Cross-scale numerical analysis and optimization of machine tool dynamics by integrating particle-filled hollow sphere structures
Table of contents
Project duration: |
07/2023 – 06/2026 |
Funding: | Funded by the German Research Foundation DFG |
Project manager: | Dipl.-Ing. Xin Zhou |
Partner: | Prof. Dr. Matti Schneider Institut für Ingenieurmathematik Universität Duisburg-Essen https://www.uni-due.de/ingmath/ |
Motivation
One way to increase the productivity of machine tools is to increase the feed rates during machining. This usually leads to high acceleration forces. The resulting structural vibrations have a negative impact on the quality of the workpiece surface. The absolutely necessary reduction of vibration amplitudes can be achieved by passive methods, e.g. damping materials, without additional energy input. In order to reduce the acceleration forces of moving assemblies, these are often designed as lightweight structures. However, the necessary combination of lightweight construction and vibration damping is not sufficiently achievable with the existing construction materials for the increasing demands on dynamics.
Particle-filled hollow sphere structures enable lightweight constructions with structure-integrated, locally adapted, passive damping with a simultaneously high modulus of elasticity to density ratio through sandwich construction and thus open up new freedoms in the structural design and optimization of highly dynamic, moving assemblies. For component design, in which the damping from structurally integrated particle dampers distributed over a structure must be taken into account and optimized, no consistent calculation and design methods have been available to date. However, this is absolutely essential for the widespread use of PHS as a construction material.
Objective of the project
The aim of the project is to provide a cross-scale numerical method for the description of particle-filled hollow sphere structures and their application to optimize the structural dynamics of machine tools.
Approach
- Simulation models at the micro level enable efficient mapping of the dynamic behavior of a particle-filled hollow sphere.
- Viscoelastic model approaches make it possible to describe the frequency-selective dynamic properties of the particle-filled hollow sphere structure.
- This mesomodel allows the derivation of a linearized model on macroscopic level and its parameterization.
- The homogenized macroscopic model approach can be embedded in an FE structural model in ANSYS and used to optimize the compliance frequency response of a machine tool.
Challenges
- Uncertainties and difficult-to-detect nonlinear effects occur in the direct measurement of individual hollow spheres.
- The influence of the test setup for characterizing the damping properties of the hollow sphere structure on the measured values must be minimized.
- The use of a linear, homogeneous and isotropic material model to model and simulate the hollow sphere components at the component scale is limited.
Path to solution
A metrologically identified and parameterized modeling strategy is developed from the micro-level (particle level) to the macro-level (component level).
- Metrological quantification of the dynamic properties of individual spheres and characterization of the decay behavior
- Metrological characterization of the damping properties of hollow sphere composites
- Modeling of the dynamic properties of individual spheres, spherical joints and the overall structure and transfer to an FE-compatible model
- Design and model-based optimization of machine tool components with hollow spheres
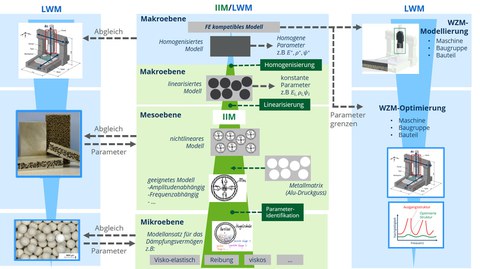
Path to solution for cross-scale optimization
Results
The developed simulation methodology allows the cross-scale mapping of the frequency-selective dynamic properties of particle-filled hollow sphere structures. This allows the macroscopic structure of highly stressed machine elements to be optimized by manipulating local material properties at the micro level. By selectively varying the microscopic parameters such as filling level and particle size, the damping properties of the particle-filled hollow spheres can be varied in such a way that the resulting damping can be optimized with respect to the expected macroscopic structural natural frequencies. These frequency-optimized hollow spheres can then be positioned with spatial resolution at the locations with the best damping effect according to the macroscopic vibration modes.
Current status
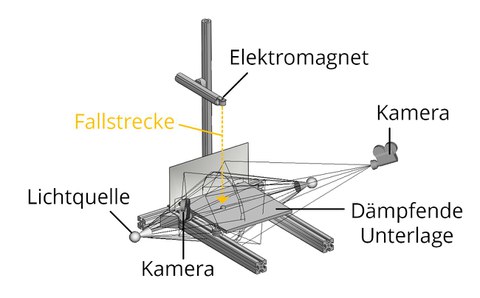
Drop-Ball-Test zur Ermittlung des Dämpfungsverhaltens einer einzelnen Hohlkugel
Derzeit wird ein Prüfstand für die Drop-Ball-Prüfung von einzelnen Hohlkugeln gebaut. The hollow sphere is held by an electromagnet and falls from a defined height onto a cushioning surface. A camera system, consisting of two high-speed cameras and the light sources, is calibrated and records the fall of the ball simultaneously and stereoscopically. The speed before and after the ball first hits the surface is calculated from the images and the energy loss or attenuation of the individual balls is determined.
Contact
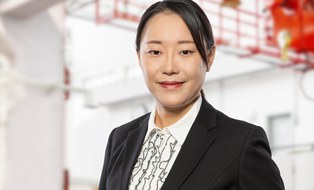
Research associate
NameMs Dipl.-Ing. Xin Zhou
Machine Technology
Send encrypted email via the SecureMail portal (for TUD external users only).
Chair of Machine Tools Development and Adaptive Controls
Visiting address:
Kutzbach-Bau, Room 206 Helmholtzstraße 7a
01069 Dresden