Burning desire for thermoplastic composites
(Interview from 2022)
Dagmar Möbius
A stop along the Elbe river during a cycling trip inspired Christian Garthaus to move to Dresden after graduating from high school. As a child, the Bremen native dreamed of becoming a tentmaker and had heard of TUD’s unusual “Industrial Design Engineering” degree program. He has now lived in Dresden for 20 years and established his own company in the city four years ago.
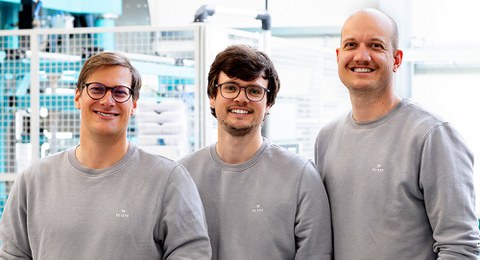
The founding team. Form left to right::Daniel Barfuß, Alexander Rohkamm, Dr. Christian Garthaus
Math and art were his favorite subjects in school. “But it took me a while to decide on a career path,” recounts Dr. Christian Garthaus. A cycling trip after graduating from high school set him on the right track – albeit by chance. During a stop in Dresden, he not only found the city to his liking – he also discovered the “Industrial Design Engineering” degree program. It was exactly what he had been looking for. “Design in relation to mechanical engineering; two interconnected worlds found only at a few universities.” Garthaus began his studies in 2002 at TU Dresden and graduated in 2009 with a Diplom-Ingenieur degree in Lightweight Engineering and Polymer Technology. There were stints abroad at the Universidade Federal da Bahia in Brazil, Nanyang Technological University in Singapore and a company in the United Kingdom along the way. However, his clearest memories remain “the huge institute with loads of equipment for testing and experiments” and the annual excursion week, which involved visiting numerous companies.
After completing his Diplom, Christian Garthaus remained at TUD as a Research Associate. Together with his research group, he investigated and developed technology for composite parts. He explains, “Composites have been around for decades. It’s a type of material that combines carbon or glass fibers with synthetic materials. We were working in collaboration with Boeing on a new technology for manufacturing thermoplastic composite parts. By using a thermoplastic synthetic material and a combination of a special braiding method with an efficient pressing process, we were able to automate the process for creating components and produce them in industrial proportions. The finished parts are ultralight, recyclable and made-to-measure for each application. In 2017, Christian Garthaus submitted his dissertation, titled “On the production of a functional hollow profile structure made from continuous fiber-reinforced thermoplastics”. Then came the question of how and where this new technology could be applied.
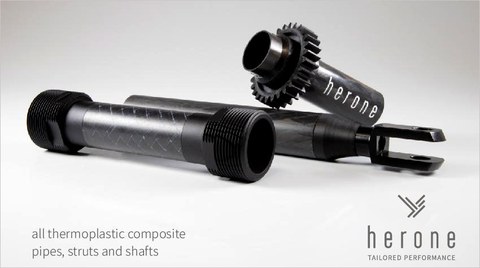
Thermoplast composite materials: pipes, struts and shafts
heroneTechnology
Using automated processes for braiding thermoplastic tapes followed by consolidation in an internal pressure-based pressing process, herone technology enables the production of hollow thermoplastic composite materials in a resource-efficient and cost-effective manner. These completely forgo metals, but not their advantages. Metal fasteners are made from the same thermoplastic base material, making the composite parts fully recyclable.
In January 2018, Dr. Christian Garthaus founded herone GmbH in Dresden together with Daniel Barfuß and Alexander Rohkamm. After the engineering start-up began generating revenue, they celebrated two milestones in the spring of 2022: They moved into their new 1000 m² production hall and successfully completed the AS/ EN 9100 aviation certification to boot. “We’re now service providers and manufacturers,” said the 40-year-old managing director. The cost-efficient fiber composite tubes come into use wherever weight, movements or fluids are transferred, including in aviation, medical technology or sports. This year, herone GmbH presented their thermoplastic composite products as a manufacturer at JEC World, a specialist trade show in Paris for the first time. "These range from integral turbine enclosures for air taxis to pre-stressed hood struts and cables for transporting hydrogen," says Dr. Christian Garthaus.
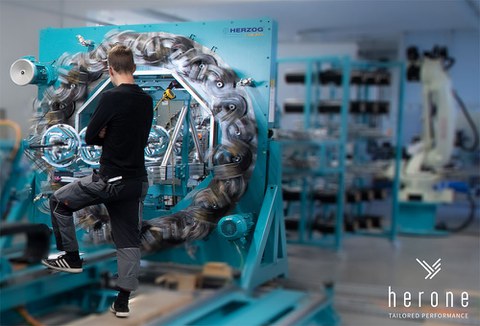
Automated braiding process for thermoplastic tapes.
The automated braiding process for thermoplastic tapes
Together with his team, Christian Garthaus is extremely optimistic about the future thanks to a 4.6-million investment in herone technology. Eleven of the company’s thirteen employees come from Dresden. There are also a few young people completing their internship or writing their research projects at the company. His favorite products for home use are the bicycle parts. “We've put a lot of passion into strut components for aviation,” explains Christian Garthaus, who is an avid cyclist in his spare time. "I've been doing this for 14 years now, and we're still working towards building an airborne part. It’s a long road to get new technology onto an airplane, but it's starting to feel like a reality," he laughs.
Contact:
Dr. Christian Garthaus
GF herone GmbH
Meschwitzstraße 21
01099 Dresden
Tel.: +49 174 9190 621
E-Mail
Web
LinkedIn Profile