Optimierung der Fräsparameter für NiTi-Formgedächtnislegierungen
Inhaltsverzeichnis
Duration: |
07/2023 - 06/2025 |
Funding: | This project is based on a grant from the German Academy of Sciences Leopoldina. |
Author: | Nataliia Balytska |
Motivation
Nickel-titanium (NiTi) shape memory alloys (SMAs) have been the focus of research due to their functional and mechanical properties such as shape memory, super elasticity, high damping, high corrosion resistance, wear resistance and biocompatibility. It is a potential material for biomedical and aerospace applications.
Its unique stress-strain curve with high strain hardening makes predicting machining behavior difficult. In addition, strong adhesion and poor chip breaking, low thermal conductivity, high specific heat and low effective Young's modulus limit machinability. The combination of all these factors results in high specific cutting energy and cutting forces, high tool wear and excessive burr formation. The surface integrity of the finished part is compromised. However, due to the lack of alternatives, machining is widely used to produce precise parts from NiTi-SMA.
Phase transformation of NiTi-SMAs is central to their machinability. The temperature for transformation is only in the range of 60 - 110 °C and depends on the material composition, preheat treatment, and manufacturing method. Small changes in temperature can cause significant changes in material properties due to phase transformation. Phase transformation also depends on the applied stress. Cutting parameters and process design influence not only the temperature, but also the plastic deformation during machining, and therefore greatly affect the functional behavior of NiTi-SMA. This results in a narrow window of suitable machining parameters.
The majority of scientific papers on milling NiTi-SMA focus on end milling, rather than face milling. The research community still lacks a complete understanding of the exact influence of the chemical and phase composition of the alloy, cutting conditions, preheat treatment, tool material and coating, cooling and lubrication conditions, and machining strategy on the face milling process of NiTi-SMA. There is a clear need for more in-depth, systematic studies of how the geometric parameters of face milling tools affect the surface integrity of NiTi-SMA parts. This is particularly important for machining flat, precise workpiece surfaces that require high accuracy, low work hardening, and residual stresses.
Aim of the project
The aim of the project is to improve the quality of machined flat surfaces on NiTi shape memory alloy parts. Higher quality flat surfaces will improve the service life of these parts under harsh operating conditions. The research will focus on determining optimal cutting conditions for face milling NiTi-SMA.
Research idea
The project idea is that the cutting parameters can be optimized to provide chip flow conditions, stress and temperature fields in the cutting zone that would minimize tool wear and result in high surface and sub-surface quality.
The challenge
It is not possible to take into account the simultaneous influence of all factors on the milling process parameters. Technically, it is extremely difficult to obtain the actual values of the temperature fields in the cutting zone when milling nitinol of a certain chemical composition and phase composition. Physical experiments are limited when it comes to placing thermocouples below the surface being machined. Not all of the necessary material properties in various specific material conditions are available for reliable modeling. This also creates difficulties in modeling the cutting forces when machining nitinols.
Path to solution
First, the correlation between cutting conditions (cutting speed, depth of cut, feed rate) and cutting forces, temperatures, surface integrity and tool life in face milling of NiTi shape memory alloys will be investigated based on a DOE that will allow the collection of high quality experimental data.
Second, the identification of milling conditions to minimize cutting forces, temperature fields, and surface roughness, as well as to ensure the quality of the subsurface layer, will allow the development of recommendations for efficient face milling of titanium nickelide.
Results
The expected results are recommendations for the selection of cutting conditions for efficient face milling of austenitic Nitinol. These recommendations ensure minimal roughness of the machined surfaces and proper condition of the subsurface layer after milling.
Current status
The first experiments were carried out on a model DMU 80 eVo milling machine under dry cutting conditions. Flat surfaces of 30 x 30 mm workpieces were milled. Machining was performed using a CoroMill® 300 face mill with uncoated round carbide inserts. The machined NiTi alloy in the austenitic phase had the following chemical composition: Ni 56.05 %, Ti 43.65 % (by weight). Cutting forces were measured using a Kistler 9257B dynamometer. Thermal images were obtained using an Optris PI 450i thermal imaging camera.
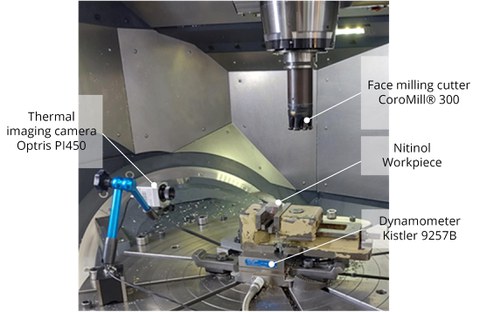
Versuchsaufbau zur Bearbeitung von Nitinol
The optical profilometer was used to analyze the surface micro relief and chip shape after face milling. It was found that the cutting inserts were subjected to very intensive wear at a minimum milling length of 30 mm. Metallographic analysis of the milled samples revealed the presence of martensitic needles in the surface layer, see Figure 2. This indicates the phenomenon of phase transformation in the surface layer of Nitinol caused by milling. The combined effect of high temperature and plastic deformation transforms the austenitic phase into the martensitic phase. This result encourages further study of the process of milling nitinols in order to ensure the required structure of the sub-surface layer and functional properties after machining.
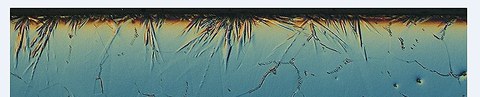
Martenit formation under the machined surface
Publications
in progress
contact
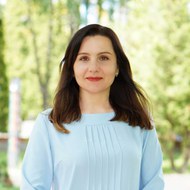
Wissenschaftliche Mitarbeiterin
NameFrau Dr. Nataliia Balytska
Maschinenverhalten
Eine verschlüsselte E-Mail über das SecureMail-Portal versenden (nur für TUD-externe Personen).
Professur für Werkzeugmaschinenentwicklung und adaptive Steuerungen
Professur für Werkzeugmaschinenentwicklung und adaptive Steuerungen
Besuchsadresse:
Kutzbach-Bau, Raum 204 Helmholtzstraße 7a
01069 Dresden