Significantly increased efficiency of a final packaging system; Product and cycle rate adapted motion design of the Pick & Place technology
For sorting, transport, insertion or positioning processes in the processing industry, products usually have to be moved with low inertia, but in large numbers and at high speeds. Robots with a parallel kinematic structure represent one possible approach for constructive realization. Due to their design, these have particularly favorable dynamic properties. One widely used design is the DELTA robot, which enables three-dimensional movements to be realized.
Within the scope of the project, an application-specific optimization of the system behavior of a handling device consisting of a DELTA robot with vacuum gripper is to be achieved. The aim is to find an optimum compromise between functional reliability and the highest possible process speed. So far this has been done iteratively and shall now be supported by specific simulation.
Experience shows that above a certain process speed, a loss of contact between product and gripper occurs. Therefore, one focus will be the formation of a valid contact model of the used active unit. Since the application area is clearly defined, a descriptive model will be used.
Based on this model, methods for motion optimization will be investigated, which will first be simulated and then investigated on the test bench with respect to their applicability. The aim is to improve the contact behavior even at high process speeds by specifically adjusting the motion input to the system parameters of the active unit. By using optimized trajectories, an improved maximum quality output is aimed at, which was previously limited by the process behavior.
Aim of the project is the development and integration of an adaptable motion control for the packaging plant of the project partner, which allows the application of optimal trajectories.
Project financing:
The project is funded by “Zentrales Innovationsprogramm Mittelstand (ZIM)” by the Federal Ministry for Economic Affairs and Energy (BMWi).
Project duration:
11/2020-12/2022
Project leader and contact:
Project leader: Prof. J.-P. Majschak
Project management: Dipl.-Ing. Georg Steinert
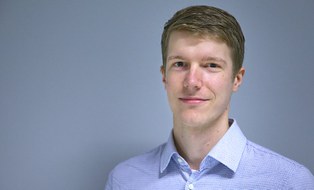
Processing Systems
NameDipl.-Ing. Georg Steinert
Motion Technology
Send encrypted email via the SecureMail portal (for TUD external users only).