Sep 30, 2024
Promotion Dennis Birkner
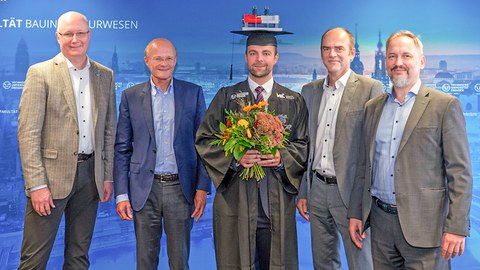
Dennis Birkner and the doctoral committee present
On 26.09.2024, Mr. Dennis Birkner, M.Sc. successfully defended his scientific thesis as part of the doctoral procedure with the topic "Damage development and stress redistributions in fatigue-loaded concrete compression zones". In addition to the chairman of the doctoral committee, Prof. Dr. Viktor Mechtcherine (Technische Universität Dresden), Prof. Dr. Steffen Marx (Technische Universität Dresden), Prof. Dr. Josef Hegger (RWTH Aachen University) and Prof. Dr. Stefan Löhnert (Technische Universität Dresden) were present as reviewers.
Abstract:
The fatigue behavior of concrete has so far been studied intensively in the literature using centrically loaded cylindrical specimens. Only a few studies have been carried out on concrete structures subjected to cyclic bending loads. Such structures can be found in wind turbine towers, for example. Research results for high-strength concrete, which is usually used in such structures, are even scarcer. Due to the high number of occurring load cycles and the large cross-sectional dimensions, the testing of the fatigue behavior of such structures is associated with major challenges. Numerical simulations, in contrast, enable the investigation of a large number of parameter variations within a very short period of time, which accelerates the investigation of the fatigue behavior of components. The used material models quickly become very complex and require time-consuming calibration of the input parameters in structural tests. A model for simulating the macroscopic damage processes in concrete subjected to fatigue loading in compressed cross-sections, which can be calibrated using standard cylinder tests, does not yet exist.
The present work addresses these aspects and implements an additive strain model to simulate the strain and damage development of concrete subjected to fatigue bending loads. A three-step approach was chosen for this purpose. In the first step, experimental investigations were designed and carried out. The tests are essential for the numerical model and were carried out on cylindrical and beam-shaped specimens. The input parameters for the material model were determined from static and cyclic tests on the concrete cylinders and the beam tests were used to validate the model. The beam tests were carried out in a resonance-based testing facility, which allowed the realization of the required high forces with load frequencies of 19 Hz. This made it possible to apply the high number of load cycles in a short time. In the second step, the strain model was implemented in the simulation procedure of the finite element software ANSYS Mechanical. The functions for the stiffness and strain development were derived from cylinder tests. In the third step, the numerical implementation was validated using the beam tests. Different phenomena were considered, such as the temperature and strain development as well as the changes in material stiffness and the resulting stress redistributions in the cross-section.
In the experimental investigations of the beam specimens, fatigue failure due to spalling of the concrete compression zone or complete destruction of the beams was achieved using the resonance-based testing facility. All beams endured significantly more load cycles than the number of cycles to failure according to fib Model Code 2010. This was due to early damage and a reduction in stiffness in the most heavily loaded regions, which subsequently led to a reduction in stresses. The numerical simulations confirmed the effects observed in the beam tests. In particular, the model was able to simulate the most damaged regions very well. Moreover, it was shown that stresses redistributed to less heavily loaded regions as a result of the relief of the damaged regions. This confirmed the positive effect of stress redistributions on the fatigue life of the structures. The model can be used to carry out parameter studies with varying load levels or degrees of prestressing, for example, in order to gain valuable insights into the predimensioning of fatigue-loaded structures and to identify critical locations in the geometry. For more detailed conclusions, additional tests have to be carried out in order to expand the numerical model to a wider range of parameters.
We would like to congratulate Dennis Birkner on completing his doctorate and wish him all the best and every success for the future.