Viel Herzblut für thermoplastische Composite
(porträtiert im Jahr 2022)
Dagmar Möbius
Ein Stopp während einer Fahrradtour entlang der Elbe führte Christian Garthaus nach dem Abitur nach Dresden. Der Bremer, der als Kind Zeltbauer werden wollte, hatte vom seltenen Studiengang „Technisches Design“ an der TUD gehört. Nun ist er schon seit 20 Jahren Dresdner und hat hier vor vier Jahren ein Unternehmen gegründet.
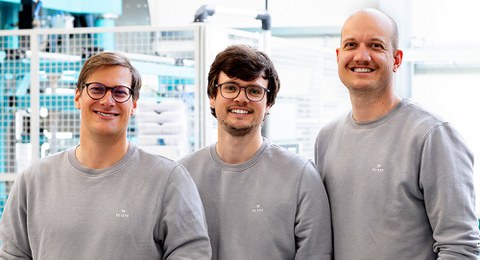
Das Gründerteam von links: Daniel Barfuß, Alexander Rohkamm, Dr. Christian Garthaus
Mathematik und Kunst waren seine Leistungsfächer in der Schule. „Mit meiner Berufsentscheidung war ich aber relativ spät dran“, erzählt Dr. Christian Garthaus. Erst eine Fahrradtour nach dem Abitur brachte ihn auf die Zielgerade – wenn auch zufällig. Bei einem Stopp in Dresden fand er nicht nur die Stadt sympathisch, sondern entdeckte auch den Studiengang „Technisches Design“. Das war genau das, was er gesucht hatte: „Design, das an Maschinenbau aufgehängt ist, zwei verbundene Welten, die es nur an wenigen Universitäten gibt.“ 2002 begann er sein Studium an der TU Dresden und beendete es 2009 als Diplom-Ingenieur für Leichtbau und Kunststofftechnik. Dazwischen lagen Auslandsaufenthalte an der Universidade Federal da Bahia in Brasilien, an der Nanyang Technological University in Singapur und bei einem Unternehmen in Großbritannien. In Erinnerung blieb ihm vor allem das „Rieseninstitut mit viel Equipment für Versuche und Experimente“ und die jährliche Exkursionswoche, bei der zahlreiche Firmen besucht wurden.
Nach dem Diplom blieb Christian Garthaus als wissenschaftlicher Mitarbeiter an der TUD. Mit seiner Arbeitsgruppe erforschte und entwickelte er eine Technologie für Composite-Bauteile. Er erklärt: „Composite gibt es schon seit Jahrzehnten. Das ist ein Werkstoff, bei dem die Carbon- oder Glasfasern mit Kunststoff kombiniert werden. Wir arbeiteten – gemeinsam mit Boeing – an einer neuen Technologie für die Herstellung von thermoplastischen Composite-Bauteilen. Durch die Verwendung eines thermoplastischen Kunststoffs und die Kombination eines speziellen Flechtverfahrens mit einem effizienten Pressvorgang können die Bauteile automatisiert und in großen Stückzahlen hergestellt werden. Die gepressten Bauteile sind ultraleicht, recycelbar und maßgeschneidert für die jeweilige Anwendung. 2017 promovierte Christian Garthaus „Zur Herstellung funktionalisierter Hohlprofilstrukturen aus endlosfaserverstärkten Thermoplasten“. Nun stellte sich die Frage, wie und wo sich die neue Technologie anwenden lässt.
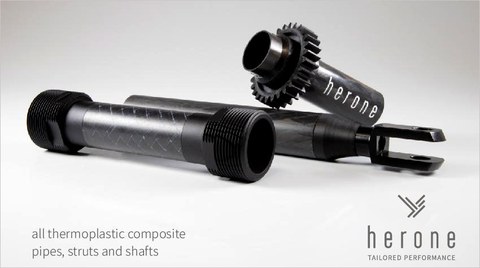
Thermoplastische Verbundwerkstoffe: Rohre, Streben und Wellen
Die herone-Technologie
Basierend auf dem automatisierten Verarbeiten thermoplastischer Tapes im Flechtverfahren und anschließender Konsolidierung in einem innendruckbasierten Pressverfahren, lassen sich mit der herone-Technologie thermoplastische Composite-Hohlprofile ressourcenschonend und kosteneffizient herstellen. Diese verzichten vollständig auf Metalle, nicht aber auf deren Vorteile. Ehemals metallische Verbindungselemente werden aus dem gleichen thermoplastischen Grundwerkstoff gefertigt, so dass die Verbundbauteile vollständig recycelbar sind.
Im Januar 2018 gründete Dr. Christian Garthaus mit Daniel Barfuß und Alexander Rohkamm die herone GmbH in Dresden. Nachdem das Start-up bisher schon als Ingenieurdienstleister Umsatz generierte, wurden im Frühjahr 2022 zwei Meilensteine gefeiert: Die neue 1000 Quadratmeter große Produktionshalle wurde bezogen und die Luftfahrt-Zertifizierung AS/ EN 9100 konnte erfolgreich abgeschlossen werden. „Ab jetzt sind wir Dienstleister und Produzent“, sagt der 40-jährige Geschäftsführer. Die kosteneffizienten Faserverbund-Profile kommen dort zum Einsatz, wo Lasten, Bewegungen oder Flüssigkeiten übertragen werden: natürlich in der Luftfahrt, in der Medizintechnik oder im Sport. Erstmals präsentierte die herone GmbH in diesem Jahr auf der Fachmesse JEC World in Paris ihre Produkte aus thermoplastischen Composites als Produzent. „Die reichen von einer integralen Turbinenumhausung für Flugtaxis über vorgespannte Motorraumstreben bis hin zu einem Leitungssegment für den Transport von Wasserstoff“, so Dr. Christian Garthaus.
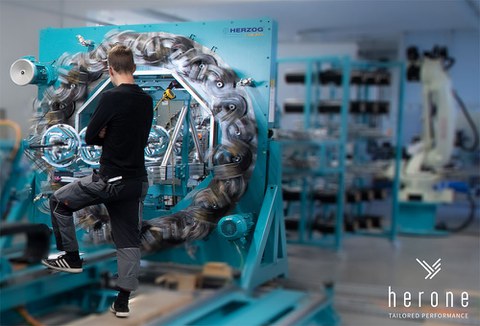
Das automatisierte Flechtverfahren für die thermoplastischen Tapes.
Das automatisierte Flechtverfahren für die thermoplastischen Tapes
Mit seinem Team sieht er angesichts der 4,6-Millionen-Investition in die herone-Technologie sehr optimistisch in die Zukunft. Von 13 Mitarbeitenden kommen elf von der TU Dresden. Zusätzlich absolvieren zwei, drei junge Menschen ein Praktikum oder schreiben ihre Forschungsarbeiten im Unternehmen. Sein Lieblingsprodukt für den privaten Gebrauch sind Fahrradkomponenten. „Wir haben viel Herzblut in Strebenbauteile für die Luftfahrt gesteckt“, sagt der Ingenieur, der privat lieber Fahrrad fährt als selbst fliegt. „Ich mache das jetzt seit 14 Jahren und wir sind noch immer auf dem Weg zu einem fliegenden Teil. Es ist ein langer Weg, mit einer neuen Technologie ins Flugzeug zu kommen, doch langsam wird es real“, lacht er.
Kontakt:
Dr. Christian Garthaus
GF herone GmbH
Meschwitzstraße 21
01099 Dresden
Tel.: +49 174 9190 621
E-Mail
Web
LinkedIn-Profil