Experimental investigation and numerical modeling of chip collection during groove sawing or groove milling of wood-based materials as a basis for their optimization (groove sawing modeling)
Woodprocessing differs in several aspects from conventional machining processes, where the collection and removal of chips and dust is the biggest problem. Due to the material properties of wood, cooling fluids cannot be used to flush the chips. Combined with the high energy cost of chip removal and the danger it poses to the operator and the workplace, this is the reason for the development of special chip removal solutions. However, these are very machine, tool and process specific and therefore require a long development time that smaller companies cannot cope with.
To study this case, one of the highly employed processes used by the furniture industry, such as grooving, where a channel is milled on a plate to later be used in the mounting steps, has to be investigated. Grooving proves to be troublesome, not only in the removal of chips from the air and the milled groove, but also for the modelin. A rotating tool that removes material by cutting from a plate moving under it, producing and ejecting a wide size and shape distribution of wood chips, has to b e modeled. For an accessible simulation method, a commercial software is used to simulate simplified point-particles trajectories from the cutting tool. The estimation of the necessary empirical coefficients used by this simplified model will be obtained through fully-resolved simulations. As a comparison, own experimentally determined data can be used.
Funding period 1
For a simulation method practicable in an industrial application, commercial software is used to simulate chip ejection and chip collection with simplified point-particle trajectories from the cutting tool. The estimation of the required empirical coefficients for non-spherical particles used by this simplified model was supported by fully resolved simulations. Own experimentally determined data was used for comparison.
Goal of the project was to present a modelling approach, by identifying usable models, and estimating their associated deviations. By decoupling the simulation of the tool-induced flow from the simulation of the chip flight and chip capturing, and by combining CFD simulation for the flow field with DEM simulation of the motion and collisions of the larger chips, a good compromise between effort and accuracy was found. With this methodology, it was possible to expemplarily design a modified solution for chip capturing.
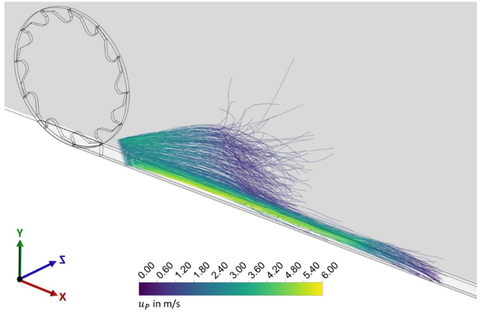
Simulation of chip flow during wood grooving.
The final report of the project can be obtained from the Forschungskuratorium Maschinenbau (FKM) e. V. (Postal address: Lyoner Str. 18, 60528 Frankfurt am Main, E-Mail: info@fkm-net.de, Tel.: +49 69 6603 1352).
Funding period 2
Due to the broad variety of chip size and shapes, the coupling between fluid and particle simulation (CFD-DEM coupling) is being pursued further as a promising approach for modelling and simulating wood machining.
The investigation of practical use cases with the simulation methodology to be developed in combination with corresponding experimental investigations serves to demonstrate the validity of the models and the practicability of the method. Concrete design recommendations and reduced simulation models are also to be derived from these investigations and made available to SMEs in the industry in particular.
Cooperation |
Chair of Wood and Fibre Material Technology. TU Dresden |
Funding |
BMWK |
Contact |