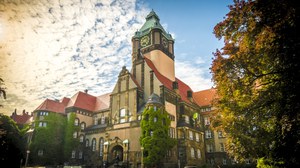
Introduction
Dear readers,
Welcome to the chair of traditional machine elements and modern transmission system technology for the multi-megawatt field of mechanical and systems engineering and engineering of vehicles on land, at sea and in the air.
High-power drive trains and the necessary machine elements are our passion. Nevertheless, we have also contributed to groundbreaking developments in the watch industry in the recent past. It all started in 1828 with the foundation of the first Technical College in Dresden. The very first Professor of Mechanical Engineering at this institution was Johann Andreas Schubert, who designed and built the first working steam locomotive in Germany,” Saxonia”. Based on this tradition, outstanding personalities like Richard Stribeck, Karl Kutzbach, Enno Heidebroek and Stefan Fronius, significantly pushed the research in the fields of machine elements and the machines and systems assembled from them. In particular, the research on gears, that was started by Stribeck, intensified by Fronius and continued by Heinz Linke, brought the chair the highest reputation among professionals.
For over two decades, the constantly increasing complexity of modern machines, systems and vehicles on land, at sea and in the air, has illustrated that the deepened analysis of single machine elements is not sufficient any more. The future belongs to engineers able to apply their comprehensive basic knowledge to contexts to understand the entire system behavior of a machine, plant or a vehicle.
In order to meet these demands, all employees of the chair are occupied with the research and improvement of traditional machine elements as well as the analysis and synthesis of the dynamic behavior of complex transmission systems in machines, plants and vehicles. Our current research includes, on the one hand, spur gears, bevel gears, planetary gears, shaft-hub connections, shafts and rolling bearings. On the other hand, we analyze the overall dynamic behavior of wind turbines (onshore and offshore), marine propulsion systems, aircraft engines, bucket wheel drives and chassis of large open-cast mining equipment and mechanical watches, using multi-body simulation. Additionally, servo-hydraulic component tests are used to determine fatigue and endurance strength of machine elements and assemblies. In all cases, special attention is paid to the unity of theory and experiment.
Based on this unique combination of elements and systems, we work on connecting the topics of “strength calculation”, “gear calculation” and “determination of dynamic loads” with the goal of a load-adapted design of dynamically loaded machines, systems and vehicles.
A great number of national and international companies and research associations have already confidently collaborated with us, for which I would expressly like to thank all our partners. We will carry on researching reliably and advising you confidentially in the future. To the student reader, German and European companies for mechanical engineering and systems engineering are strongly recommended as future employers, offering globally outstanding requirements along with excellent working conditions for engineers.
In modern machine, systems and vehicle engineering, the design objective continues to be finding the easiest and in every regard best system solution for specific conditions, using traditional as well as innovative machine elements. Considering the advantages and disadvantages of different solutions is a diverse and responsible task, imposing high requirements on the engineer and designer. With this in mind, all members of the chair will make their contributions through research and teaching to the further development of traditional mechanical engineering with the most contemporary methods, all according to the motto:
Rooted in the past – alive in the present – committed to the future.
With kind regards from Dresden and
on behalf of all our employees
Berthold Schlecht