Nov 30, 2023
Compostable theater sculptures from the 3D printer: Innovation from Dresden for sustainable theater construction
In the "GreTA" research project, artists from the Dresden University of Fine Arts (HfBK Dresden) and scientists from the Institute of Lightweight Engineering and Polymer Technology (ILK) at TU Dresden have focused on the development of environmentally friendly theater sculptures using state-of-the-art 3D printing technologies and sustainable materials. The aim is to produce impressive stage sets that are not only aesthetically impressive, but also environmentally friendly.
Current theater sculptures, especially those with large dimensions and high complexity, generate considerable amounts of non-recyclable waste, mainly in the form of polystyrene. With the help of the "GreTA" research project, it should be possible to dispense with this in future by relying on liquid deposition modeling (LDM) as a suitable process for 3D printing of bio-based materials.
Material tests with agar-agar, carrageenan and glutin glue
Extensive material tests have already been carried out during the research project in order to identify suitable natural materials for the 3D printing process. Instead of conventional thermoplastics, a plastic mass is used that must be recyclable, stable, lightweight and cost-effective. Various binders, such as agar-agar, carrageenan and cell glue, have already been tested for use in the LDM process, but these often led to long drying times, severe shrinkage and low adhesion. The solution was found in glutin glue, which cures at room temperature to form a stable thermoplastic elastomer. Uniform shrinkage is already taken into account when creating the 3D model. In combination with suitable fillers and additives, it becomes an impact-resistant mass that is fully compostable and recyclable.
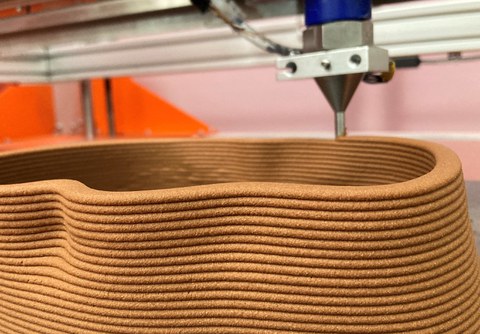
Materialtests mit Agar-Agar und Korkmehl im LDM-Verfahren
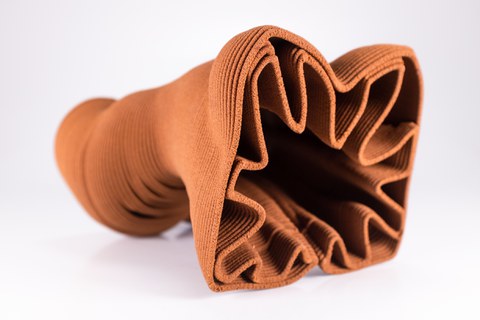
Erstes erfolgreich gedrucktes Objekt aus Glutinleim und Korkmehl mit einer Größe von 40 cm und spezieller Stützstruktur
Successful practical test at the Rathen rock stage
The developed technology has already been successfully tested in practice. As part of the project, two original-sized "pig halves" for the opera "Der Freischütz" were created using the LDM process with the developed material recipe of water, glycerine, cork flour and glutinous glue. The perfect model was captured and digitized at the "Vorwerk Podemus Hof" using mobile scanning technology. A filling structure optimized in terms of printing time, surface, stability, drying and shrinkage behaviour was then designed for the spiral vase mode. The five-part model had to air-dry for around a week before it could be assembled and glued together. The employees of the Landesbühnen Sachsen took care of the deceptively realistic painting and finalization for the stage.
Prof. Ulrich Eißner from the HfBK emphasizes: "The production of the 'Freischütz pig halves' for the Felsenbühne Rathen initially filled us as a research team with pride and joy. After all, it was the very first practical theater application of our developed 3D printing process. And it works, even if not everything is perfect yet. The use of recyclable and compostable materials not only represents a groundbreaking improvement in 3D printing technology, but also opens the door to new creative horizons for stage designers and artists. The focus on sustainability combined with cutting-edge technology shows that art and environmental awareness can go hand in hand."
The "GreTA" project is co-financed with tax revenue on the basis of the budget approved by the Saxon state parliament.
*GreTA - Generative production of recyclable basic structures for theater sculpture from nature-based raw materials.
Information and queries to: Prof. Niels Modler(), Johanna Maier(), Leopold Dietrich(), Prof. Ulrich Eißner(), Carl Ahner (ahner@hfbk-dresden.de)