HR manager Pilz is professionalizing personnel administration
(Interview from 2003)
Susann Mayer
A cooperation agreement to reduce or completely eliminate the distance that can still exist between research and industry – that was the hope expressed by TU Rector Prof. Achim Mehlhorn as he signed the agreement between Edelstahlwerke GmbH (previously Sächsische Edelstahlwerke GmbH) and TU Dresden on nurturing young researchers.
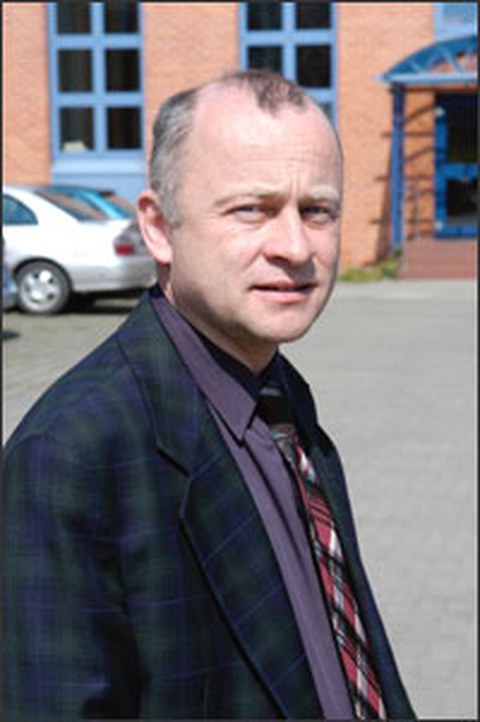
Dietmar Pilz
Dietmar Pilz, HR manager at BGH Edelstahlwerke Freital GmbH and a graduate of TU Dresden, knows how important this project is. The main focus of the partnership, established on April 14, 2003, is organizing internships for TUD students to provide practical training. The partnership is of particular interest to the company, as it provides access to the latest scientific and research developments, helping solve problems at the interface of theory and practice.
The 48-year-old Pilz is aware of the expertise and capabilities on both sides. In the 1970s, he trained as a maintenance mechanic (vocational training with Abitur high school diploma) at the Edelstahlwerk Freital plant. The factory's history of steel production and processing goes back to Sächsische Gußstahlfabrik, founded in 1855. In the GDR, the plant became the largest stainless steel producer in the country, with 5000 employees melting 300,000 metric tons of crude steel every year. Production ranged from low-alloy structural steels to nickel and titanium alloys. Nowadays, BGH Edelstahlwerke GmbH has sites in Freital, Lippendorf, and Lugau, and is one of the largest employers in Saxony. The Freital plant has specialized in 800 different special steels. Industry has lower quantity and high quality demands for such custom steels. Buyers need smaller volumes, but also a flexible response to changing market requirements in this sector. From specially coated wires for incandescent bulbs and stainless steel for medical instruments to valve materials, BHG has adapted to its customers’ demands.
He explains his decision to study at TUD as follows: "In the GDR, TUD was considered THE university, perhaps alongside Humboldt-Universität in Berlin. I was also spurred on by my school principal, who said that the admissions requirements for TUD were very high and it did not make much sense for me to apply, as I only had decent to average grades."
He dared to apply anyway and was accepted to study labor engineering in 1977. "During my vocational training, I realized that studying a purely technical discipline (mechanical engineering, materials science, or automotive engineering) was not for me. I was looking for an engineering discipline that was all about creating ideal, effective interaction between working people, equipment, and resources through the strategic organization of working processes. So my studies were interdisciplinary with subjects such as – as far as I can remember – engineering mechanics, technical drawing, manufacturing and materials technology. Plus the foundation subjects of chemistry, math, and physics, and labor engineering courses such as job design, occupational psychology, occupational medicine, and occupational safety."
His expertise proved useful when he returned to Edelstahlwerke in 1982 and became responsible for work design in the "Work Organization" department. As he was the only one in the 10-person department who had trained as a labor engineer, he took on the management of the entire department in 1989. "Following the fall of the Berlin Wall and the reunification of Germany, what I learned in my degree is of less use to me today. But there are some relevant aspects in specific individual tasks, for example occupational health evaluations, job descriptions, calculating allowances for difficult working conditions under collective bargaining agreements, and assessing staffing requirements."
Since 1994, he has been head of human resources, where he is responsible for 450 employees. Drawing up and implementing social compensation plans and improving the age structure of the company are not the only areas for which he is responsible. He has also introduced a flexible working model and developed a graduate trainee program.
Equipping students for practice has always been a top priority at TUD. The partnership that has now been agreed offers exciting opportunities for students from the science and engineering faculties in particular. Pilz anticipates that the partnership will enable TU students from all disciplines to add practical experience to their knowledge of theory while they are still at university, whilst also establishing links that could help them in their future career. In his view, the arrangement is a way of bringing young people into industry at an early stage and giving them the opportunity to find out about a business with high-tech and highly complex working and production processes firsthand. The partnership is also designed to make the best possible use of existing resources by sharing research findings and expertise.