07.12.2021
Hybridstrukturen im Minutentakt
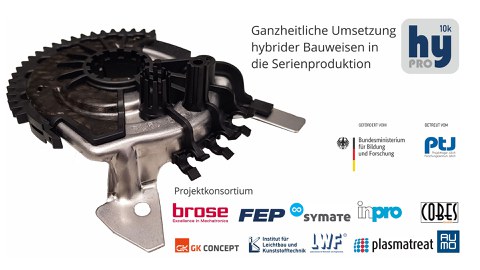
Generisches hypro-FKM-Hybridbauteil
Automatisierte Prozesskette zur Herstellung von Faserverbund-Kunststoff-Metall-Hybridbauteilen am ILK in Betrieb genommen – wichtiger Meilenstein im Projekt hypro erreicht
Im Projekt „hypro – Ganzheitliche Umsetzung hybrider Bauweisen in die Serienproduktion“ wurde ein wichtiger Meilensteil auf dem Weg zur serientauglichen und wettbewerbsfähigen Produktion hybrider Bauteile erreicht. Im Technikum des Instituts für Leichtbau und Kunststofftechnik (ILK) der TU Dresden wurde eine vollautomatisierte Anlage aufgebaut und in Betrieb genommen, die die Herstellung von Faserverbund-Kunststoff-Metall-Hybridbauteilen (FKM-Hybridbauteilen) im Minutentakt ermöglicht.
FKM-Hybridbauteile bieten mit ihrer Eignung für die Umsetzung hochbelastbarer und geometrisch komplexer Leichtbaustrukturen ein erhebliches Leichtbaupotenzial. Durch den Einsatz thermoplastischer Kunststoffe können sie Zykluszeiten von unter einer Minute erreichen und bieten somit eine hohe wirtschaftliche Attraktivität. Um jedoch eine hochbelastbare Verbindung der Einzelkomponenten sicherzustellen, erfordert die Kombination der unterschiedlichen Werkstoffe: Metalle, Thermoplast-Faserkunststoffverbund (FKV) und Kunststoffe, einen hohen Vorbehandlungsaufwand – insbesondere die des metallischen Einlegers. Daher ist die Produktionstechnologie für diese Hybridstrukturen momentan nicht wettbewerbsfähig und wird derzeit noch nicht im industriellen Maßstab umgesetzt.
Das BMBF-Projekt hypro hat zum Ziel, diese Lücke zu schließen und ein tiefgreifendes Verständnis für thermoplastische FKM-Hybridstrukturen aufzubauen. Zu diesem Zweck hat das Projektkonsortium unter Koordination der Brose Fahrzeugteile SE & Co. KG, Bamberg eine durchgängig automatisierte Prozesskette zur Herstellung von FKM-Hybridbauteilen konzipiert und eine Anlage zu ihrer Umsetzung im Technikum des ILK aufgebaut und in Betrieb genommen.
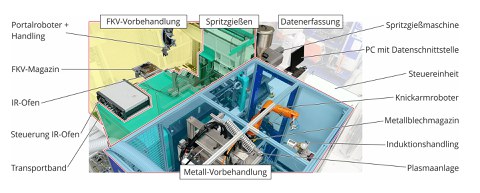
Automatisierte hypro-Fertigungsanlage
Der aufgebauten Anlage liegt ein Spritzguss-Kombinationsprozess zu Grunde, bei dem tiefgezogene Metalleinleger mit vorkonfektionierten FKV-Patches kombiniert und mit faserverstärktem Kunststoff umspritzt werden. Um eine hoch belastbare Verbindung zwischen den Kunststoffkomponenten und dem Metalleinleger zu gewährleisten, wird dieser mittels Plasmatechnologie inline gereinigt und beschichtet. Zur Aktivierung der haftvermittelnden Plasmabeschichtung wird der Metalleinleger durch ein Induktionshandling innerhalb weniger Sekunden erwärmt und in das Spritzgießwerkzeug transferiert. Dort wird er anschließend mit dem FKV-Patch verpresst und umspritzt. Die Koordination der einzelnen Prozessschritte erfolgt über eine zentrale Steuereinheit. Diese überwacht den aktuellen Fortschritt eines jeden Einzelprozesses, regelt die Prozessparameter und reagiert auf Prozessschwankungen, etwa bei veränderten Heizraten. So wird sichergestellt, dass sowohl das FKV-Patch als auch der Metalleinleger in definierten Zuständen gefügt werden. Gleichzeitig erfasst die Steuereinheit durchgängig alle relevanten Prozess-, Qualitäts- und Umgebungsdaten, welche anschließend bauteilspezifisch in einer Datenbank IoT-Plattform „Detact“ abgelegt werden. Dieser Datenstand ermöglicht nun umfangreiche Prozessstudien im Stückzahlbereich bis zu 10.000 und die Herausarbeitung relevanter Stellgrößen zur wirtschaftlichen Herstellung hochbelastbarer Hybridbauteile. Somit rückt das Ziel des Projektkonsortiums in greifbare Nähe: die Überführung der thermoplastischen FKM-Hybridbauweise in Großserienprozesse mit Taktzeiten unter einer Minute.
Das Verbundprojekt hypro wird durch das Bundesministerium für Bildung und Forschung (BMBF) aufgrund eines Beschlusses des Deutschen Bundestages unter der Betreuung des Projektträgers Jülich PTJ gefördert. (FKZ 03XP0284A-J)
Projektleitung für ILK:
Prof. Dr. habil. Maik Gude, Professur für Leichtbaudesign und Strukturbewertung.
Ansprechpartner:
Dr.-Ing. Robert Kupfer, Fachgruppe Neutralleichtbau
E-Mail: , Tel.: +49 (0)351 463-38749