Feb 15, 2017
Textile sensors for reliable component monitoring
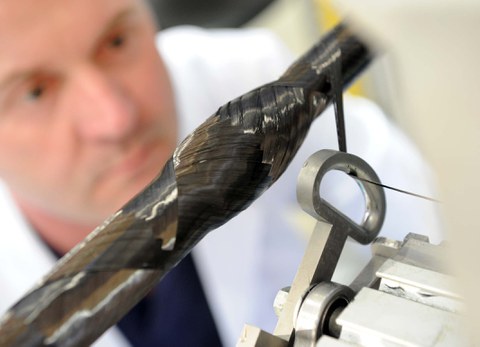
The manufacturing of components such as this braided shaft is particularly challenging if the damage-free integration of sensory carbon fibres is required.
Scientists from Technische Universität Dresden (TU Dresden) participating in the Tessy research project (Monitoring CFRP Structures Using Textile-Based Sensory Systems Integrated Using Textile Technologies) are currently developing textile-based sensor networks suitable for integration into heavy-duty CFRP components.
Designs for CFRP components such as rotor blades forming part of wind turbines often deliberately make the components larger than they actually need to be. The aim of this “oversizing” is to compensate for missing information on the residual load-bearing capacity of the components further to ageing, overloading or other relevant loading events.
The data yielded by conventional structural health monitoring techniques is nevertheless of limited validity. Strain gauges, for example, are unsuitable for the reliable delivery of accurate measurements over a long period. This is attributable to inherent disadvantages such as adhesive failure due to environmental factors and the gauges’ high level of sensitivity to temperature. Up to now, the CFRP-compatible integration of monitoring technology into heavy-duty components has therefore only been possible up to a point.
The Tessy project: Predictable, reliable lightweight engineering
Initiated by the Federal Ministry for Economic Affairs and Energy, the Tessy research project sees scientists from the Institute of Textile Machinery and High Performance Material Technology (ITM), the Institute of Lightweight Engineering and Polymer Technology (ILK) and the Institute of Electronic Packaging Technology (IAVT, all part of TU Dresden) develop textile-based sensor systems based on carbon fibres connected to an electrical circuit. Taking advantage of the electrical conductivity of the carbon fibres, the researchers measure strain by monitoring the fibres’ electrical resistance, which varies depending on the strain placed on the reinforcement structure.
In addition to the intelligent connection and arrangement of the sensor fibres, the main challenge faced by the scientists is the damage-free integration of the sensory carbon fibres into the textile reinforcement structure. In particular, the fibre displacement and pores that occur during infiltration with a polymer matrix may restrict both sensor functionality and the load-bearing capacity of the component. Scientists participating in the Tessy project are therefore analysing and evaluating how sensor layout affects the infiltration of semi-finished textiles using conventional techniques. Material testing focusing on component performance is also being used to gain insights into potential damage to reinforcement structures caused by the integration of sensor fibres and their electrical contacts.
Oversizing no longer necessary
Unlike conventional structural health monitoring systems, the novel sensors are able to detect not only local and global, but also static and dynamic strain and structural deformation throughout the service life of a component. The simulation-assisted analytical procedures being developed as part of the project will make it possible to deliver immediate statements on the residual load-bearing capacity of a component. CFRP-compatible integration should also lead to long-term sensor stability throughout the service life of the overall structure. In the words of the Director of the ITM, Prof. Dr.-Ing. habil. Chokri Cherif: “These novel sensors facilitate the precise localisation of all critical changes to the structure. This enables us to identify potential damage at an early stage – and in turn avoid the considerable costs associated with consequential repairs. In the long-term, these textile-based sensors will render the safety-related oversizing of CFRP components unnecessary. In addition to saving both resources and energy, this will also reduce CO2 emissions during production.”
Two prototypes designed for applications in the fields of medical technology and automotive engineering respectively will be used to not only demonstrate the considerable potential offered by sensor networks of this type, but also validate the sensors’ functionality in combination with a comprehensive set of analytical methods.
Contact
Technische Universität Dresden
Institute of Lightweight Engineering and Polymer Technology (ILK)
Dipl.-Ing. Oliver Weißenborn, Research Associate
Tel.: +49 (0) 351 463 42573
Email:
Institute of Textile Machinery and High Performance Material Technology (ITM)
Dipl.-Ing. Eric Häntzsche, Research Associate
Tel.: +49 (0) 351 463 31635
Email:
Institute of Electronic Packaging Technology (IAVT)
MSc. Ievgen Kharabet, Research Associate
Tel.: +49 (0) 351 463 43776
Email: