SandMesh³
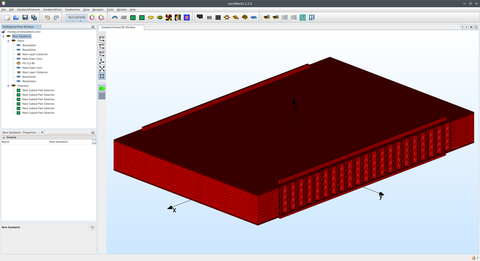
Screenshot of the SandMesh³ program for the creation of detailed FE models of sandwich structures
Short description
SandMesh³ is developed at the Chair of Aircraft Engineering of the TUD Dresden University of Technology as an easy-to-use FE model generator for sandwich structures.
For a reliable simulation of the mechanical behavior of a sandwich under impact load as well as a numerical analysis of the failure of damaged and undamaged specimens, very detailed FE models have to be provided. This is especially true for the extremely complex topology of open-core materials such as honeycombs or folded cores. In addition, the boundary conditions of the test configuration to be simulated must be taken into account in an appropriate manner. The generation of such detailed FE models of sandwich structures is extremely time-consuming. SandMesh³ solves this task efficiently.
Face sheets
SandMesh³ provides different models for sandwich face sheets to represent the individual characteristics of each simulation in an appropriate manner.
Stochastically distributed material data
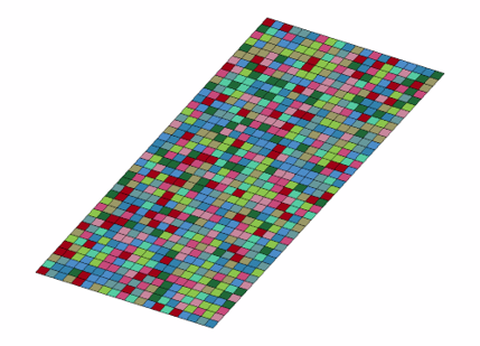
Figure of a FE fase sheet model with stochastically distributed material data, created using SandMesh³
Virtually no industrially manufactured component consists of a completely homogeneous material. Microcracks, voids and other defects cause locally varying stiffnesses and strengths. By stochastically subdividing the surface layer into parts with varying material data, this can be taken into account in the FE model.
Delamination
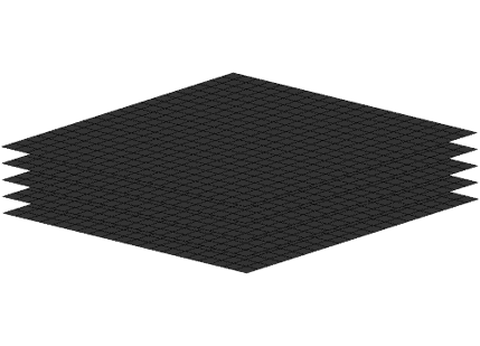
Face sheet model with separate shell layers, created using SandMesh³
For simulating delaminations, corresponding failure criteria must be integrated into the FE model. For example, all layers of a laminate can be represented by separate shell layers. The interconnection is then realized either by contacts or by cohesive elements that also have to be discretized.
Impact damages
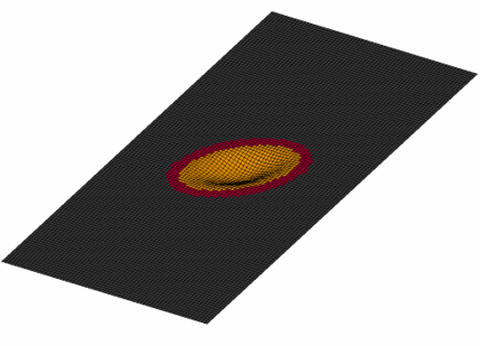
Model with impact (yellow) and damage environment (red), created using SandMesh³
For numerically determining the residual strength of damaged structures, the relevant damage must be represented into the FE model. Impact damage in the surface layer can be taken into account in the form of an arbitrarily aligned, elliptical indentation. Additionally, reduced material parameters are assigned to the damage environment.
Ultra sound scan based modeling
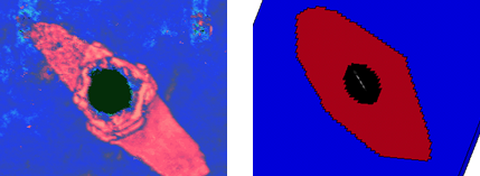
Ultrasonic scan (left) and derived FE model (right), created using SandMesh³
Results of ultrasonic scans can be used for a realistic modeling of impact damages. For this purpose, the ultrasonic images are automatically processed. Thereby, the shape and size of the damage are determined and integrated into the FE model by equivalent part assignments or suitable contact formulations.
Core structures
Currently, three different types of the most common sandwich core structures can be modeled:
- folded cores,
- honeycomb cores,
- foam cores.
The modular design of SandMesh³ allows the integration of new structure types whenever required. As for the surface layers, additionally a large number of special features can be taken into account when modeling the core structures.
Folded cores
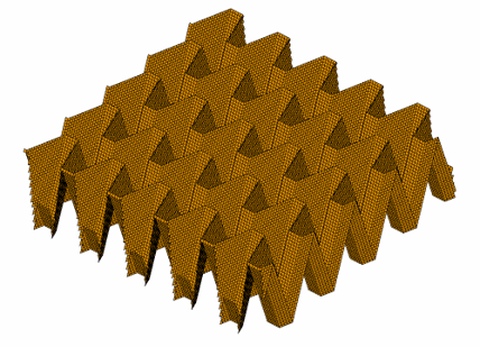
FE model of a folded core, created using SandMesh³
Folded cores are manufactured from resin-impregnated paper using a special folding technique based on non-trivial geometric methods. SandMesh³ determines the geometry for arbitrary folded core configurations, based on angles, distances and curvature, in order to represent the real manufactured folded core in the FE model.
Honeycombs
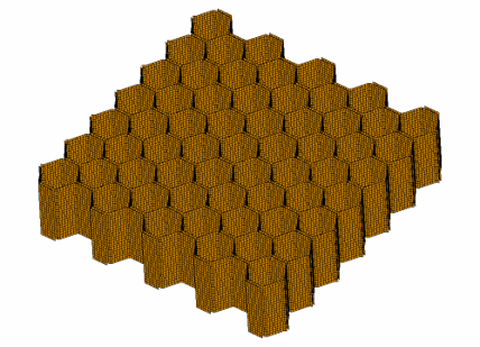
FE model of a honeycomb core created, using SandMesh³
Honeycombs can contain a number of anomalies due to their manufacturing process. Some of them can significantly affect the mechanical behavior of the cores. SandMesh³ can take irregularities, such as over- and under-expansion, curvatures in the wall cross-section, as well as resin accumulation in the corners, into account when generating the FE model.
Additional options
SandMesh³ offers a number of additional options for the creation of FE models of sandwich structures:
- Imperfections of the face layers and honeycomb walls, that can be modeled by random displacements of the nodes or by multiple sine half-waves.
- Curvature of the entire model.
- Creation of layered sandwich models with multiple core structures.
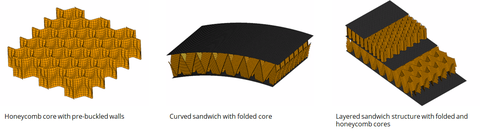
Examples of different FE models for sandwich structures using the options available in SandMesh³
Appplication examples
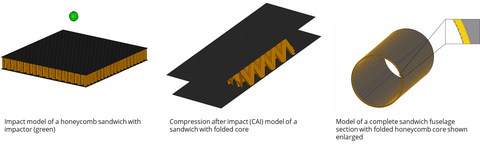
Application examples of the SandMesh³ program for detailed modeling of sandwich structures
Contact
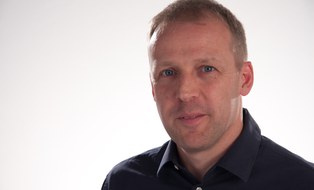
Team leader
NameMr Dr.-Ing. Falk Hähnel
Send encrypted email via the SecureMail portal (for TUD external users only).
Chair of Aircraft Engineering
Chair of Aircraft Engineering
Visiting address:
MAR32, 3rd floor, Room 314 Marschner Straße 32
01307 Dresden