SpiFa
Development of a new type of lightweight partition wall for aircraft based on a new type of load insert made of thermoset hardpoints in combination with fiber composite tapes with a spider web structure for weight savings of at least 5 % and 20 % faster production
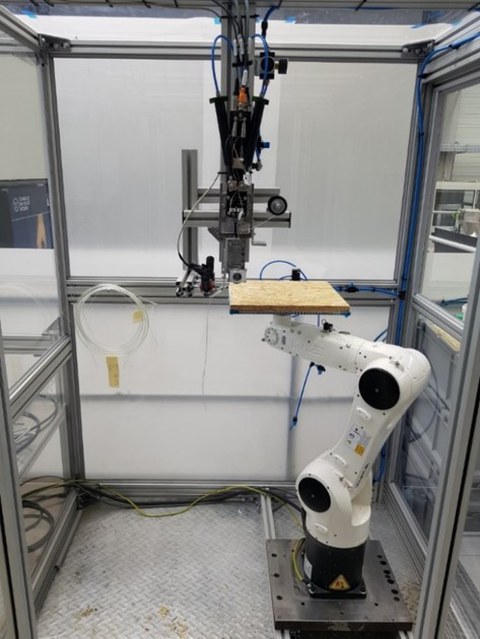
Fiber placement machine.
To reduce CO2 emissions in air traffic, it is necessary to reduce the empty weight of aircraft. Bionic design methods and generative manufacturing processes make it possible to exploit the lightweight design potential in the area of load introduction points in partition wall elements made as sandwich structures. Up to now, for the attachment of add-on parts to these lightweight sandwich structures, consisting of a core material and fiber reinforced face sheets, large areas of the core have been filled with a potting compound before the placement of the load bearing insert.
Based on the design methods, a thermoset hardpoint was developed in combination with a load path-adapted – spider web-like – fiber reinforcement for load transmission into the face sheets, which enables a mass reduction of 5 % and a shortened production time. The load-path-adapted fiber orientation is realized by a fiber placement process in which an impregnated roving is cured at the point of fiber placement by means of UV radiation. Determination of the process parameters and process automation are key areas of research. Pull-out tests are carried out at sub-component level to validate simulation results and, based on the experimental data, a metamodel is created to predict pull-out strengths as a function of significant spider web parameters.
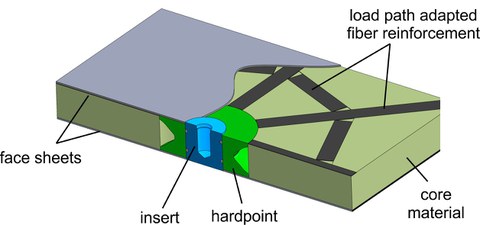
Load introduction point with spider web like fiber reinforcement.
01.09.2021 – 29.02.2024
Federal Ministry of Economic Affairs and Climate Action (BMWK): Central Innovation Programme for SMEs (ZIM)
Funding reference: KK5047605
German Federation of Industrial Research Associations “Otto von Guericke” e. V. (AiF)
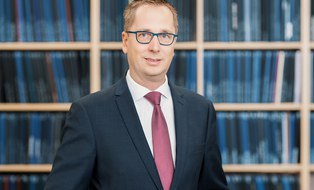
Chair of Lightweight Systems Engineering and MultiMaterial Design
NameProf. Dr.-Ing. habil. Maik Gude
Send encrypted email via the SecureMail portal (for TUD external users only).
Institute of Lightweight Engineering and Polymer Technology
Visitors Address:
DÜR, Floor 0, Room 71 Holbeinstr. 3
01307 Dresden
Deutschland
- Eckart Kunze (Thermoset Processes and Preforming)
Publications Eckart Kunze | TU Dresden