Nov 30, 2017
Kosteneffizienter Hybridleichtbau durch eine intelligent vernetzte Prozesskette
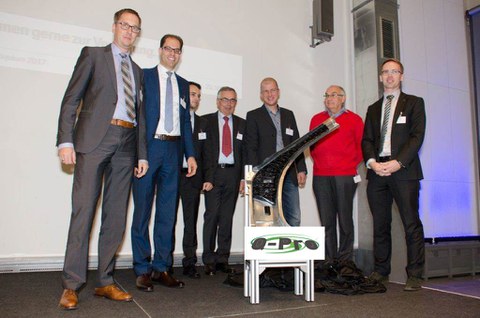
Das Q-Pro-Team präsentiert den A-Säulen-Demonstrator.
Vor allem für die Elektromobilität sind innovative Leichtbaulösungen in Multi-Material-Design sowie qualitätsgesicherte Prozessketten von hoher Bedeutung. Im BMBF-Projekt Q-Pro hat ein interdisziplinäres Team aus Industrie und Wissenschaft unter Federführung der Dr. Ing. h.c. F. Porsche AG und des Instituts für Leichtbau und Kunststofftechnik (ILK) der TU Dresden eine neuartige Leichtbau-A-Säule in 3D-Hybrid-Bauweise entwickelt und nun erstmals der Öffentlichkeit präsentiert. Gefertigt wird diese hochkomplexe Bauteilstruktur in einem vollständig automatisierten und qualitätsüberwachten Fertigungsprozess.
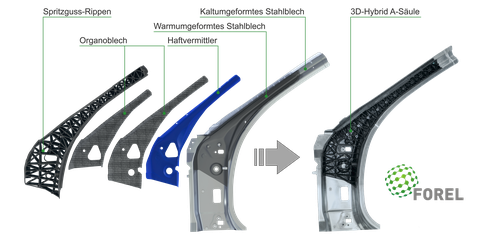
Aufbau der intrinsisch gefügten Leichtbau-A-Säule in 3D-Hybrid-Bauweise
Der Einsatz großserienfähiger Leichtbaulösungen stellt eine wesentliche Voraussetzung zum Erreichen der ambitionierten Elektromobilitätsziele dar. Mit der sogenannten 3D-Hybrid-Technologie – eine Verbindung aus hochfestem Stahl, endlosfaserverstärktem Thermoplast und faserverstärkter Thermoplast-Rippenstruktur – kann ein entscheidender Entwicklungsschritt zur Senkung des Fahrzeuggewichts und somit zur Reichweitenerhöhung beigetragen werden. Bislang fehlten für die großserienfähige Fertigung solcher komplexer Hybridstrukturen jedoch geeignete Fertigungsprozesse mit hohem Automatisierungsgrad, die eine ausreichend hohe Bauteilqualität sicherstellen.
Genau aus dieser Fragestellung ergab sich schließlich die Motivation für das Verbundvorhaben Q-Pro, was unter dem Dach der Forschungsplattform FOREL geführt wird. Seit über zwei Jahren forscht das Projektteam unter Leitung von Prof. Dr.-Ing. habil. Maik Gude an neuen konstruktiven sowie fertigungstechnischen Lösungen für Faserverbund-Metall-Mischbauweisen. Gegenüber konventionellen Fertigungsverfahren werden die Einzelkomponenten bei der 3D-Hybrid-Technologie bereits im Ur- bzw. Umformprozess der Einzelkomponenten miteinander gefügt. Für die Sicherstellung einer ausreichenden Verbindungsfestigkeit kommen spezielle Haftvermittler bzw. Klebstoffe zum Einsatz. Darüber hinaus werden Laserstrukturierungen auf der Metalloberfläche untersucht, die eine mikroformschlüssige Verbindung mit dem Kunststoff während des Fertigungsprozesses ermöglichen.
Das Potential dieser Technologie kann an dem Projektdemonstrator einer Leichtbau-A-Säule für ein Cabrio (Bild 1) eindrucksvoll aufgezeigt werden. Gegenüber konventionellen A-Säulen kann durch die neue 3D-Hybrid-Bauweise die Komponentenanzahl der Baugruppe reduziert werden. Das Gewicht der Karosserie kann mit den neuartigen Hybrid-A-Säulen um mehr als 5 kg reduziert werden. Die Versuche haben darüber hinaus gezeigt, dass die Performance gegenüber der monolithischen Metallbauweise zusätzlich um 25 Prozent gesteigert werden konnte. Der Einsatz der 3D-Hybrid-Technologie in weiteren Karosseriebaugruppen bietet, insbesondere bei Elektrofahrzeugen mit höherer Crashmasse und zusätzlichen Anforderungen bezüglich Batterieschutz, ein hohes Potential, das Gewicht der Karosserie zu reduzieren und dadurch die Reichweite zu erhöhen.
Für die Fertigung der hybriden A-Säule hatten die ILK-Forscher um Dr.-Ing. Michael Krahl im institutseigenen Prozess-Entwicklungszentrum einen vollautomatisierten Fertigungsprozess aufgebaut. Eine Besonderheit ist hier das integrierte Qualitätsüberwachungssystem. So werden beispielsweise über verschiedene Kameras die Positionen der Halbzeuge im Prozess überwacht. Pyrometer erfassen Temperaturen entlang der gesamten Prozesskette. Darüber hinaus werden eine Vielzahl von Prozessparametern aus den unterschiedlichen Maschinen (Presse, Infrarotheizfeld, Spritzgießmaschine) ausgelesen und in einer zentralen Datenbank erfasst. Unter Einsatz neuer statistischer Analysetools werden die Prozessdaten analysiert und die Parameter hinsichtlich einer reproduzierbaren Bauteilqualität angepasst.
Das Projekt Q-Pro wird mit Mitteln des Bundesministeriums für Bildung und Forschung (BMBF) im Rahmenkonzept „Innovationen für die Produktion, Dienstleistung und Arbeit von morgen“ (Förderkennzeichen 02P14Z040 – 02P14Z049) und mit Mitteln aus den Energie- und Klimafonds gefördert und vom Projektträger Karlsruhe (PTKA) betreut.
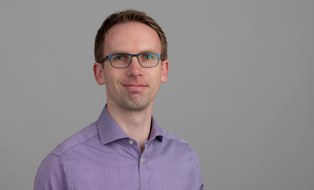
Dr.-Ing. Michael Krahl
Deputy Head of Thermoplastic processing
Send encrypted email via the SecureMail portal (for TUD external users only).
Institute of Lightweight Engineering and Polymer Technology
Visitors Address:
DÜR, Floor 1, Room 175 Holbeinstr. 3
01307 Dresden
Deutschland