“I’ve always enjoyed construction”
(portrayed in 2023)
Dagmar Möbius
Maximilian Hansen began studying architecture after spending three years attending law lectures. That took him seven years, because he was working in between. The experience still helps him today. While he worked on the Sagrada Familia as a student and created a conservation concept for a Persian temple complex for his thesis, he is now focusing on sustainable trade show construction, event equipment and paper architecture with his own company.
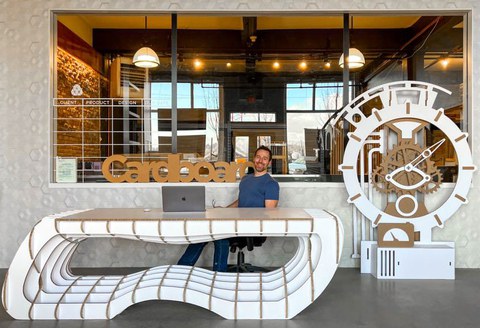
Maximilian Hansen with one of his paper products.
“I can see the Pacific Ocean, and on the other side the mountains,” is how Maximilian Hansen describes the view from his window during the video call. It’s ten o'clock in the morning for him in Vancouver, and 7 o'clock in the evening in Germany. The 41-year-old has a lot of business in North America. Born in Dresden, he spent his childhood in West Berlin. When he returned with his parents at the age of ten, the city on the Elbe seemed very dull to him, in contrast to the very colorful Berlin. “Today I say I'm East German,” he laughs. Knowing very well that even to his wife, a Canadian, he finds it difficult to explain the subtle differences.
After graduating from high school and joining the army, Maximilian Hansen first studied law for three years at TU Dresden. At school, he found mathematics and physics difficult – so he wanted to do something different. “But then I got fed up with prefabricated patterns,” he says. A friend of him was studying architecture and complained about how awful that was. Maximilian Hansen was attracted to just that: “I’ve always enjoyed construction.” He studied from 2005 to 2012. Since his parents' construction company became insolvent, his sister and himself, at that time in the 4th semester, could no longer be supported. He was not granted BAFÖG because he lacked a language certificate. “I worked in drywall construction for five or six years,” Maximilian Hansen says. “One semester I worked a lot, one semester I studied a lot. You can see that in my grades, too: 3.0 - 1.0 - 3.7 - 1,0.” The comment by one of his lecturers, that he should know what really matters, sounded arrogant to him. Today, he acknowledges: “She was pretty much right on the money.”
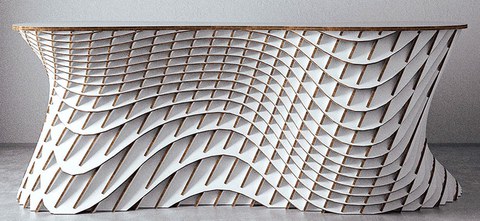
Paper architecture is part of the program of Nordwerk Design.
Looking back, he describes studying architecture as “quite design-oriented and therefore rather detached from reality” – at least in relation to what he is doing today. “At the time, neither the computer skills that were relevant in practical life were taught, nor were building materials and material-related options sufficiently explored in depth. There were 1,000 students for just 24 CAD workstations in my day, and there were hardly any student licenses for relevant software, so we had to rely on the CAD workstations,” he mentions one example. Nevertheless, he learned all sorts of skills that he still appreciates today: constructive and technical aspects of building and the permanent presentation of projects.
Maximilian Hansen describes himself as fortunate that he was able to work on practical and structurally demanding projects with his professors Christoph Schulten (structural design) and Prof. Dr. Wolfram Jäger (structural engineering), for example on the Sagrada Familia in Barcelona. “At one point, Professor Jäger talked about the challenges of mapping the rubble of the Frauenkirche in Dresden and why he did it anyway. That helped me in a business sense, because it showed that in areas where there is little knowledge or where the knowledge that exists is not readily available, a little courage, common sense, and solid engineering skills can lead the way as you solve one problem at a time.” Maximilian Hansen realized that tasks that seem complex can be simplified if you think about from a constructional structure perspective. He is still working that way today.
For his final thesis, the Diplom engineer in architecture developed a consolidation concept for the 40-meter-high ruins of a temple complex in Iran. He used ancient surveying methods to do so. His thesis was nominated for the Saxon Construction Industry Award and the Kurt Beyer Prize. Whether his concept was implemented is unknown: “Political quarrels got in the way.” After his graduation, Maximilian Hansen worked at the Chair of Building Construction at TU Dresden for one and a half years. In his free time, he developed the basic concept for his current company with Daniel Fucke (the later co-founder; he left the company in 2017). “You should never underestimate the role of pub,” he laughs. “Drinking beer is good for visionary brainstorming.”
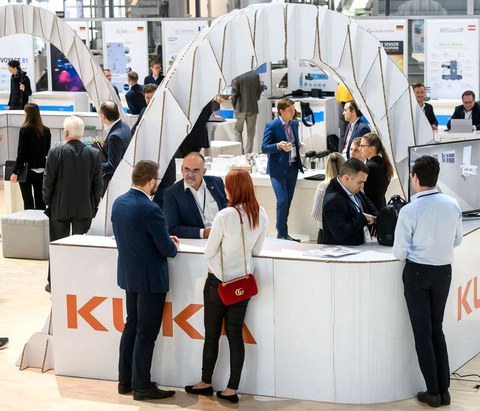
Exhibition buildings at the HighTech Venture Days Dresden
In 2013, Nordwerk Design was founded with youthful vigor. “We had been experimenting before, but we needed to learn how trade show construction works,” he says. During your studies, nobody explains to you how temporary buildings work. It was a tough time, but we believed in it.” The banks didn't approve any loans. They said there was no money to be made with this idea. “There are one-dimensional personalities sitting there,” Maximilian Hansen tries to explain. “Trade shows produce inconceivable amounts of waste, and even though paper is a raw material, in Germany you have to pay to dispose of it.” In fact, while his solution is green, it's not necessarily cheaper. While trade show booths can be used multiple times, the packaging is sometimes as expensive as building a new one. The engineer identifies the perception of paper as the number one problem in his industry: “The properties are unknown, for example, paper can absorb water – and regarding fire protection: High-quality paper material panels are classified like lumber. In China and Japan, they use them in construction. But that is swept under the carpet. In Germany, the breakthrough will take another ten to fifteen years,” he estimates.
The one large paper trade show booth he and his team built for Volvo in Toronto and Vancouver had only one roll of duct tape that was not recyclable. “Sustainability is taken very seriously there,” he praises. For a U.S. series, he supplied furniture. Otherwise it’s hard to get a foot in the door of film productions, he says. Prior to Covid, the Nordwerk team realized around 20 projects a year. They have cooperation partners all over the world. “We produce and print our products ourselves. During the pandemic, we were able to keep ourselves afloat with data sets,” says Maximilian Hansen. Students and alumni of TUD and HTW could no longer be employed because the trade show industry was immediately and very strongly affected by the pandemic.
Currently, the industry has not yet fully recovered, there are ten projects on the books. One major project that has shown the potential of the industry was a 1,600 square meter paper exhibition stand in New Orleans. At present, the company is furnishing North American stores of a sporting goods manufacturer. A not so demanding mass production. However, “Things that are not an eye-catcher are financing the business,” says the Nordwerk Design founder, who is now running the company on his own. Even though he tours worldwide, the company's location will continue to be in Dresden's Friedrichstadt district. And he is in regular contact with his university via the alumni network.
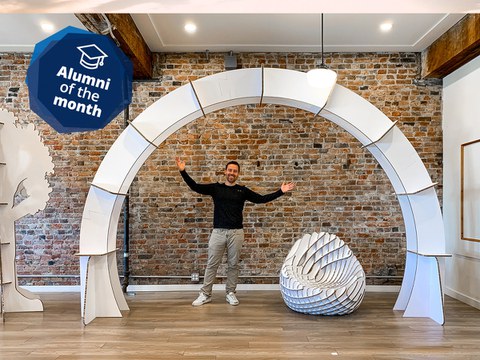
Maximilian Hansen is the graduate of the month for October 2023.
Contact:
Maximilian Hansen
Nordwerk Design