openLAB
Table of contents
Motivation
The aim of the IDA-KI (Infrastructure Data Analysis with Artificial Intelligence) research project is to develop methods for the automated analysis and evaluation of monitoring data. The validation is carried out using real measurement data recorded on a 45 m long research bridge (openLAB). First, the reference condition of the bridge is measured with and without service loads over a period of one year. Subsequently, load tests are carried out in a targeted manner up to the severely damaged state and significant damage to the structure is actively induced. At the same time, redundant sensors will be damaged or manipulated so that a real database with specific signal characteristics for metrological and structural anomalies can be created. This will create an important basis for the development of evaluation methods (also based on machine learning) so that measurement errors in monitoring data can be corrected in the future and differentiated from structural damage.
Research consortium and funding bodies
The research consortium is made up of an equal number of partners from practice and research:
TUD Dresden University of Technology
Institute of Concrete Structures (IMB)
01062 Dresden
Hamburg University of Technology
Institute for Digital and Autonomous Building
Blohmstraße 15
21079 Hamburg
MKP GmbH
Zum Hospitalgraben 2
99425 Weimar
Hentschke Bau GmbH
Zeppelinstrasse 15
02625 Bautzen

Projekttreffen an der Technischen Universität Hamburg
The IDA-KI project (FKZ: 19FS2013) with a total volume of € 3.85 million is funded by the Federal Ministry of Digital and Transport (BMDV) as part of the mFUND research initiative.
openLAB - A research bridge in Lusatia
The research bridge, openLAB, is a prestressed concrete bridge approximately 45 m long and 4.5 m wide, which was built on the premises of Hentschke Bau GmbH in Bautzen. The bridge combines different construction methods in order to provide a wide range of common constructions. Each of the three fields has its own core research focus. The openLAB will be used to test the suitability of the evaluation algorithms to be developed and to facilitate practical transfer.
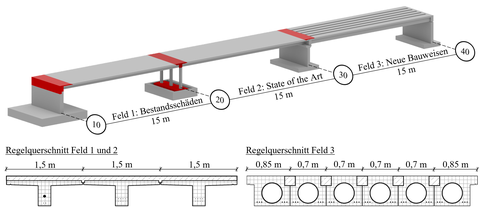
3D-Modell des openLABs inkl. der Regelquerschnitte [1]
Fields 1 and 2 were each constructed from three prefabricated elements (PE) with a slab-beam cross-section and classic in-situ concrete additions. Field 1 illustrates typical damage and damage mechanisms of the early in-situ concrete construction method: Coupling joint problems in PE 1.1; stress corrosion cracking in PE 1.2; areas with reduced shear load-bearing capacity in PE 1.3. In addition, gravel pockets and blowholes are present for diagnostic investigations. Further damage, e.g. to the tendons, is planned for later. Field 2 was implemented according to the current state of the art. A special feature is located in PE 2.1, a so-called Smart Tendon, a cooperation with the mFUND project of the same name. Distributed fiber optic sensors (DFOS) are integrated in the "smart" tendon or in the prestressing strands, which are used to measure the strain state along the tendon and thus detect any damage to the structure at an early stage. In field 3, PE of a rapid construction system was realized without in-situ concrete additions, which are fully loadable immediately after assembly. The load distribution in the transverse direction of the bridge is achieved by casting reinforced joints.
Other structural features (shown in red in the 3D model) are a movable support bearing (axis 20), a monolithic connection between the superstructure and supports (axis 20) and a mineral fiber-reinforced transition (axis 30) [1]. In order to be able to achieve actually relevant loading conditions on the structure up to the ultimate limit state (ULS) with reasonable testing effort, only 25 % of the load model (LM) 1 according to DIN EN 1991-2 was used for the design.
![Abbildung 2: Fertiggestellte Forschungsbrücke im Mai 2024, Blick von Achse 40 in Richtung Achse 10 [1]](https://tu-dresden.de/bu/bauingenieurwesen/imb/ressourcen/bilder/bilder-forschung/ida-ki-openlab/20240514_152429_Fabian-Collin.jpg/@@images/ac947c9a-ccae-4a4b-aeb1-2988aece07c4.jpeg)
Fertiggestellte Forschungsbrücke im Mai 2024, Blick von Achse 40 in Richtung Achse 10 [1]
The drone video shows impressions from the construction phase, shortly before completion. © Hentschke Bau GmbH
Test concept
Reference phase: After completion of the bridge, the reference condition of the structure is initially measured over a period of one year under climatic conditions and "traffic". To simulate the effects of traffic, a rail-guided load vehicle is driven over the bridge several times a month. Further load runs take place on particularly hot and cold days.
After the one-year reference phase, the structure is ready for static and dynamic load tests. In the static tests, the force is applied via hydraulic presses and a load traverse. In addition to the dynamic impact of the load vehicle, the structure can also be excited with a directed exciter or a "shaker" so that the dynamic structural behavior can be investigated in different frequency ranges.
Monitoring system
A comprehensive monitoring system is installed at openLAB to monitor the global structural and local component behavior and thus enable reliable damage detection.
Initially installed monitoring system: During the reference phase, an acceleration sensor is installed in the middle of each PE axis in fields 1 and 2 and an inclination sensor in the area of the moment zero crossings near axis 20. The tests are used to analyze the extent to which different types of damage (e.g. cutting tension wires) affect the modal parameters or the deformation figure. Furthermore, sensors are used to determine the ambient conditions; in this case to determine the air temperature, relative humidity (RH), solar radiation and the amount of precipitation. Strain gauges, inductive displacement transducers and sensors for measuring the component temperature are used to monitor local effects.
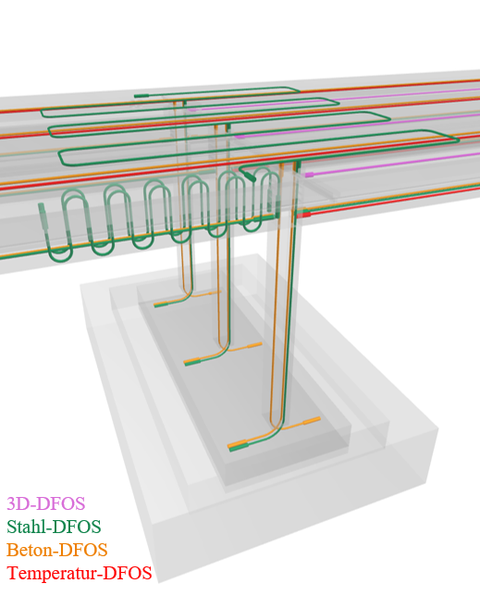
Faseroptische Sensoren bilden ein künstliches Nervensystem [1]
Due to the possibility of performing distributed measurements with high spatial resolution, DFOS offer great potential for structural monitoring [1,2]. Robust DFOS were installed in the precast elements and the in-situ concrete addition before concreting, thus enabling distributed strain and/or temperature measurement with high spatial resolution from "hour zero". With a total length of approx. 1.5 km[MH1] , the DFOS virtually form an artificial nervous system of the bridge.
The exact arrangement of the sensors, including semantic information on the sensor type, can be taken from the as-maintained model. In principle, the configuration of externally arranged sensors can be adapted temporarily - e.g. during a load test - depending on the task.
As-maintained model
All relevant information from the planning, construction and operation of the bridge is provided centrally via an as-maintained model [3]. The range of stored data extends from planning documents and information on the monitoring system to recorded damage and its assessment through to raw sensor data. The as-maintained model thus functions as a virtual image of the real structure, which allows a statement to be made about the current condition of the structure based on the aggregated condition information from monitoring, structural inspections and diagnostic examinations and thus provides a decision-making aid for predictive maintenance.
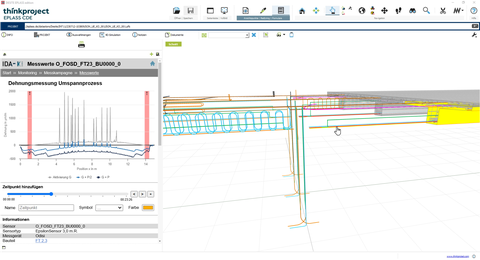
Beispielbild der Benutzeroberfläche
External partners have read-only access via an EPLASS InfoClient. Further information can be found in the following instructions: Instructions for using EPLASS InfoClient
openLab: Anleitung Nutzung EPLASS InfoClient © Hentschke Bau GmbH
A "linked data" approach is used to integrate the high-frequency monitoring data into the associated BIM model. Measurement data and aggregated status information can be visualized on the browser-based platform "iris" developed by the project partner MKP. Alarm messages can be issued automatically by defining limit values.
Andreas Jansen (MKP) will provide the access data for iris on request:
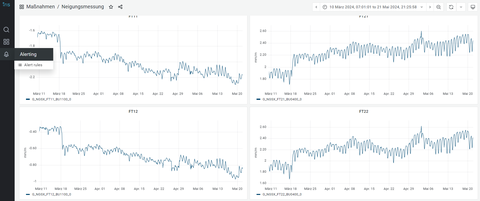
Überwachung der Messdaten in Echtzeit
Evaluation concepts
The automated evaluation and assessment of large volumes of data is the most important prerequisite for a near real-time condition assessment. The free software fosanalysis is being developed in the project for the DFOS data [4,5]. This allows anomalies in the measurement signal to be detected and cracks along the sensor to be monitored. For anomaly detection in the measurement data of "conventional" sensors, such as accelerometers and inclinometers, an approach to fault diagnostics based on analytical redundancy is being developed. Fault diagnostics consists of the subtasks (i) fault detection, (ii) fault isolation, (iii) fault identification and (iv) fault rectification [6,7]. It is planned to expand the monitoring task-related with additional measurement technology from external project participants in order to be able to evaluate the potential of different sensor types with regard to anomaly detection. All monitoring data is to be integrated into the evaluation processes.
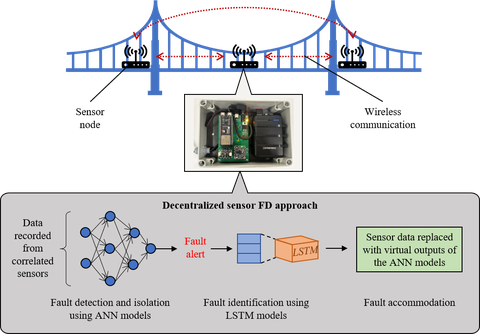
Schema der dezentralisierten Fehlerdiagnose
Data access and usage agreements
The following measurement data will be made available via the research data repository OpARA (Open Access Repository and Archive):
- Measurements in the reference phase
- Measurements during selected load tests (e.g. also for system identification)
The link to the data is provided via this website. Data use is subject to the following conditions:
- The data is used for non-commercial research purposes.
- In the case of publications, the origin of the data including DOI must be stated. Example of acknowledgements: "The measurement data were obtained at openLAB and provided by the TUD Dresden University of Technology as part of the IDA-KI research project (FKZ 19FS2013A-D)."
- The IDA-KI research consortium must be informed about publications using the data provided at the latest at the time of publication.
- If own sensors are installed at openLAB, the measurement data must be made available to the consortium and the public (if necessary after a short latency period). The type and scope of data provision will be detailed in consultation with the consortium management.
Opportunities for cooperation
The large-scale demonstrator will also be made available to external research groups who wish to test and validate sensor technology and monitoring techniques. Cooperation with national and international industrial partners and research institutions at openLAB is desired by both mFUND and the project partners. Interested parties are invited to contact the consortium management or the project partners involved.
There is active cooperation with the monitoring provider Statotest, for example, which has supplemented the existing monitoring system with its own measurement technology. A total of eight measuring boxes are used to dynamically record accelerations and inclinations. The data supplements the measurements from the initial measurement system and offers the opportunity to compare different sensor types and measurement principles with regard to their potential for anomaly detection. Statotest uses the measurement data from the damaging load tests to check and further develop existing evaluation procedures.
The following calendar provides an overview of the dates of the load tests and special measurements on the bridge: https: //tud.link/a8yy3n
Contact us
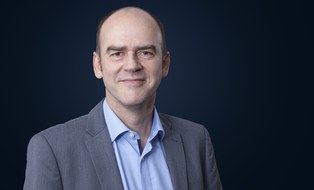
Director and Professor of Concrete Structures
NameMr Univ.-Prof. Dr.-Ing. Steffen Marx
Send encrypted email via the SecureMail portal (for TUD external users only).
Technische Universität Dresden - Institute of concrete structures
Technische Universität Dresden - Institute of concrete structures
Visiting address:
BEY Beyer-Bau, Floor 0, Room E 08 George-Bähr-Str. 1
01069 Dresden
Postal address:
TUD Dresden University of Technology Institut für Massivbau
01062 Dresden
Parcel address:
TUD Dresden University of Technology Institut für Massivbau Helmholtzstr. 10
01069 Dresden
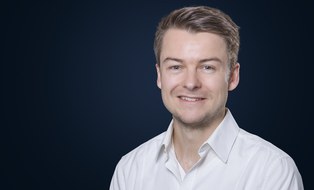
Research Associate
NameMr Max Herbers M.Sc.
Send encrypted email via the SecureMail portal (for TUD external users only).
Technische Universität Dresden - Institute of concrete structures
Technische Universität Dresden - Institute of concrete structures
Visiting address:
BEY Beyer-Bau, Floor -1, Room S 48 George-Bähr-Str. 1
01069 Dresden
Publications
[1] | Herbers, M.; Bartels, J.-H.; Richter, B.; Collin, F.; Ulbrich, L.; Al-Zuriqat, T.; Chillón Geck, C.; Naraniecki, H.; Hahn, O.; Jesse, F.; Smarsly, K.; Marx, S.: openLAB - A research bridge for the development of a digital bridge twin. Beton- und Stahlbetonbau 119 (2024) 3, 167-180 - https://doi.org/10.1002/best.202300094 |
[2] | Herbers, M.; Richter, B.; Gebauer, D.; Classen, M.; Marx, S.: Crack Monitoring on Concrete Structures - Comparison of Various Distributed Fiber Optic Sensors with Digital Image Correlation Method. Structural Concrete 24 (2023) 5, 6123-6140 - https://doi.org/10.1002/suco.202300062 |
[3] | Collin, F.; Ulbrich, L.; Jesse, F.: Konzept eines Digitalen Zwillings für Brückenbauwerke in der Betriebsphase. Structural Engineering 101 (2024) 3, 199-205 - https://doi.org/10.1002/bate.202400003 |
[4] | Richter, B.; Herbers, M.; Marx, S.: Crack Monitoring on Concrete Structures with Distributed Fiber Optic Sensors - Toward Automated Data Evaluation and Assessment. Structural Concrete 25 (2024) 2, 1465-1480 - https://doi.org/10.1002/suco.202300100 |
[5] | fosanalyis - A framework to evaluate distributed fiber optic sensordata [Software]. https://github.com/TUD-IMB/fosanalysis. |
[6] | Al-Zuriqat, T.; Chillón Geck, C.; Dragos, K.; Smarsly, K.: Adaptive Fault Diagnosis for Simultaneous Sensor Faults in Structural Health Monitoring Systems. Infrastructures 8 (2023) 3, 39 - https://doi.org/10.3390/infrastructures8030039 |
[7] | Al-Zuriqat, T.; Peralta, P.; Chillón Geck, C.; Dragos, K.; Smarsly, K.: Implementation and validation of a low-cost IoT-enabled shake table system. In: Farhangdoust, S.; Guemes, A.; Chang, F.-K. [Eds:] Proc. of Int. Workshop on Structural Health Monitoring (IWSHM), Stanford: DEStech Publ., Inc, 2023, 1063-1070 |