11.10.2019
K 2019: ILK-Leichtbauer mobilisieren die Spritzgießtechnik
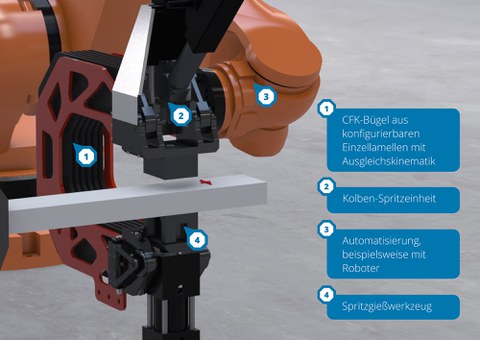
Modularer Leichtbau-C-Bügel mit Spritzaggregat für die mobile Funktionalisierung
Durch innovative Bauweisen und den intelligenten Einsatz von Faserverbundwerkstoffen ist es Wissenschaftlern des Instituts für Leichtbau und Kunststofftechnik (ILK) der TU Dresden gelungen, die Spritzgießtechnologie derart weiterzuentwickeln, dass diese erstmals mobil einsetzbar ist. Der verarbeitenden Industrie kann eine neuartige Anlagentechnik bereitgestellt werden, bei der nicht mehr das Produkt zur Anlage, sondern die Maschine zum Produkt geführt werden kann. Dadurch ergeben sich völlig neue Möglichkeiten bei der Gestaltung von Fertigungsprozessen sowie der Herstellung komplexer Hybridstrukturen.
Mobiles Spritzgießsystem
In den letzten Jahren haben vor allem hybride Bauteilstrukturen aus flächigen Metall- oder Faserkunststoffverbund-Halbzeugen an Bedeutung gewonnen, die mit zusätzlichen Funktionselementen aus Kunststoff versehen werden. Meistens werden Funktionselemente wie strukturelle Versteifungen oder Füge- bzw. Dichtelemente mit Hilfe der Spritzgießtechnologie an die Komponenten geformt. Die hierfür benötigten Werkzeuge und die dazugehörigen Spritzgießanlagen sind jedoch vor allem bei komplexen bzw. großen Strukturen mit hohen Investitionskosten verbunden und können daher nur bei Großserienanwendung wirtschaftlich eingesetzt werden. Dies steht dem derzeitigen Trend hin zu geringeren Stückzahlen und zunehmender Variantenvielfalt entgegen. Die bekannten Verfahren, deren Fokus auf Massenfertigung von Gleichteilen liegt, sind dabei häufig unrentabel.
Aus dieser Problemstellung heraus haben die Leichtbauexperten vom ILK eine einzigartige Anlagentechnik entwickelt, die es erlaubt, die Variabilität bestehender Fertigungen signifikant zu erhöhen, während die Anlageninvestition nur ein Bruchteil bisheriger Lösungen beträgt. Die ROBIN-Anlagentechnik besteht dazu aus einem Automatisierungssystem (z. B. Knickarmroboter, Linearantrieb) und einem als C-Bügel ausgeführten mobilen Spritzgießsystem. Der lasttragende Bestandteil des C-Bügels ist dabei in Faserverbundbauweise ausgeführt, so dass eine hohe Struktursteifigkeit bei ausreichend geringer Gesamtmasse (ca. 150 kg) realisiert werden kann (Bild 1).
Erstmalig mobiles Spritzgießen möglich
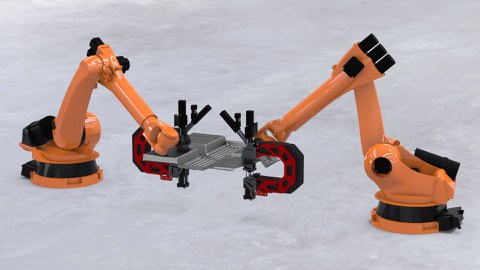
Fertigungskomplex zur lokalen Funktionalisierung einer großflächigen Bauteilstruktur mit zwei gekoppelten ROBIN-Systemen
Damit wird das Spritzgießen erstmalig mobil, kann variabel mit üblichen Automatisierungssystemen kombiniert und direkt in kontinuierliche Fertigungs- oder Montagestrecken integriert werden. Durch die Bauform des C-Bügels und die kompakten Werkzeugabmessungen können großflächige Komponenten ideal im Inneren des Bügels aufgenommen werden, so dass die Funktionalisierung nahezu an beliebiger Position des Bauteils erfolgen kann. So können zum Beispiel Verbindungselemente, Gewinde, Strukturversteifungen, Abstandshalter, Kantenschutz, oder ähnliches realisiert werden. Zukünftig können Kunden mit einem oder mehreren gekoppelten ROBIN-Systemen (Bild 2) auf große und teure Spritzgießanlagen mit einer Investition von mehreren Mio. Euro verzichten, um großflächige Spritzgieß-Hybridkomponenten herzustellen und so insbesondere kleine und mittlere Serien wirtschaftlich umzusetzen.
Eine Funktionalisierung der Bauteile mit der ROBIN-Technologie ist jedoch nicht nur durch die Kombination mit dem Spritzgießen möglich. Das Prinzip des robotergeführten Leichtbau-C-Bügels ist einfach mit anderen Aggregaten wie PUR-Injektionssystemen sowie mechanischer oder thermischer Fügetechnik zu kombinieren.
Von der Leistungsfähigkeit der ROBIN-Technologie können sich Interessenten selbst überzeugen. Zusammen mit den Partnern AUMO GmbH, CHRISTMANN Kunststofftechnik GmbH und der FEP Fahrzeugelektrik Pirna GmbH erfolgt die Weltpremiere auf der K-Messe vom 16.-23.10.2019 in Düsseldorf. In Live-Vorführungen können Besucher die Position der mobilen Spritzgießeinheit selbst beeinflussen und Hybridstrukturen herstellen. Sie finden uns auf dem Messestand 07SC08 vom Science Campus in Halle 7.
FOREL-Mockup zeigt Ergebnisse aus sieben Forschungsprojekten
Als weiteres Highlight stellen die Forscher mit dem FOREL-Mockup die Ergebnisse aus sieben Forschungsprojekten mit über 100 beteiligten Partnern der vom BMBF geförderten offenen und unabhängigen Forschungsplattform zur Entwicklung von Hightech-Leichtbausystemlösungen in Multi-Material-Design für die Mobilität der Zukunft (FOREL) anhand verschiedener Fahrzeugkomponenten vor. Binnen sechs Jahren haben namhafte Partner aus Wirtschaft und Wissenschaft die Forschung entlang der gesamten Wertschöpfungskette signifikant vorangetrieben.
In den vergangenen Jahren wurden in den verschiedenen Teilprojekten Technologien entwickelt und anhand verschiedener Fahrzeugkomponenten aufgezeigt, die nun in einem Demonstrator zusammengeführt wurden . Das Mockup beinhaltet eine A-Säulen-Tragstruktur in 3D-Hybrid-Technologie, eine Partikelschaum-Fahrzeugtür, ein Rückwandoberteil einer Fahrzeugkarosserie, die zu 80 % aus rezyklierten kohlenstofffaserverstärkten Kunststoffen besteht, eine innovative Unterbodenstruktur mit neuartigen, hybriden Sandwichmaterialien, eine Seitenspiegelhalterung in Kunststoff-Magnesium Hybridbauweise, eine Tragstruktur einer Fahrzeugtür, die unter Verwendung neuartiger 3D-Textilien hergestellt wurde sowie eine hybride Rückenlehne eines Fahrzeugsitzes. Das Mockup wird auf dem SCIENCE CAMPUS CENTER (SC09) präsentiert.
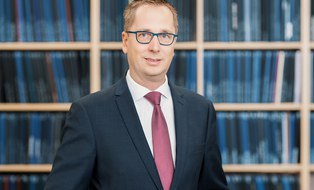
Professur für Systemleichtbau und Mischbauweisen
NameProf. Dr.-Ing. habil. Maik Gude
Eine verschlüsselte E-Mail über das SecureMail-Portal versenden (nur für TUD-externe Personen).
Institut für Leichtbau und Kunststofftechnik
Besucheradresse:
DÜR, Etage 0, Raum 71 Holbeinstr. 3
01307 Dresden
Deutschland
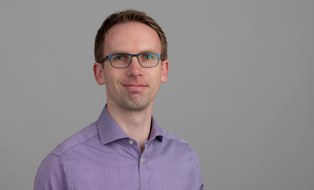
Dr.-Ing. Michael Krahl
Stellvertretender Leiter Thermoplastverfahren
Eine verschlüsselte E-Mail über das SecureMail-Portal versenden (nur für TUD-externe Personen).
Institut für Leichtbau und Kunststofftechnik
Besucheradresse:
DÜR, Etage 1, Raum 175 Holbeinstr. 3
01307 Dresden
Deutschland