Ultrasonic Enhanced Embossing for Small Scale Production of Leather Goods
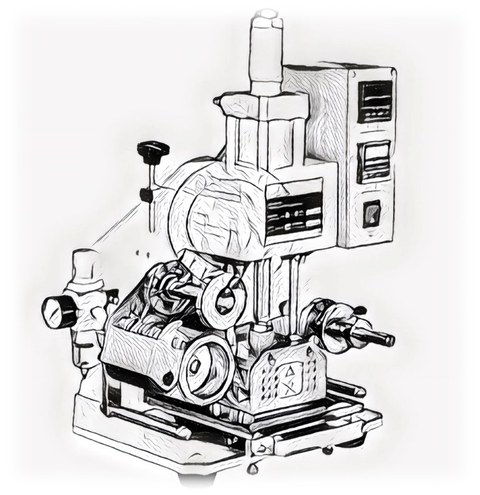
symbolic image of the embossing device for leather products
Process development for ultransonic enhanced embossing of leather products and device for small scale production of embossed leahter goods with additive manufactured tools
Ultrasonic enhanced embossing technology offers an innovative way to meet the demands of the automotive, furniture and apparel industries for the look and feel of leather. Embossing allows large quantities of leather to be produced cost-effectively with reproducible textures, which are for example required for seating surfaces in vehicles and furniture.
Traditionally, the industrial production of such textures has been carried out using an energy-intensive and technically complex process with heated hydraulic presses or in embossing machines with rotating rollers. In addition, conventional embossing tools are expensive because they are made of high-quality steels or alloys that have to withstand the high pressure and temperature requirements during the embossing process. The production of large structures or complex patterns requires time-consuming metalworking processes such as milling or engraving. Quick pattern changes, customer-specific adaptations or even individual one-off pieces were not economically feasible until now and had to be produced manually.
The ultrasonic technology offers promising approaches to support the leather embossing process without heating the embossing tools beforehand, which means that 3D-printed plastic tools with a short service life can be used for small series. This enables more efficient and flexible production.
The focus of the research project is on the development of a prototype of an ultrasonic enhanced embossing device with which leather and leather articles can be embossed using prefabricated 3D-printed plastic stamps. In addition, a process is to be developed within the framework of the prototypical application in order to convert specified images, logos or fonts into 3D printable data files and tools.
Project funding:
The research project is supported by the the Federal Ministry for Economic Affairs and Climate Action through the program "Zentrales Innovationsprogramm Mittelstand".
Project duration:
02.2023 - 03.2025
Partners:
Project management and contact:
Project leader: Prof. Jens-Peter Majschak
Project manager: Dipl.-Ing. André Hofmann
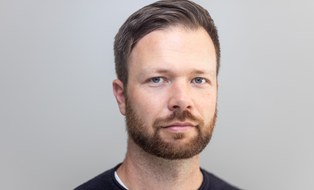
Processing Systems
NameDipl.-Ing. André Hofmann
Forming of fibre-based Materials
Send encrypted email via the SecureMail portal (for TUD external users only).