Strukturbasierte Modellierung des für die Stabilität des Zerspanprozesses relevanten drehzahlabhängigen Übertragungsverhaltens eines Spindel/Werkzeug-Systems
Laufzeit: | 07/2010 – 06/2011 07/2008 – 06/2009 10/2005 – 09/2007 |
Finanzierung: | DFG |
Bearbeiter: | Dr.-Ing. Michael Löser |
Zielstellung
Das dynamische Übertragungsverhalten von rotierenden Spindel-Werkzeug-Systemen ändert sich über der Drehzahl. Dies kann einen Einfluss auf die Stabilität von Zerspanprozessen besitzen. Ziel des Projektes ist es, die Vorteile strukturbasierter und modaler Beschreibungen des dynamischen Verhaltens eines Spindel-Werkzeug-Systems zu verbinden und dabei deren Nachteile zu minimieren.
Lösungsweg
Grundlage des Vorgehens ist es, hinsichtlich der Ersatzparameter eine Separierung der Einflussgrößen vorzunehmen, welche die Drehzahlabhängigkeit verursachen. Damit wird es möglich, den Einfluss der Einzeleffekte isoliert voneinander zu untersuchen. Dies soll durch eine hybride Methode zur Ermittlung modaler Ersatzparameter erreicht werden. Grundlage ist dabei ein möglichst einfaches strukturbasiertes Modell. Für dieses Modell können Abweichungen bezüglich der Abbildung des dynamischen Übertragungsverhaltens toleriert und damit der Aufwand für Modellerstellung und Parameterabgleich verringert werden. Wichtig ist, dass das Modell die Qualität der Drehzahleinflüsse wiedergibt. Diese qualitativen (relativen) Änderungen des Übertragungsverhaltens können dann auf Ersatzparameter übertragen werden, die aus Messungen an der realen Struktur gewonnen wurden. Hierbei reichen Messungen an wenigen Stützstellen aus. Zwischen diesen Stützstellen kann dann das drehzahlabhängige Verhalten modellgestützt interpoliert werden.
Um die Parameteridentifikation und die Untersuchungen zum Modellumfang effizient zu gestalten, wurde unter Matlab ein Script zur strukturbasierten Modellierung des Spindel-Werkzeug-Systems erstellt. Dabei wurde eine FE-Formulierung für Timoshenko-Balken verwendet. Für die Dämpfungsberechnung wurde ein Rayleigh-Ansatz zugrunde gelegt. Die Abbildung von Koppelelementen, wie HSK-Schnittstelle oder Lagersteifigkeiten, erfolgt durch konzentrierte Feder-Dämpfer-Elemente. Da Torsions- und Längsschwingungen der Struktur nicht Gegenstand der Untersuchungen dieses Projektes sind, wurde der Freiheitsgrad der Knoten des Modells auf FG = 4 beschränkt. Es werden nur die translatorischen und rotatorischen Freiheitsgrade senkrecht zur Längsachse der Spindel berücksichtigt.
Ergebnisse
Das Vorhaben zur hybriden – simulativen und messtechnischen – Ermittlung von Übertragungsfrequenzgängen konnte umgesetzt und auf zwei Referenz-Systeme angewandt werden. Je nach Charakteristik des untersuchten Systems lassen sich dabei unterschiedlich gute Prognoseergebnisse erzielen. Mit diesem Vorgehen lässt sich der messtechnische Aufwand zur Ermittlung der drehzahlabhängigen Frequenzgänge und damit die Zeit in der eine Maschine durch Messungen belegt werden muss redu-zieren. Mit dem – zunächst für ruhende Systeme – dargestellten Ansatz zur Kopplung modaler Ersatzbeschreibungen des Spindel-Lager-Systems mit Strukturmodellen des Werkzeug-Futter-Systems lässt sich dieses Vorgehen prinzipiell erweitern und auf andere Spindel-Futter-Werkzeug-Konfigurationen übertragen.
Im Rahmen des Projektes konnten Grundlagen für die mess-technischen Untersuchungen an rotierenden Spindeln bereitge-stellt werden. Es wurden Anforderungen an das Minimalmodel hinsichtlich Diskretisierung, Modellvereinfachung und Modellum-fang definiert. Mit den durchgeführten Sensitivitätsanalysen konnten Parametereinflüsse ermittelt sowie die zu erwartenden Fehler abgeschätzt werden. Die gewonnenen Erkenntnisse sind dabei zumindest qualitativ auf andere Spindel-Lager-Werkzeug-Systeme übertragbar.
Die Quantifizierung von Unsicherheiten, die sich bei einer Anwendung des Vorgehens auf weitere Untersuchungsobjekte ergeben ist allerdings schwierig. Für einzelne Aspekte, wie Parametersensitivitäten sowie messtechnische und modellierungsseitige Einflüsse konnten „lokale“ Aussagen für die untersuchten Referenzsysteme gemacht werden, die sich allerdings auch je nach Charakteristik (z.B. der Einbausituation) für die beiden Systeme unterscheiden. Für die Bereitstellung einer bewerteten Aussagefähigkeit der Modelle anderer Untersuchungsobjekte müssten die Einzelaspekte und ihr Zusammen-wirken systematisch aufbereitet und zusammengefasst werden. Dies könnte Aufgabe zukünftiger Forschungsarbeiten sein.
Kontakt
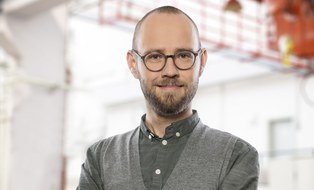
Research associate
NameMr Dr.-Ing. Lars Penter
Senior Engineer Research and Education
Send encrypted email via the SecureMail portal (for TUD external users only).
Chair of Machine Tools Development and Adaptive Controls
Visiting address:
Kutzbach-Bau, Room 106 Helmholtzstraße 7a
01069 Dresden