Rotorkühlung für Asynchronmaschinen in hochdynamische Anwendungen
Hochdynamische elektrische Asynchronmaschinen werden aufgrund ihrer Robustheit in Prüf- und Produktionsanlagen eingesetzt. Der Einsatz ist durch häufige Drehmomentwechsel gekennzeichnet, wobei ein Arbeitszyklus auch nur eine einzige Umdrehung umfassen kann. Daraus resultieren besondere Anforderungen an diese Antriebe. Zum einen ist ein Rotor mit geringem Trägheitsmoment erforderlich und zum anderen müssen die im Vergleich zu anderen Maschinen erhöhten thermischen Lasten sicher abgeführt werden. Bekannte Kühlsysteme werden diesen besonderen Anforderungen nur unzureichend gerecht. Deshalb wird ein neuartiges Konzept mit einer direkten Rotorkühlung über radiale Kühlkanäle untersucht, welches die Wärmeabfuhr näher an den Wärmequellen ermöglicht.
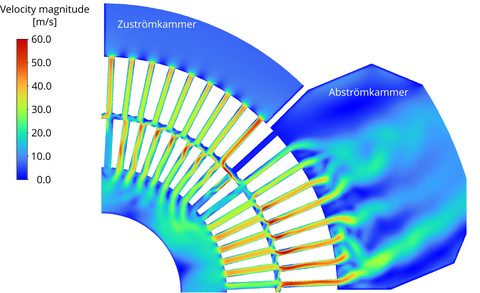
Darstellung des Geschwindigkeitsbetrags innerhalb der radialen Kühlspalte. Die Ergebnisse stammen aus einer numerischen Simulation mit Fluent.
Aufgrund der Komplexität der Gesamtmaschine können nicht alle relevanten Phänomene in ihrem zeitlichen Verlauf aufgelöst und gekopplet mit Feldberechnungsmethoden simuliert werden. Deshalb erfolgen separate elektromagnetische, festkörpermechanische und thermische Simulationen mittels FEM sowie CFD-Simulationen mit gekoppeltem Wärmetransport im Festkörper. Dadurch können relevante Phänomene unter kritischen Lastbedingungen und während kompletter Lastzyklen identifiziert und analysiert werden. Darauf aufbauend erfolgen multiphysikalische Simulationen auf Basis der Netzwerkmodellierung, mit denen längere Betriebszeiträume analysiert werden können. Alle Simulationsmodelle werden anhand von Modellexperimenten validiert. Hierfür wird ein Scheibenmodell des Antriebs verwendet, das die optische Zugänglichkeit zu den radialen Kühlkanälen für optische Messungen der Strömungsgeschwindigkeit gewährt und die thermischen Zustände der realen Maschine nachbildet.
Durch das Projekt soll ein Grundlagenverständis für das neuartige Kühlsystem geschaffen werden. Insbesondere sind die folgenden Forschungsfragen zu beantworten:
- Wo und wann treten thermisch kritische Zustände im Motor auf? Wie können diese vermieden werden?
- Wie groß ist das Leistungspotential der Gesamtmaschine bei Einsatz der Radialkühlung im Vergleich zu bisherigen Kühlverfahren und wie kann dieses bestmöglich ausgenutzt werden?
- Wo liegen die methodischen Grenzen der eingesetzten Simulationsverfahren und wie sieht die Modellstruktur für die verschiedenen Verfahren für eine aufwandsoptimale Simulation der Radialkühlung einer solchen hochdynamischen Maschine aus
Finanzierung | DFG under Grant FR 1593/19-1 |
Kontakt |