Simulative und experimentelle Analyse des Umformvorganges von Karton durch Ziehen
Laufzeit: | 2014-2017 |
Finanzierung: | AIF / IVLV |
Bearbeiter: | Dr.-Ing. Lars Penter |
Kooperation: | Lehrstuhl für Verarbeitungsmaschinen und Verpackungstechnik |
Zielstellung
Die Weiterentwicklung von Prozessen, denen so komplex vernetzte physikalische Zusammenhänge zugrunde liegen wie sie bei der 3D Umformung von Karton durch Ziehen festgestellt wurden, gelingt nur, wenn diese Zusammenhänge entkoppelt wissenschaftlich analysiert werden. Für eine schrittweise Entkopplung des thermodynamischen und tribologischen Systems voneinander und von den rheologischen Vorgängen im Material stehen derzeit verschiedene Simulationsstrategien und -werkzeuge zur Verfügung, die für sich betrachtet nicht in der Lage sind den gesamten Umformprozess integrativ abzubilden. Aus diesem Grund ist es Ziel des Projektes Teilmodelle zu erstellen, die die auftretenden Spannungszustände simulieren und diese zusammen mit separaten Modellen für die Erfassung des thermodynamischen Zustandes und des Reibverhaltens über definierte Schnittstellen zu einem Prozessmodell auf Basis einer Multiskalenmodellierung zu verbinden.
Lösungsweg
Die einzelnen Teilmodelle orientieren sich an den für die Umformung maßgeblichen physikalischen Wirkmechanismen bei der Faltenentstehung, der Beeinflussung der rheologischen Eigenschaften durch die thermodynamischen Zustandsgrößen Temperatur und Feuchte im Material, der Beeinflussung des Reibverhaltens und der Fixierung des Materials im umgeformten Zustand. Für diese Teilsysteme sind zunächst Modelle zu wählen, anzupassen oder neu zu entwickeln und zu verifizieren. Da die bekannten Prüfmethoden für Kartonmaterialien keinen Rückschluss auf das Materialverhalten unter den prozessspezifischen Bedingungen zulassen, ergibt sich das Ziel zusätzlich zu dem derzeit im Projekt ZIM KF 2104316WZ entwickelten Reibmessgerät Prüfmethoden und zugehörige Prüfvorrichtungen zu entwickeln, mit denen notwendige Materialdaten für die Modelle zur Verfügung gestellt werden können. Gleichermaßen wird die Erarbeitung der Teilmodelle aufzeigen, welche weiterführenden Messungen spezifischer Prozessgrößen notwendig sind, um eine Verifikation der entsprechenden Teilsysteme zu ermöglichen und die Aussagekraft des Gesamtmodells zu sichern.
Ergebnisse
Zur numerischen Berechnung der Faltenbildung im Stauchversuch wurde ein 2-dimensionales Modell des Kartonstreifens erstellt (siehe Bild 1). Das Schichtmodell besteht aus Hexaederelementen. Die Deck- und Kernschicht werden durch eine kohäsive (zusammenhaltende) Schicht aus Kontaktelementen verbunden. Mit dieser Schicht ist das Modell in der Lage die Delamination der Kartonschichten qualitativ nachzubilden. Zusätzlich müssen zwischen den Schichten Kontakte definiert werden, welche im Delaminationsfall ein Durchdringen der Schichten verhindern. Die Delamination kann im Modell ausschließlich in den definierten Schichten erfolgen. Für die Nachbildung des tatsächlichen Delaminationsverhaltens ist die Modellierung weiterer kohäsiver Kontaktschichten notwendig.
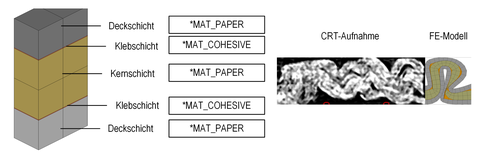
Bild 1: 2D-Modell des Stauchversuches
Das Simulationsmodell ist in der Lage das Knickverhalten des Kartons qualitativ nachzubilden. Die Faltenbildung wird maßgeblich durch die Delamination der Kartonschichten charakterisiert. Sobald sich eine Falte gebildet hat reagiert das Modell sehr sensitiv auf den kurzzeitig einbrechenden Widerstand. Daher ist die ermittelte Reaktionskraft von starken Schwingungen geprägt. Die Elemente in den Innenradien der Falten werden sehr stark deformiert. Wird ein Grenzwert überschritten, werden diese Elemente gelöscht (Bild 2).

Bild 2: 2D-Simulation des Stauchversuches mit Delaminationsverhalten
Die relativ einfachen 3D-Prozesssimulationsmodelle (Bild 3) liefern qualitative Trends hinsichtlich der zu erwartenden Stempelkraft, des Flanscheinzuges und der dazu notwendigen Werkzeugtemperaturen. Es ist wurde gezeigt, dass es möglich ist die signifikanten Einflüsse der Temperatur, der Ziehgeschwindigkeit, der Versuchsanzahl und der Anfangsfeuchtigkeit auf den Flanscheinzug für ein rotationssymmetrisches Bauteil darzustellen. Damit lassen sich in Zukunft Prozesse für komplexere Bauteile hinsichtlich Werkzeugoberflächen und -temperaturen auslegen. Aufgrund der verwendeten Materialmodelle aus der Metallumformung bleibt der Parametrierungsaufwand für das Prozessmodell überschaubar. Der Einsatz von auf Karton spezialisierten Materialmodellen für die Prozesssimulation erscheint für produzierende KMU aufgrund der umfangreichen Parametrierung als zu aufwendig.
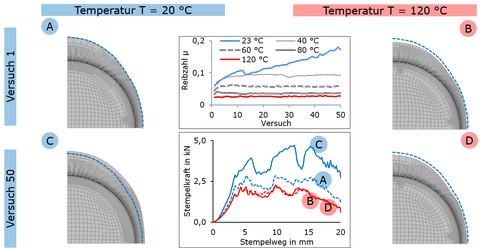
Bild 3: thermo-mechanisches 3D-Simulationsmodell des Kartonumformprozesses
Veröffentlichungen
Lenske, A. ; Müller, T. ; Penter, L. ; Schneider, M. ; Hauptmann, M. ; Majschak, J.-P. : Evaluating the factors influencing the friction behavior of paperboard during the deep drawing process. In: BioResources 12 (2017), Nr. 4, S. 8340–8353 Volltext |
Schneider, M. ; Kabel, M. ; Andrä, H. ; Lenske, A. ; Hauptmann, M. ; Majschak, J.-P. ; Penter, L. ; Hardtmann, A. ; Ihlenfeldt, S. ; Westerteiger, R. ; Glatt, E. ; Wiegmann, A. : Thermal fiber orientation tensors for digital paper physics. In: International Journal of Solids and Structures 100–101 (2016), S. 234 – 244. – ISSN 0020–7683 Link |