visiting address:
Zeunerbau, Room 353 George-Bähr-Straße 3c
01069 Dresden
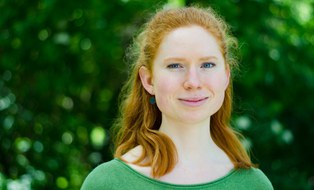
Dr.-Ing. Martha Kalina
Send encrypted email via the SecureMail portal (for TUD external users only).
Chair of Computational and Experimental Solid Mechanics
Visiting address:
Zeunerbau, Room 355 George-Bähr-Straße 3c
01069 Dresden
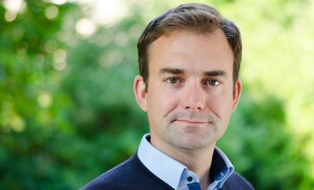
Professor for Computational and Experimental Solid Mechanics
NameProf. Dr.-Ing. habil. Markus Kästner
Send encrypted email via the SecureMail portal (for TUD external users only).
Chair of Computational and Experimental Solid Mechanics
Visiting address:
Zeunerbau, Room 353 George-Bähr-Straße 3c
01069 Dresden
Cooperations
DFG Priority Programme 2013
Prof. Dr.-Ing. Alexander Brosius, Institute of Manufacturing Schience and Engineering