HyDrun
Analysis of the interface during inline hybridization of metal die-casting
and injection molding
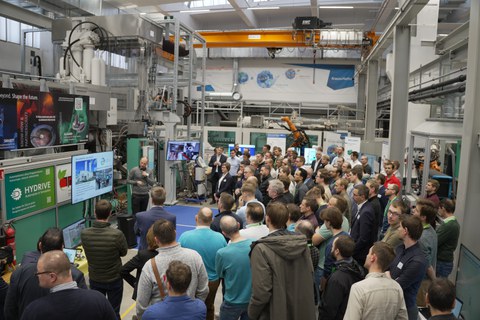
Fig. 2: Sight casting at the final project meeting of the METEOR + HyDrun projects.
In the development of complex and highly resilient lightweight structures, there is a trend towards using different materials in one component. Different manufacturing processes are often combined to produce such multi-material or hybrid components. Among other things, this can reduce high investments in the purchase of machinery or save storage and transport costs. In particular, the innovative inline joining of light metal and plastic is being intensively researched at the ILK under the name of hybrid casting on a new type of DuoCast vertical die casting machine with integrated bolt-on injection molding. With the help of a robot system for component handling, further steps such as deburring and functionalization of the surfaces for injection molding of the plastic are carried out. This enables the synchronized production of complex hybrid structures on a single system. The high degree of automation means that cycle times, energy consumption and costs can be reduced. After commissioning the hybrid casting system, process parameter studies were carried out in the HyDrun project to optimize casting quality and component handling. With numerous production trials in 2024, the end-to-end process sequence was successfully demonstrated at the end of the project and innovative hybrid structures made of metal die casting and plastic injection molding were produced inline (Fig. 1). The result is a unique pilot plant that is also available for testing (Fig.2).
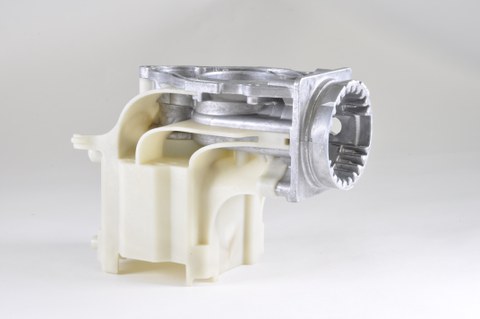
Fig. 1: The HyDrun hybrid demonstrator manufactured inline from die-cast metal and injection-moulded plastic.
01.06.2021 – 31.05.2024
Consortium Leadership
Project partners
- AXIAL Ingenieurgesellschaft für Maschinenbau mbH
- HILTI Entwicklungsgesellschaft mbH
- FRIMO Group GmbH
- Härte- u. Oberflächentechnik GmbH &Co. KG
- HYDRIVE Engineering GmbH
- INNOVENT e.V. Technologieentwicklung
- KraussMaffei Technologies GmbH
Associated partner
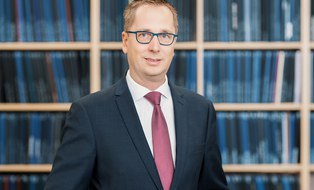
Chair of Lightweight Systems Engineering and MultiMaterial Design
NameProf. Dr.-Ing. habil. Maik Gude
Send encrypted email via the SecureMail portal (for TUD external users only).
Institute of Lightweight Engineering and Polymer Technology
Visitors Address:
DÜR, Floor 0, Room 71 Holbeinstr. 3
01307 Dresden
Deutschland
- Tino Mrotzek (Novel Materials and Special Processes)
Publications Tino Mrotzek | TU Dresden
- Paul Seurich (Novel Materials and Special Processes)
Publications Paul Seurich | TU Dresden
- Dr. Thomas Behnisch (Novel Materials and Special Processes)
Publications Thomas Behnisch | TU Dresden