Nov 08, 2019
Hochleistungs-Faserverbundkunststoff aus dem 3D-Drucker
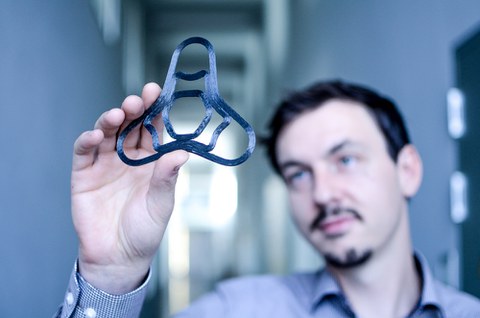
ILK-Wissenschaftler Andreas Borowski prüft ein generativ gefertigtes endlosfaserverstärktes CF-PEEK-Bauteil
Wissenschaftler der TU Dresden realisieren endlosfaserverstärkten Verbundkunststoff aus Kohlenstofffasern und PEEK (Polyetheretherketon)
Wissenschaftler des Instituts für Leichtbau und Kunststofftechnik der TU Dresden haben eine modulare generative Fertigungsanlage für die Verarbeitung von Verstärkungsfasern wie Kohlenstoff- und Glasfasern sowie von Hochleistungskunststoffen wie beispielsweise PA6 und PEEK entwickelt. Die neuartige Anlage kommt im Innovationslabor für generative Fertigung des ILK zum Einsatz und arbeitet ohne Bauraumbeheizung und mit einem modularen Dualextrusion-Systemdruckkopf. Durch das werkzeuglose Fertigungskonzept und der effizienten, materialsparenden Schichtbauweise erweitert die Anlage somit den Multimaterial-Baukasten des Instituts um ein weiteres zukunftsweisendes Fertigungsverfahren.
Fused-Layer-Modeling-Verfahren mit besonders hohem Faservolumengehalt
Durch eine nahezu grenzenlose Formfreiheit der additiven Fertigung, kombiniert mit den Vorteilen aus der Welt der Faserkunststoffverbunde, birgt die daraus resultierende generative Fertigung ein hohes Potential für den Multi-Material-Leichtbau und vor allem für die Gestaltoptimierung von Strukturbauteilen. Die Basis der neuartigen Fertigungsanlage bildet das FLM-Verfahren (Fused-Layer-Modeling), mit dem ein Objekt schichtweise aufgebaut und innerhalb der einzelnen Bereiche verschiedene Materialien kombiniert werden können. Da die Eigenschaften unverstärkter Polymere gerade bei größeren Bauteilen nicht ausreichen, ist die Verstärkung durch Kurz-, Lang- und Endlosfasern besonders interessant. So ist der Systemdruckkopf in der Lage, Hochleistungsmaterialien effizient zu verarbeiten und erreicht hierbei einen besonders hohen Faservolumengehalt. In Kombination mit einer sehr geringen Bauteilporosität können so extrem hohe Steifigkeiten bei einer gleichzeitig hohen Festigkeit in der generativen Faserverbundstruktur erreicht werden.
Nach bereits abgeschlossener erfolgreicher technologischer Validierung des Gesamtsystems erarbeiten die Forscher des ILK aktuell relevante Verbundkennwerte, sodass in einem weiteren Schritt mithilfe numerischer Simulationsverfahren komplexe generativ gefertigte Strukturbauteile einsatzgerecht ausgelegt werden können. Durch die lokalvariable Positionierung der Endlosfasern können lastpfadgerechte Substrukturen innerhalb der einzelnen Bauteilschichten abgelegt werden. Der Leichtbaugrad eines Bauteils steigt so wesentlich. Die Ein- und Überleitung von äußeren Belastungen auf die Struktur induziert innere Bauteilbeanspruchungen, die möglichst gerecht auf angrenzende Verbundpartner zu verteilen sind. Je besser die Verteilung einer Belastung auf ein Bauteil gelingt, desto langlebiger und hochwertiger wird die Gesamtstruktur. Aktuelle Forschungsaktivitäten befassen sich zudem mit der roboterbasierten Pfadablage auf mehrfach gekrümmten Grundstrukturen, um diese hochflexibel und ohne zusätzliche Werkzeuge funktionalisieren zu können.
Innovationslabor für generative Fertigung
Das Innovationslabor für generative Fertigung des Instituts für Leichtbau- und Kunststofftechnik wächst stetig, ebenso wie die Bandbreite der für die Verfahren geeigneten Materialien. So können über Hochleistungskunststoffe wie PEEK, PEI (Polyetherimid) und PA6 auch Biopolymere auf Basis von Lignin verarbeitet werden, sodass ein sehr vielfältiges Materialspektrum abgedeckt ist. Entsprechend der Anwendung und den damit zusammenhängenden Beanspruchungen kann somit auf Materialien bzw. Materialkombinationen zurückgegriffen werden, die in vollem Umfang den jeweiligen Anforderungen gerecht werden.
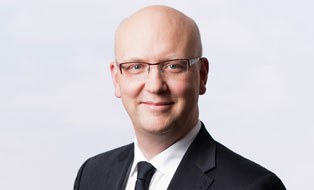
Chair of Function-integrative Lightweight Engineering
NameProf. Dr.-Ing. Niels Modler
Send encrypted email via the SecureMail portal (for TUD external users only).
Institute of Lightweight Engineering and Polymer Technology
Visitors Address:
DÜR, Floor 0, Room 69 Holbeinstr. 3
01307 Dresden
Deutschland