250 Meter über dem Meer
(porträtiert im Jahr 2012)
Martin Morgenstern
Der Werkstofftechniker Thomas Zwieg beschäftigte sich während seines Studiums mit Korrosion und Oberflächenbehandlung von Werkstoffen und promovierte zu eisabweisenden Beschichtungen. In der Praxis beschichtete er schon einmal dicke Brückenkabel hoch über dem Meer. Heute ist er unter anderem als Produktentwickler für zarte Musiksaiten tätig.
Die Brücke zwischen seinen Fachgebieten schlägt er im Interview mit dem Autor Martin Morgenstern:
Der Beginn Ihres Studiums fiel in die Zeit der politische Wenden. Wenn Sie daran zurückdenken, wie haben sich die Veränderungen an der Universität niedergeschlagen?
Die Wendezeit war eine der spannendsten Perioden meines Lebens, insbesondere das halbe Jahr von den Demonstrationen im Herbst 1989 hin zur ersten freien Volkskammerwahl im März 1990. Hier wurden große Ideale geträumt. Dass die obligatorischen, politischen Vorlesungen nun entfielen und durch zusätzlichen fachlichen Unterricht ersetzt wurden, empfand ich als befreiend. Ich gehörte zum letzten Studienjahrgang mit fester Seminargruppe und festgelegtem Studienplan für das gesamte Studium. Dies war meiner Meinung nach nicht nachteilig. Mein beruflicher Erfolg in Dänemark hat deutlich gezeigt, dass das Ausbildungsniveau an der TU Dresden – insbesondere am Institut für Werkstoffwissenschaft – von sehr hohem, international vergleichbarem Niveau war und ist.
Haben sich mit der Wende Ihre beruflichen Vorstellungen geändert?
Nein. Werkstofftechnik war mein Wunschstudium und ich würde es auch heute nach 18 Jahren Berufserfahrung wieder studieren.
In Ihrer Diplomarbeit bei Prof. Hartmut Worch untersuchten Sie die Korrosionsbeständigkeit in konstruktiven Spalten von Aluminiumwerkstoffen für die Luftfahrt sowie von mit Titanverbindungen beschichteten Dentalwerkstoffen für Zahnimplantate. Sie vertieften sich bereits frühzeitig auf das Thema der Beschichtungen?
Korrosion und die Oberflächenbehandlung von Werkstoffen gehörten eindeutig zu meinen Lieblingsfächern im Studium. Beide Fachgebiete, insbesondere jedoch die funktionelle Oberflächenbehandlung, bestimmen seitdem auch in hohem Maße meine berufliche Tätigkeit.
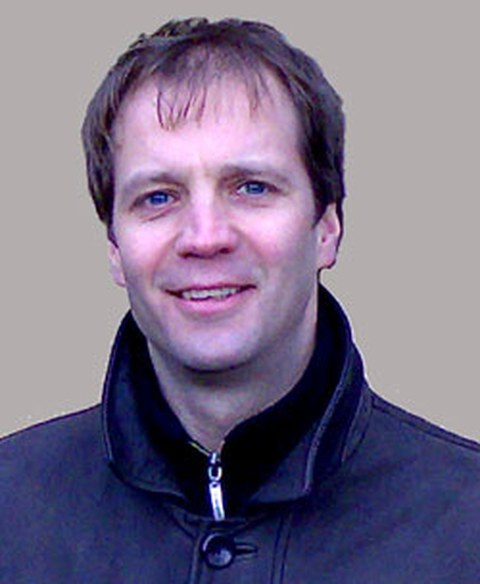
Dr. Thomas Zwieg
Sie gingen 1992 ein halbes Jahr nach Dänemark, zum Ingenieurpraktikum ans Dänische Technologische Institut (DTI). Nach Studien-Ende 1994 wurden Sie am DTI fest angestellt und arbeiteten dort bis 2007, zuletzt als Gruppenleiter in der Materialforschung. Worin bestand Ihre Tätigkeit?
Anfangs arbeitete ich in einem Forschungsprojekt zur Lebensdauerberechnung von kritischen Kraftwerkskomponenten mit, in dem ich Korrosionsprozesse in Ermüdungsrissen und deren Einfluss auf das Risswachstum untersuchte. Später folgten verschiedene Projekte zur Oberflächenbehandlung von Aluminiumwerkstoffen. Dabei vertiefte ich mich in die sogenannte „Sol-Gel-Technologie", eine nass-chemische, nanotechnologische Beschichtungsmethode. Diese Technologie hatte ich zugrunde gelegt, als ich 2002 meine eigene Arbeitsgruppe zu funktionellen Beschichtungen aufbaute, der zuletzt sechs akademische Mitarbeiter angehörten.
Im Jahr 2006 folgte Ihre Doktorverteidigung an Ihrem ehemaligen Dresdner Institut. Sie hatten sich mit eisabweisenden Beschichtungen beschäftigt ...
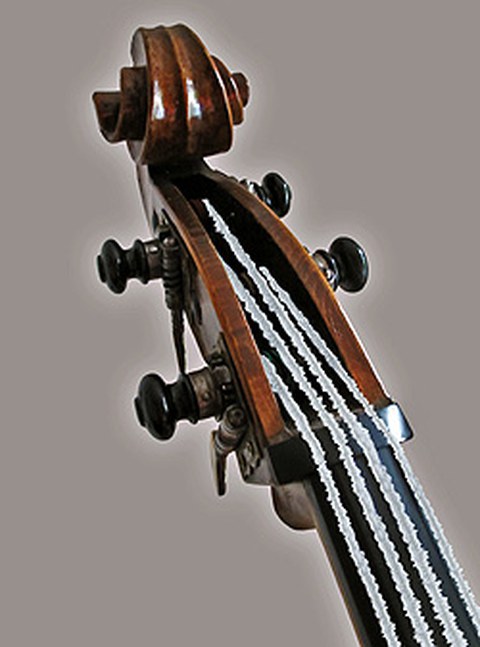
Früher entwickelte der Werkstoffwissenschaftler Dr. Thomas Zwieg eisabweisende Beschichtungen, heute neuartige Saiten für Streichinstrumente.
Meine Doktorarbeit mit dem Thema „Biomimetical ice nucleating surfaces" zielte darauf ab, Oberflächen mit eisbildenden und eisabweisenden Eigenschaften zu entwickeln. Solche Oberflächen sind beispielsweise gesucht, wenn in der Kältetechnik Eis erzeugt werden soll. Dafür wählte ich einen neuen, biomimetischen Lösungsweg. Ich ließ mich von an arktische Kälte angepassten Lebewesen inspirieren, deren Zellmembran eine kontrollierte Eisbildung ermöglicht, ohne dass das Eis an dieser haften bleibt. Die genaue Struktur und Wirkungsweise dieser Zellmembran ist noch immer nicht gänzlich geklärt und wird deshalb weiterhin erforscht. Der von mir abgeleitete Wirkmechanismus funktioniert jedoch sehr gut. Die Herausforderung bleibt, wie solche Oberflächen in der praktischen Anwendung lange stabil bleiben.
Stimmt es, dass Sie vier Patente halten, unter anderem für Beschichtungen gegen Eis und gegen Graffiti?
Bisher ist mir das Patent zu den biomimetischen eisbildenden und eisabweisenden Oberflächen weltweit erteilt worden, das ich bereits 2001 eingereicht hatte. Das andere sind laufende Verfahren.
Stichwort „eisabweisende Oberflächen" – da gab es ja ein richtiges Abenteuer für Sie „über" dem Großen Belt ...
Mit dem Großen Belt verbindet sich eine meiner schönsten Aufgaben: die Beschichtung eines Abschnitts vom Hauptkabel der Brücke über den Großen Belt – in 250 m Höhe über dem Meer. Solch ein Erlebnis gibt wahrscheinlich keine Achterbahn der Welt. Auf dem Kabel zu stehen ist dabei das eine. Die Sicherheitskabel aber loszulassen und beim Beschichten seitlich dieses Kabels an der Sicherheitsleine zu schweben, wenn zusätzlich noch starker Wind herrscht, etwas ganz anderes. Wir haben seinerzeit Versuche mit einer eisabweisenden Beschichtung an diesem Kabel durchgeführt.
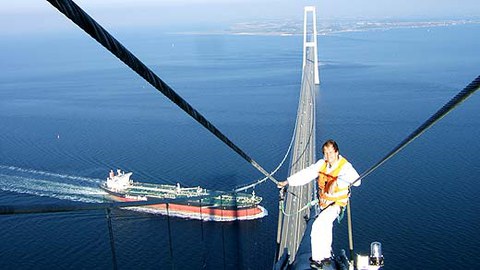
In 250 m Höhe über dem Großen Belt beschichtet Dr. Zwieg ein Hauptkabel.
Ergänzend zu Ihrer Tätigkeit als Ingenieur haben Sie Kurse in Projektmanagement, Fundraising oder Ökonomie besucht. Inwieweit eröffnen solche ergänzenden Weiterbildungen einem Ingenieur neue Möglichkeiten und Berufsfelder?
Dieses Wissen ist heute für den Ingenieur unabdingbare Voraussetzung für eine erfolgreiche Arbeit. Nicht nur in der universitären Forschung, auch in den Entwicklungsabteilungen der Firmen wird in Projekten gedacht, geplant und gehandelt. Für alle diese Projekte müssen finanzielle Mittel beantragt bzw. eingeworben werden, oft auch in den Firmen. Insbesondere in der öffentlichen Forschung wird durch die ständige Jagd nach Geld und die umfangreichen Antragsverfahren aus meiner Sicht enorm viel wissenschaftliches Potenzial vergeudet.
Heute sind Sie bei einem namhaften Hersteller von Musikinstrumentsaiten als Produktentwickler beschäftigt. Worin besteht Ihre Arbeit?
Ich leite unsere Abteilung für Produktentwicklung und bin für die Entwicklung neuartiger Musiksaiten verantwortlich sowie dafür, dass bereits bestehende Produkte ständig verbessert werden. Unsere Firma Larsen Strings gehört zu den weltweit führenden Herstellern von Musiksaiten für Streichinstrumente. Unsere Saiten werden hauptsächlich von professionellen Musikern in den Symphonie- und Opernorchestern gespielt. Diese Musiker sind qualitativ höchst anspruchsvoll und haben sehr individuelle Anforderungen an ihr Instrument und dessen Besaitung. Es ist eine große fachliche Herausforderung, die von den Musikern gewünschten klanglichen Attribute in messbare, technische Werkstoff- und Verarbeitungsparameter zu übertragen. Und auf dieser Grundlage Musiksaiten zu entwickeln, die diese Anforderungen vollauf befriedigen können. Dies erfordert besonderes musikalisches Gehör und Verständnis. Die Entwicklungsarbeit für solche Saiten dauert in der Regel mehrere Jahre. Streichersaiten sind viel komplexer aufgebaut, als man sich im Allgemeinen vorstellt. Dabei sind sehr umfangreiche akustische und spieltechnische Tests sowohl im Labor als auch gemeinsam mit Musikern im Konzertsaal notwendig. Deshalb ist es immer wieder ein besonderer Höhepunkt, wenn neue Saiten auf dem Markt eingeführt werden. Ein unglaublich großer Motivationsfaktor ist es, unsere Saiten weltweit bei berühmten Orchestern und Solisten im Konzert zu hören.
Verfolgen Sie die Geschicke Ihrer ehemaligen Universität?
Ja, zum Beispiel über die Homepage. Die Universität ist ja unglaublich gewachsen und Forschung aus Dresden ist in Dänemark bekannt und geschätzt. Die Auszeichnung zur Exzellenz-Universität hat mich sehr gefreut. Mein besonderes Interesse gilt natürlich den aktuellen Aktivitäten am Institut für Werkstoffwissenschaft.
Was hätten Sie sich damals an der TUD anders gewünscht – bzw. welche Tipps hätten Sie für uns in punkto Wissenschaftsphilosophie, Forschung und Entwicklung und den erfolgreichen Übergang in den Beruf?
Persönlich habe ich rückblickend keine Wünsche. Als wichtig erachte ich die zusätzliche Ausbildung in der Methodik: Wie formuliert und leitet man Projekte und wie sollten Fachpublikationen verfasst werden. In Dänemark wird eine bestimmte Anzahl referierter Fachpublikationen über das Forschungsthema vorausgesetzt, damit man einen akademischen Grad erlangen kann.
Bildet die TUD in den Ingenieurwissenschaften aus Ihrer heutigen Sicht fach- und bedarfsgerecht aus?
Eine allgemeine Einschätzung fällt mir schwer, da es sehr viele Fachrichtungen an der TUD gibt. Ich kann für die Werkstoffwissenschaft sprechen, deren Ausbildung ich als eindeutig fach- und bedarfsgerecht einschätze. In der heutigen Zeit des zumeist großen (Über-)Angebots ist es wichtig, sich bei hohem fachlichem Niveau zusätzlich zu differenzieren. Dies gilt sowohl für Produkte als auch für unser Fachwissen und -können. Als ich nach Dänemark kam, war mein Fachwissen gut vergleichbar mit dem meiner dänischen Kollegen. Dennoch unterschied sich die Gewichtung und Tiefe dieses Fachwissens. Meine Kollegen wussten sehr viel mehr darüber, wie man metallische Werkstoffe erzeugt, insbesondere Metalle gießt. Ich hatte eine wesentlich breitere Sicht auf Werkstoffe, insbesondere auf die Struktur- und Eingenschaftsbeziehungen, die neben den Metallen auch die keramischen und die polymeren Werkstoffe – ja selbst Biomaterialien – mit einschloss. Diese seinerzeit von Professor Schatt eingeführte und von Professor Worch weiter vertiefte, gleichwertige Betrachtung der metallischen, polymeren, keramischen und biologischen Werkstoffe hat sich in meiner beruflichen Arbeit als großer Kompetenzvorteil in der Herangehensweise an gestellte Aufgaben erwiesen.
Update 2020:
Heute, acht Jahre nach dem Interview für das Absolventenportrait arbeite ich noch immer bei der Firma Larsen Strings A/S als Leiter der Produktentwicklung. Zusätzlich bin ich seit 7 Jahren auch stellvertretender Direktor unserer Firma. Die Arbeit mit den und für die Musiker ist und bleibt mir eine große Erfüllung. Meine vier Töchter sind inzwischen erwachsen. Die drei jüngsten studieren in Dänemark sowie in Deutschland. Die Älteste hat ihr Studium bereits abgeschlossen und meine Frau und ich sind gerade zum zweiten Mal Großeltern geworden. Man kann mit Sicherheit in vielen Ländern der Welt spannende und erfüllende Tätigkeitsfelder finden und glücklich werden. Was Dänemark auszeichnet, ist die soziale Sicherheit und die sehr familienfreundliche Arbeitspolitik, wo jeder, unabhängig vom Beruf, öffentlichem oder privatem Arbeitsgeber eine geregelte Arbeitszeit in Anspruch nehmen kann und damit immer ausreichend Zeit für die eigene Familie hat. Die Familie wird in Dänemark im Allgemeinen höher priorisiert als die Arbeit. Die Qualität der Arbeit leidet darunter nach meiner Erfahrung in keiner Weise. Ganz im Gegenteil wirkt diese Akzeptanz motivierend und ist einer der Hauptgründe dafür, dass ich nunmehr seit 25 Jahren hier lebe.
Kontakt:
LARSEN STRINGS A/S
Dr. Thomas Zwieg
Manager Product Development