IndHy
Development of a flexible induction handling system for the robot-assisted series production of metal-plastic hybrid structures
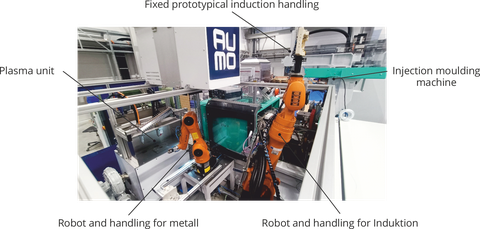
Fig. 1: Process components of the hypro process chain at TUD-ILK.
The results of the completed HyPro research project (One hybrid structure per minute) demonstrate that the fully automated production of metal-plastic hybrid components in batch sizes of 10,000 is feasible (see process video). However, industry feedback indicates that reducing the number of sub-processes is essential for achieving economic viability. Specifically, the use of two articulated-arm robots (see Fig. 1), the weight of the induction handling system, and the performance limitations of the induction systems pose significant challenges for implementation, particularly in small and medium-sized enterprises (SMEs).
For broader market adoption, lightweight, flexible, and high-performance induction generators and handling systems are required for integration with small robot systems that have payload capacities between 5 and 25 kg. To address this, COBES has developed a compact induction generator with a 5 kW output. However, this system does not achieve the rapid heating rates demanded by industry, which are critical not only for hybrid composites but also for other application scenarios. The proposed project aims to enhance this system by increasing its output to 10 kW while maintaining the same installation footprint.
Additionally, the process chain will be restructured to utilize a single articulated robot for all process steps. This will require the development of coupled handling systems capable of performing both gripping and heating tasks. A key challenge is designing a reliable coupling mechanism for water, electricity, compressed air, vacuum, and measurement signals that is compatible with smaller robotic systems.
hypro – holistic implementation of hybrid design in series production © TUD/ILK
01.11.2024 – 31.10.2026
Federal Ministry for Economic Affairs and Climate Action (BMWK): Central Innovation Programme for SMEs (ZIM)
Funding code: KK5047610JF4
German Federation of Industrial Research Associations “Otto von Guericke” e. V. (AiF)
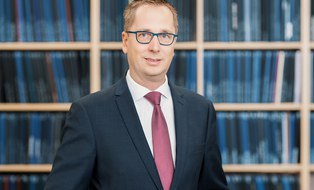
Chair of Lightweight Systems Engineering and MultiMaterial Design
NameProf. Dr.-Ing. habil. Maik Gude
Send encrypted email via the SecureMail portal (for TUD external users only).
Institute of Lightweight Engineering and Polymer Technology
Visitors Address:
DÜR, Floor 0, Room 71 Holbeinstr. 3
01307 Dresden
Deutschland
- Wikentij Koshukow (Joining Technologies |Thermoplastics Processing)
Publications Wikentij Koshukow | TU Dresden