Motion Technologies
Motivation
In processing machines, a wide variety of moving working elements are used to realize a processing operation. In this context, mostly fast uneven movements, e.g. when feeding products, have to be realized, which meet the requirements of the executed processes. Specially developed non-linear translating gears are often used, but also modern robotic systems.
While criteria such as modularity or low manufacturing costs play an important role in the majority of developments, limitations arise precisely when very fast or demanding movements are required or the product has an inherent behavior that is difficult to control.
Approach
By taking into account the intrinsic behavior of an active unit in the design of the process control, a significant improvement in the reliability as well as the minimum achievable cycle times of processing operations can be achieved. The basis for this is a valid process model, which represents the relevant interactions.
Main focus
The work includes the development and application of methods to increase the performance of processing operations with moving work elements or moving processing goods. In particular, the focus is restricted to the two processing operations "intermittent fluid transport in a container" and "transport of piece goods with vacuum grippers".
Intermittent fluid transport in a container
Intermittent fluid transport frequently takes place in packaging systems in the beverage and pharmaceutical industries. A movement phase is followed by a resting phase in which further processing operations, such as quality assurance or labeling, can take place. Due to the process, it is necessary that there is no slosh of the fluid during the resting phase, and furthermore that there is no loss of fluid during the movement phase. For this purpose, optimal motion designs are calculated which fulfill the technological requirements mentioned and offer considerable advantages with respect to maximum achievable cycle rates compared to conventional motion designs. Investigations into the robust and adaptive design of the process are the subject of current research projects.
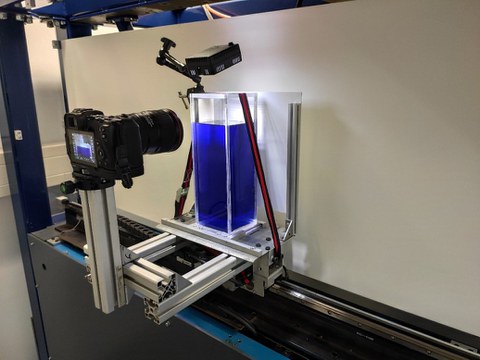
Test rig for the investigation of intermittent fluid transport
Transport of piece goods with vacuum grippers
Loading processes in packaging machines are increasingly being implemented by systems with a free movement function, e.g. robots with a parallel kinematic structure. Their adaptability is a major advantage here. The use of elastic vacuum grippers also allows a high degree of flexibility with regard to the surface properties and geometry of the products. The aim is to reduce the load on the active unit, consisting of vacuum cup and product, by adapting the process control. For this purpose, depending on the gripper design, different process models are used and included in the motion planning. The aim is also to extend the highly simplified process models established in the state of the art in science and technology.

FEM model to illustrate the behavior of an active unit consisting of an elastic suction cup and a packaging with an elastic surface
Technical equipment
For the main research areas, there are test rigs, which are equipped with the corresponding measurement technology. In addition to force and acceleration measurements and the analysis of internal control signals, optical measurement systems are primarily used and evaluated for specific problems (photogrammetry).
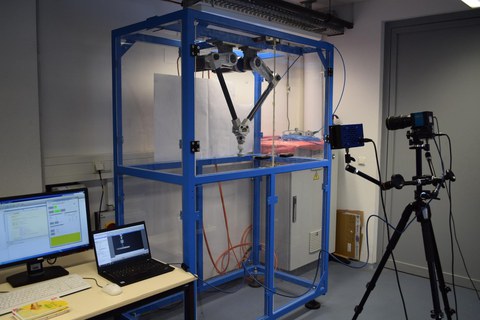
Delta robot with optical measuring system
Click here to see an overview of current research projects.
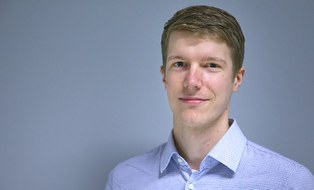
Processing Systems
NameDipl.-Ing. Georg Steinert
Motion Technology
Send encrypted email via the SecureMail portal (for TUD external users only).