SFB/TRR 285–A03
Calculation and evaluation of process-induced material structure phenomena in FKV-metal connections
Fiber-reinforced thermoplastics (FRTP) enable the production of lightweight structures within short cycle times. By leveraging the specific material properties of FRTP, connections between dissimilar joining partners can be realized with innovative assembly interfaces. Joining processes are accompanied by local changes in the material structure.
Within the second funding period, a modeling strategy for direct pin pressing and self-riveting in FRTP is being developed. In addition to process simulation at the meso scale, the work also focuses on analyzing load-bearing behavior. Currently, meso-level modeling strategies for direct pin pressing and self-riveting are under development.
While a multi-filament approach was used during the first funding period, the textile now being employed is represented on meso scale more realistically and combined with extended Lagrange-Euler (ALE) methods. For a numerical representation of the entire process, shear and compaction processes must be taken into account. For this purpose, experimental test environments have already been developed, and numerical studies have been conducted on both micro-scale models (Fig. 1) and cohesive zone and contact formulations at the meso-scale. In the next step, the more suitable cohesive zone approach will be applied to the textile. Building on that, data-based approaches to material modeling will be examined, enabling a subsequent analysis of load-bearing capacity.
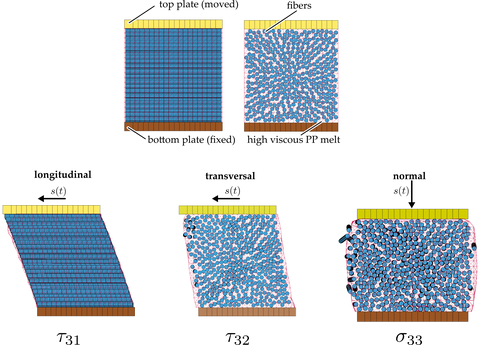
Numerical investigations of the shear and compaction behaviour of FRTP above melting temperature.
01.07.2023 – 30.06.2027
- Laboratory for Material and Joining Technology (LWF) at the University of Paderborn (UPB)
- Institute of Polymer Technology (IKT) at the Friedrich-Alexander-University Erlangen-Nuremberg
- Department of Forming and Machining Technology (LUF) at the University of Paderborn (UPB)
- Automotive Lightweight Design (LiA) at the Faculty of Mechanical Engineering at the University of Paderborn (UPB)
- Institute of Manufacturing Technology (LFT) at the Friedrich-Alexander Universität Erlangen-Nürnberg (FAU)
- Institute of Solid Mechanics (IFKM) at the TU Dresden
- Institute of Manufacturing (IF) at the TU Dresden
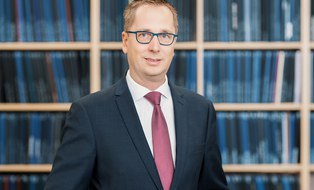
Chair of Lightweight Systems Engineering and MultiMaterial Design
NameProf. Dr.-Ing. habil. Maik Gude
Send encrypted email via the SecureMail portal (for TUD external users only).
Institute of Lightweight Engineering and Polymer Technology
Visitors Address:
DÜR, Floor 0, Room 71 Holbeinstr. 3
01307 Dresden
Deutschland
- Dr. Andreas Hornig (Calculation Methods and Simulation)
Publications Andreas Hornig | TU Dresden
- Benjamin Gröger (Calculation Methods and Simulation)
Publikationen Benjamin Gröger | TU Dresden
- Johannes Gerritzen (Calculation Methods and Simulation)
Publications Johannes Gerritzen | TU Dresden