APRW – Untersuchung von Berechnungsmodellen und des Deformationsverhaltens für das inkrementelle Umformverhalten Axialprofilrohrwalzen
Laufzeit: | 07/2008 – 03/2010 |
Finanzierung: | Deutsche Forschungsgemeinschaft (DFG) |
Bearbeiter: | Dr.-Ing. André Hardtmann |
Kooperation: |
|
Zielstellung
Ziel des Forschungsvorhabens ist die Weiterwicklung, Erprobung und Validierung der in der ersten Antragsphase am Institut für Festkörpermechanik (IFKM) entwickelten Berechnungsverfahren für das Umformverfahren Axialprofilrohrwalzen (APRW). Voraussetzung bilden Auswahl, Bewertung und Validierung geeigneter FE-Modelle unter dem Aspekt der speziellen Anforderungen des APRWs. Dazu sind die bisherigen Modelle hinsichtlich ihre Realitätsnähe und ihrer Prognosefähigkeit weiter zu optimieren. Zu diesem Zweck sind zur Vereinfachung angenommene Randbedingungen und Symmetrieeigenschaften auf ihre Zulässigkeit hin zu überprüfen, ggf. aufzuheben und durch geeignetere zu ersetzen.
Weiterer zentraler Untersuchungsschwerpunkt ist die Modellierung komplizierter geometrischer Profileigenschaften einschließlich der Untersuchung von deren Auswirkungen vor allem auf die Genauigkeit der Berechnungsergebnisse sowie auf Rechengeschwindigkeit und Speicherbedarf.
Um die Genauigkeit und Prognosefähigkeit des FEM-Prozessmodells entscheidend zu verbessern, müssen diese elastischen Randbedingungen in einem umformtechnischen Gesamtmodell berücksichtigt werden. Vorhandene Ansätze sind auf ihre Übertragbarkeit und Anwendbarkeit für die Simulation des APRWs zu prüfen und zu bewerten. Mit einem ausgewählten Ansatz wird ein umformtechnisches Gesamtmodell für das APRW zur Simulation der elasto-statischen Einflüsse aus Maschine und Werkzeug erstellt und bewertet.
Lösungsweg
- Weiterentwicklung und Optimierung des FE-Modells zum APRW
- Modellierung komplizierter Profilgeometrien - Vernetzungsstrategien (Bild 1)
- Parameteridentifikation für das Fließ- und Reibverhalten bei großen lokalen plastischen Dehnungen
- Qualifizierung des Prozessmodells durch Berücksichtigung elasto-statischer Maschinen- und Werkzeugeinflüsse
Ergebnisse
Wie bei allen inkrementellen Umformverfahren erfordert das Ringwalzen lokal an der Kontaktstelle eine sehr feine Diskretisierung, während für den Restkörper eine sehr grobe Unterteilung ausreicht. Die Anwendung der in kommerziellen Programmsystemen implementierten Substrukturtechniken für lineare Superelemente war in der ersten Antragsphase nicht erfolgreich, da - bedingt durch die ständige örtliche Änderung der Kontakt- und damit der Umformzone - der Berechnungsaufwand zur Kondensation der Steifigkeitsmatrix des gerade in Umformung befindlichen Rohrsegmentes auf die externen Elementfreiheitsgrade größer ist als bei einem vollständig fein diskretisierten Modell. In diesem Arbeitpunkt wird die Senkung der Elementanzahl durch intelligente Vernetzungsstrategien als Lösungsansatz gesehen. Durch die Festlegung von definierten Zonen feinerer Neuvernetzung werden in der Kontakt- bzw. Umformzone die kleinen Elementgrößen verwendet, die zur Berechnung der lokalen plastischen Verformungen und damit der resultierenden Geometrien notwendig sind.
Im erarbeiteten Demonstrationsmodell wurde hierzu eine neue Vernetzungsstrategie "Template Ring Meshing" entwickelt (Bild 1) und erfolgreich zur Anwendung gebracht. Diese Technologie war entscheidend, um bei der Simulation des Walzens von Getrieberingen (Bild 3) die Rechenzeit je nach Größe und Detaillierungsgrad um ca. 50 % zu senken.
Für ein ganzheitliches Simulationsmodell ist die Verkopplung der Teilsysteme Maschine und Prozess erforderlich. Zur Modellierung relevanter Maschineneigenschaften wurde die quasistatische Kopplung von FEM-Prozessmodell und Maschinenmodell gewählt (Bild 3). Diese Kopplungsstufe stellt die Erweiterung des FEM-Prozessmodells – im Sinne eines integrierten FEM-Modells – durch Berücksichtigung der statischen Maschineneigenschaften (als reduzierte, ersetzende Beschreibung) in direkter Rückwirkung auf die geometrischen Randbedingungen der FEM-Simulation dar.
Beispielhaft wurde am Simulationsmodell für die Herstellung eines Kugellagerinnenringes der Einfluss des elasto-statischen Verhaltens, d. h. der Auffederung der Walzvorrichtung, auf den Werkstofffluss demonstriert. Hinsichtlich der realitätsnahen Ermittlung des für eine vollständige Profilausfüllung notwendigen Walzenvorschubs konnte die Modellgenauigkeit wesentlich verbessert werden.
Kontakt
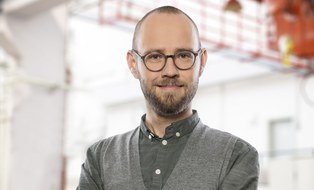
Research associate
NameMr Dr.-Ing. Lars Penter
Senior Engineer Research and Education
Send encrypted email via the SecureMail portal (for TUD external users only).
Chair of Machine Tools Development and Adaptive Controls
Visiting address:
Kutzbach-Bau, Room 106 Helmholtzstraße 7a
01069 Dresden