Near-wall flows in turbomachine cascades
Secondary flows in the sidewall area of turbomachines are extremely complex flows. On the other hand they have a large impact on the operating behaviour of such devices, e.g. the stall margin, and the generated losses.
The secondary flow itself consists of several components, such as the horseshoe vortex, the channel vortex, and possibly the tip gap vortex. These interact with each other and form a dynamic system which also interacts with the main flow and the boundary layer. On top of this, there is the transient wake of upstream blades, which not only changes the main flow, but also shapes the secondary flow. Thus, a highly dynamic complex flow is present in the sidewall areas of turbines and compressors.
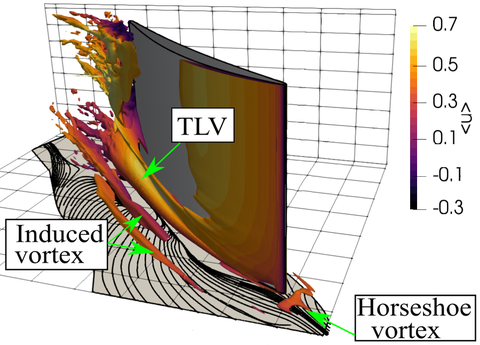
Turbine blade with exiting vortices
In general, sidewall losses represent about one third of the total losses of turbines and are of even greater importance for compressors. These effects must, therefore, be taken into account in the design of turbomachines and have to be predictable by simulations. In the literature there are numerous investigations on the radial gap vortex, for example but primarily limited to flat cascades without rotation. The situation in rotating ring cascades differs from this and has not been sufficiently investigated in terms of the impact of rotation on this feature, especially not with turbulence-resolving numerical simulations.
The current industrial standard for the simulation of turbomachinery is two-equation Reynolds Averaged Navier-Stokes (RANS) or Unsteady RANS (URANS) methods. By design, it is therefore difficult to reliably predict strongly anisotropic turbulence, large-scale vortex structures and transition effects. Individual Large Eddy Simulations (LES) of turbomachinery flows have proven the fundamental advantage of turbulence-resolving approaches, but do not always achieve the best possible result. The main reason is the complexity of such flows, e.g. due to transition phenomena, and the submodels used in the methods are not suitable enough. To date, there are only few activities that go beyond the application of the most basic models. Hence, there is a great need for improved turbulence-resolving methods with submodels well adapted to the turbomachinery sector.
Looking into the future, increasing computational capacity will allow to employ turbulence-resolving methods such as LES also in an industrial context. For this to be possible, however, these methods must be further developed and validated to handle transition flows as well as lower Reynolds number cases found in the turbomachinery sector.
On this background, the project has two main objectives. The first is to study the physics of secondary flows in a rotating cascade and compare it with that of a linear cascade. The second is to develop a reliable simulation methodology in the context of LES simulations of turbomachine cascades. Both tasks will focus on flows through a compressor. The work in the computational project described here is carried out within the DFG-funded package proposal PAK948, where the other partners carry out experimental measurements and further simulations using RANS/URANS.
Cooperation | Professur für Turbomaschinen und Flugantriebe, TU Dresden |
Funding | DFG under Grant FR1593/15-1 within the package proposal PAK948 |
Contact |
Dipl.-Ing. Moritz Kreuseler |