HyBLex
Development of high-temperature resistant fibre-plastic composites for cost-efficient production of hybrid fibre-composite-metal structures for future lightweight drive components under extreme environmental conditions
Hybrid fibre composite-metal design enable the realization of lightweight drive components that have the same or increased performance with less mass compared to the full metal design. At the same time, the consumption of resources in the production of raw materials, manufacturing, processing and use of lightweight components in hybrid design can be reduced compared to the full metal design.
The realisation of drive components made of fibre-plastic composites is currently significantly limited by the long-term temperature resistance. Thermoset hybrid resins, consisting of cyanate ester and silicone resins or the thermoplastic polyetheretherketone, in combination with carbon fibre reinforcement, have the potential to raise the continuous operating temperature of such components to 250 °C. This opens up a multitude of possible applications to replace the currently metallic components with resource-efficient structures in hybrid design. The basis for this is always a deep understanding of materials and a quality manufacturing process chain (Fig. 1) for the production of temperature-resistant hybrid lightweight components.
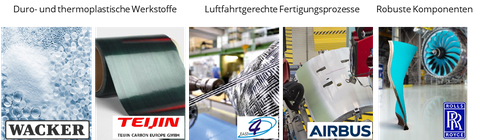
Fig. 1: Continuous process chain from raw material to technology demonstrator.
The aim of the HyBLex project is to develop thermoset and thermoplastic material systems and transform them into operational drive components for use under extreme environmental conditions. This is focused through the interaction of experienced actors along the entire value chain from the raw material supplier, to the component manufacturer and to the end user (Fig. 2).
The project work is additionally supported by competent research institutions in the field of applied materials technology (Fraunhofer IFAM) and lightweight system engineering in multi-material design (TUD-ILK). Through further cooperation with subcontractors in the field of polymer analysis (Fraunhofer IAP), aerospace manufacturing (herone, CTC) and characterisation (LZS), expertise is bundled in a targeted manner to ensure the success of the project.
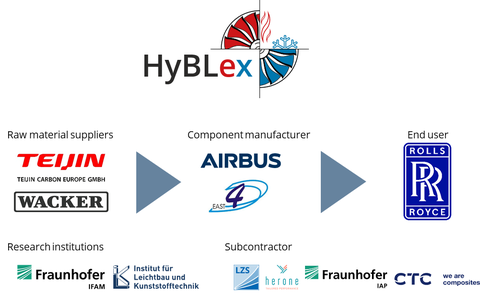
Fig. 02: Partners involved in the HyBLex project.
01.01.2023 - 31.12.2025
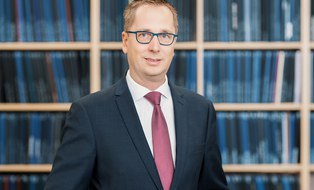
Chair of Lightweight Systems Engineering and MultiMaterial Design
NameProf. Dr.-Ing. habil. Maik Gude
Send encrypted email via the SecureMail portal (for TUD external users only).
Institute of Lightweight Engineering and Polymer Technology
Visitors Address:
DÜR, Floor 0, Room 71 Holbeinstr. 3
01307 Dresden
Deutschland
- Tino Wollmann (Calculation Methods and Simulation)
Publications Tino Wollmann | TU Dresden
- Wikentij Koshukow (Joining Technologies|Thermoplastics Processing)
Publications Wikentij Koshukow | TU Dresden