Development of a technology module for inductively supported heavy-duty machining
Table of contents
Duration: |
04/2024 - 03/2026 |
Funding: | This project is funded by the Federal Ministry of Economics and Climate Protection (BMWK) on the basis of a resolution of the German Bundestag. |
Author: | Dipl.-Ing. Frank Arnold |
Cooperation: |
Himmelwerk Hoch- und Mittelfrequenzanlagen GmbH |
Motivation
Heavy-duty machining occupies a special position in the field of machining. In addition to the machining of components with very large dimensions and high metal removal rates, this also includes the machining of complex geometries and difficult-to-machine materials such as titanium, high-temperature and high-strength steels or nickel-based alloys. High process costs due to high tool wear and significantly longer machining times are currently still technological limits. Hybrid processes, which combine several active mechanisms or processes parallel to the main process in the same active point, can combine the advantages of the individual active mechanisms and reduce the disadvantages of the individual processes. This leads to higher process performance, better machining results and lower process forces with longer tool life. Heat-assisted machining processes are an effective method for machining difficult-to-cut materials. The workpiece is preheated locally on the surface by an energy source immediately before machining. The material is locally softened at the heated point, which significantly improves machinability or, in the case of some materials, makes it possible in the first place.
The integration of inductive heat sources into the process control is a promising approach. The advantages of inductive heating lie in the possibility of applying heat locally and at a time and place shortly before tool engagement, as well as in the good adjustability of the heating process with regard to the temperature achievable in the workpiece, the local heat limitation and the heating depth. Due to a lack of scientific preparation, the process is not yet available on the market.
Aim of the project
The aim of the project is the engineering-oriented penetration of induction-assisted turning and the development of a corresponding technology module. The project aims to achieve the following sub-goals:
- Heating the edge zone of a workpiece before the tool cutting edge to a defined temperature at a defined depth measured from the workpiece surface
- Heating only the zone to be machined immediately after heating
- Softening of the material in the heated edge zone to be machined
- Increase of the cutting parameter feed rate by at least 50%
- Reduction of cutting forces and performance by at least 25%
- Increase tool life by at least 50%
- Improvement of the overall balance with regard to the use of resources compared to conventional heavy-duty machining
Research idea
The research idea consists of integrating an inductive heating module into a lathe and developing an associated cross-domain process model to quickly determine the machining parameters under various target specifications.
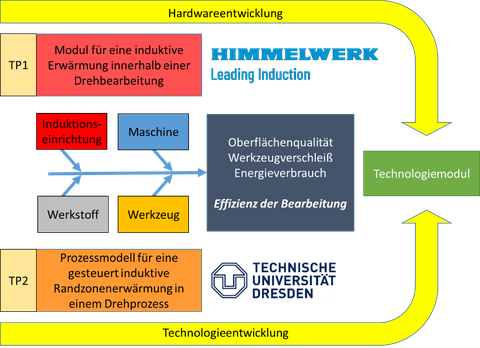
Lösungsansatz
The challenge
A complete model approach that includes all parameters to be considered is not yet known. The non-constant and partly unknown material properties significantly influence the heating parameters and thus the efficiency of the process and the quality of the machined workpiece. The electromagnetic material properties in particular are neither to be found in tables nor are they easy to determine. How the fluctuations and uncertainties of the material properties can be mapped in the process model and thus how useful predictions can be made is the subject of the work. Against the background of current developments, energy efficiency is of particular importance. Due to the additional heat input, the process model to be developed for control and regulation must ensure high efficiency of the overall process.
Path to solution
The following steps are necessary to achieve the objectives:
- Recording the relevant turning process parameters and developing a process model for hybrid, induction-assisted heavy machining with simulative investigation.
- Development of control and regulation algorithms for the heating process, taking into account all necessary parameters.
- Carrying out heating tests, metrological monitoring and evaluation to investigate the effects of changing the main parameters feed and speed on the control and regulation algorithms of the induction system on a test stand together with the project partner Himmelwerk.
- Development of a feasible concept for the integration of all necessary components for process monitoring and control of induction-assisted turning in an existing machine and integration into the turning process.
- Testing of the control and regulation algorithms on a test machine, implementation, metrological monitoring and evaluation of machining tests to evaluate the algorithms and the overall process.
Results
The result is an industrially applicable technology module for inductively supported heavy-duty machining for integration into existing machines. This technology module comprises the technical components and conductive algorithms for controlling and regulating the hybrid machining process. Its use reduces the cutting forces and performance and thus enables economical machining even on machines that are not specially designed for this purpose.
Current status
So far, preliminary tests have been carried out to identify development challenges, see figure.
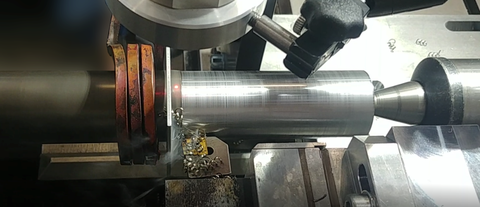
Versuchsaufbau mit Induktionsspule links sowie Werkstück und Drehmeißel rechts
Publications
Arnold, F.; Krishnamurthy, N. M.; Prasse, J.; Penter, L. & Ihlenfeldt, S.: Simulation and practical investigation of inductively assisted machining using the example of turning operations Acta Technica Napocensis - Series: Applied mathematics, mechanics, and engineering,2023, 66- https://atna-mam.utcluj.ro/index.php/Acta/article/view/2315
contact
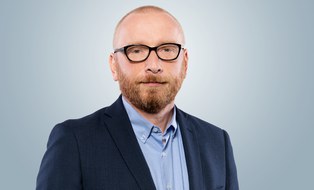
Research associate
NameMr Dipl.-Ing. Frank Arnold
Process Informatics and Machine Data Analysis
Send encrypted email via the SecureMail portal (for TUD external users only).
Chair of Machine Tools Development and Adaptive Controls
Visiting address:
Kutzbach-Bau, Room E5 Helmholtzstraße 7a
01069 Dresden