Modellverarbeitungsprozess für eine effektive endkonturnahe Fertigung von Bauteilen aus Faserverbundwerkstoffen - EFFEKT
Teilprojekt Preformhandling
Laufzeit: | 04/2009 – 03/2011 |
Finanzierung: | Bundesministerium für Bildung und Forschung (BMBF) |
Bearbeiter: | Dr.-Ing. Mirko Riedel Dipl.-Ing. Christian Friedrich Dipl.-Ing. Christer Schenke |
Kooperation: | Produktionstechnisches Zentrum Dresden (ProZeD) |
Zielstellung
Das interdisziplinäre Forschungsprojekt erarbeitet einen neuartigen Fertigungsprozess für die Herstellung von dreidimensionalen Bauteilen aus Hybridgarn-Textil-Thermoplast (HGTT)-Halbzeugen. Dabei wird das endkonturnahe Fertigteil durch Heißpressen direkt aus einer textilen Preform erzeugt und somit auf den bisher üblichen Zwischenschritt der Organoblechherstellung verzichtet. Als Demonstratorbauteil wurde ein Federdom ausgewählt.
Das Teilprojekt Preformhandling am IWM befasst sich –im Rahmen der Gestaltung und Umsetzung einer automatisierten Prozesskette – mit der Entwicklung, Konstruktion und Inbetriebnahme der Anlagentechnik zur Herstellung der Preform sowie zur Handhabung der biegeschlaffen Preform und des konsolidierten, biegesteifen Fertigteils.
Lösungsweg
Die Prozesskette (Bild 1) gliedert sich in die Herstellung der textilen Preform aus der Rollenware sowie der anschließenden Umformung und Konsolidierung der Preform zum endkonturnahen Fertigteil. Entsprechend dieser Struktur ist der Prozess am IWM in zwei getrennten Bearbeitungszentren (BAZ) umgesetzt.
Im BAZ 1 erfolgt nach Zustellung des Materials durch die Abzugseinrichtung von der Rolle auf den Schneidrost zunächst der Zuschnitt der Einzellagen mit einem Plasmabrenner. Durch die hohen Temperaturen beim Schneidvorgang wird das Material an den Schnittkanten angeschmolzen und ein Vereinzeln der Gewebebestandteile bei der Handhabung vermieden. Die Handhabung der Einzellagen sowie der fertigen Preform erfolgt mit Vakuumsauggreifern. Durch entsprechend große Öffnungsquerschnitte der Sauger kann ein ausreichend hoher Volumenstrom erreicht und das luftdurchlässige Textil prozesssicher gegriffen werden. Nach dem Stapeln zur Preform und dem Abtransport des Verschnittes durch den umlaufenden Schneidrost erfolgt als letzter Prozessschritt das Fixieren aller sechs Einzellagen mit einem Ultraschallschweißgerät. Die Preform kann somit als Ganzes in weiteren Prozessschritten gehandhabt werden.
Plasmabrenner, Vakuumsauger und Ultraschallschweißgerät können an der Plattform des Hexapod befestigt werden. So ist ein zeitaufwendiger Werkzeugwechsel unnötig und dadurch eine Minimierung der Prozesszeit möglich. Bild 2 veranschaulicht den Prozess im BAZ 1 und die zugehörigen Werkzeuge.
Im BAZ 2 wird aus der textilen Preform durch Heißpressen das Fertigteil hergestellt. Die Anforderungen liegen hier – neben dem Pressprozess selbst – hauptsächlich in der Handhabung der biegeschlaffen Preform und des biegesteifen Fertigteils. In beiden Zuständen muss das Werkstück prozesssicher gegriffen werden, um eine präzise Positionierung der Preform im Werkzeug und das zuverlässige Abnehmen des Fertigteils zu gewährleisten. Die Arbeitsschritte von Industrieroboter und Presse sind durch eine übergeordnete Steuerung koordiniert.
Mittels einer Zustelleinrichtung wird die Preform vor jedem Pressvorgang positioniert. Nadelgreifer stellen beim Greifen der Preform sicher, dass alle Lagen durch das Greifersystem gehalten werden und das genaue Positionieren der Preform im Werkzeug möglich ist. Nach dem Pressen wird das fertige Bauteil mit Vakuumsauggreifern aus dem Werkzeug entnommen und auf einem Fertigteilstapel abgelegt. In Bild 3 ist der Prozessablauf im BAZ 2 dargestellt.
Auch am BAZ 2 werden die Greifersysteme so ineinander verschachtelt, dass ein Werkzeugwechsel vermieden werden kann und eine sehr geringe Bauhöhe erreicht wird. Dadurch ist das Einlegen der Preform ohne vorhergehendes Ablegen des Fertigteils möglich, was zu einer Minimierung der Prozesszeit beiträgt.
Ergebnisse
Bild 4 zeigt die im Forschungsprojekt aufgebauten Bearbeitungs¬zentren, in Bild 5 sind die jeweiligen Werkzeugplattformen dargestellt.
Die im Projekt entstandene Versuchsanlage bleibt in Betrieb und wird für folgende Forschungsprojekte weiterhin eingesetzt:
- „3D Bauteile aus Blech und Textil durch umformende Verbundherstellung“
- „Datenbankgestützte Modellierung und Simulation der Prozessketten zur gezielten Einstellung vordefinierter Eigenschaften sowie zur Absicherung der reproduzierbaren Ferti-gung von thermoplastischen Textil-Verbundbauteilen“
- „InnoFab – Innovationsfabrik als Lehr- und Lernform einer Universität“
Kontakt
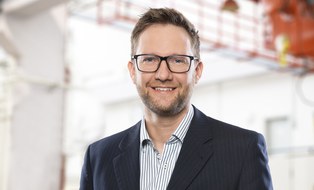
Research associate
NameMr Dr.-Ing. Christian Friedrich
Employee of the department CPPS at Fraunhofer IWU Dresden