Studentenexkursion 2017
Table of contents
- Besuch der Dienes Apparatebau GmbH
- Besuch der Lindauer DORNIER GmbH
- Besuch der Groz-Beckert KG
- Besuch der MAGEBA Textilmaschinen GmbH & Co. KG
- Besuch der KARL MAYER Textilmaschinenfabrik GmbH
- Besuch des VDMA Textile Care, Fabric and Leather Technologies
- Besuch der Brother Internationale Industriemaschinen GmbH
Dieses Jahr besuchten die Studierenden des ITM vom 09. bis 12. Mai 2017 die TECHTEXTIL und TEXPROCESS in Frankfurt und besichtigten neben zahlreichen Messe-Highlights zahlreiche Firmenmessestände.
Ein herzliches Dankeschön gilt allen Firmen für die interessanten Präsentationen
und insbesondere der Walter Reiners-Stiftung des VDMA, dem Fachverband Textile Care, Fabric and Leather Technologies des VDMA, der Fakultät Maschinenwesen der TU Dresden sowie dem Freundes- und Förderkreis des ITM für die finanzielle Unterstützung der diesjährigen Studentenexkursion.
German Resource Efficiency Award 2016 for the ITM at TU Dresden and the Oskar Dilo Maschinenfabrik KG for the realization of a unique method for the production of rCF high-performance hybrid yarns for fiber-reinforced composite materials © ITM/TUD
Die zweijährliche Techtextil-Messe in Frankfurt am Main gilt neben der Internationalen Textilmaschinen-Ausstellung (ITMA) als weltweit größte Messeveranstaltung im Bereich des Textilmaschinenbaus und der textilen Verarbeitung. Die ebenso zweijährliche Texprocess-Messe ist die internationale Leitmesse für die Bekleidungs- und textilverarbeitende Industrie.
Wie bereits in den vergangenen Jahren wurde auch im Sommersemester 2017 durch die großzügige Unterstützung des VDMA der Messebesuch für etwa 50 Studierende des ITM der TU Dresden zur TECHTEXTIL und TEXPROCESS ermöglicht.
Die selbstständige Erkundung der Messe mit vielfältigen Firmenpräsentationen und Neuheiten wurde durch die Besuche der Firmen Dienes Apparatebau GmbH und KARL MAYER Textilmaschinenfabrik GmbH, sowie durch exklusive Führungen über die Messestände der Firmen Groz-Beckert KG, Lindauer DORNIER GmbH, MAGEBA Textilmaschinen GmbH & Co. KG, Brother Internationale Industriemaschinen GmbH und einer Vorstellung des VDMA Textile Care, Fabric and Leather Technologies ergänzt.
Besuch der Dienes Apparatebau GmbH
Fritz Dienes hat das Unternehmen DIENES in 1930 in Mühlheim am Main gegründet. In der Startphase produzierte DIENES neben elektrischen Schaltern auch Spielzeugherde mit integrierten Heizungen. Ab 1938 wurden die ersten Komponenten zur Perlonherstellung entwickelt und umgesetzt und damit der Einstieg in den Textilmaschinenbau realisiert. Die Entwicklung der ersten induktiv geheizten Galetten stellte 1968 den nächsten großen Schritt in der Herstellung von Textilmaschinenbauteilen dar. Aufbauend darauf wurden 1986 die ersten Module für Produktionsmaschinen zur Herstellung von Hochleistungsfasern (Aramid) hergestellt. 1988 entwickelte das Unternehmen die MF-Heiztechnik für Galetten. Heute hat sich DIENES als Sondermaschinenbauer für Labor- und Prototypspinnanlagen für die Herstellung von Synthesefasern etabliert. Schwerpunkt sind heute Anlagen für Prozesse im Bereich von Hochleistungsfasern.
Die Firma DIENES konstruiert und realisiert komplette Prototypanlagen im Lösemittel- und Schmelzspinnbereich. Die Anlagen bestehen aus einzelnen Modulen, die durch eine sehr flexible Steuerung im MultiMode-Prinzip zusammengefügt werden.
Bis zum heutigen Tage hat die Firma DIENES folgende Labor- und Prototyp-Anlagen realisiert:
- Nassspinn-Anlagen zur Herstellung von Carbon-Precursor,
- Anlagen zur Oxidierung und Carbonisierung von Carbon-Precursor,
- Aktivierungslinien für Carbonfasern,
- Schmelzspinn-Anlagen (Mono und Biko),
- Verschieden Streckfelder und Waschlinien,
- Beschichtungs-Anlagen und
- Nanofaser-Spinnanlagen.
Die Entwicklung der LabLineCompact (LLC) Nassspinnanlage, welche im Jahr 2016 von der Firma DIENES abgeschlossen wurde, zeigt die Innovationskraft der Firma. Diese Labor-Nassspinnanlage findet aufgrund ihrer ausgezeichneten Flexibilität ihren Einsatz in verschiedenen europäischen Forschungs- und Entwicklungseinrichtungen. Dort werden verschiedene Untersuchungen, vor allem auf dem Gebiet der Biopolymeren und synthetischen Polymeren durchgeführt. Fast alle Polymer- und Lösungsmittelkombinationen können verwendet werden, da hochlegierte Edelstähle und korrosionbeständige Beschichtungen verwendet werden. Die Spinnpumpe erlaubt einen Durchsatz von 0,01 - 15 ml/min andere Durchsätze sind auf Wunsch möglich.
Eine weitere Entwicklung der Firma DIENES ist eine Zentrifugenspinn-Anlage, die gemeinsam mit der Firma REITER GmbH & Co. KG Oberflächentechnik eigens für das neue KeyLab der Universität Bayreuth konzipiert wurde. Die technologische Neuerung besteht darin, dass in der Anlage zwei Komponenten miteinander versponnen werden, die zwar für sich bereits bekannt sind, aber noch nie miteinander kombiniert wurden.
Die Firma DIENES hat darüber hinaus erfolgreich eine Lignin-Schmelzspinnanlage in einem deutschen Forschungszentrum installiert. Die Anlage ist im Produktionsmaßstab ausgeführt, so dass Forschungsergebnisse unmittelbar auf industrielle Anlagen übertragbar sind. Darüber hinaus ist die Anlage durch den Einsatz der DIENES MultiMode® Steuerungsphilosophie flexibel auf neue Anforderungen anpassbar und damit perfekt für die Anwendung als Forschungsmaschine.
Wir bedanken uns recht herzlich bei der Firma DIENES Apparatebau GmbH und insbesondere bei Herrn Müller-Probandt für die Durchführung des Rundganges auf dem Firmengelände mit so vielen Teilnehmern und für die außerordentlich überzeugende Vorstellung der Firma sowie deren Produkte.
Besuch der Lindauer DORNIER GmbH
Am 10.05.2017 besuchte das ITM der TU Dresden den Messestand der Lindauer DORNIER GmbH. Herr Karcier stellte der Gruppe von circa 50 Studenten und Mitarbeitern das Unternehmen vor. Das Traditionsunternehmen wurde 1922 unter dem Namen Dornier-Metallbauten GmbH in Manzell am Bodensee gegründet. Der heutige Hauptsitz befindet sich im nahegelegenen Lindau. Weitere Standorte sind weltweit verteilt in Shanghai, Mumbai, Istanbul und Charlotte (USA).
Das Unternehmen stellte ursprünglich Flugzeuge her (z.B. Do X oder Do Delphin III). Besonders hierbei war, dass Professor Claude Dornier sich entschied, Holz und Leinentuch durch Aluminium zu ersetzen. Dadurch entstanden die ersten metallenen Flugzeuge.
Nach dem zweiten Weltkrieg war es den Deutschen verboten, Kriegsgerät und Flugzeuge herzustellen. Aufgrund dieser Produktionsbeschränkungen verlegte Dornier den Firmensitz nach Zug in der Schweiz. 1950 wurde für einen Neuanfang in Deutschland die Tochterfirma Lindauer DORNIER GmbH von Peter Dornier, dem Sohn von Claude Dornier, gegründet. Aufgrund der hohen Nachfrage an Webstühlen und Ersatzteilen für im Krieg zerstörte Maschinen entschied sich Peter Dornier für eine Erschließung dieses Fachgebiets. Die durch den Flugzeugbau gesammelten Erfahrungen erwiesen sich als äußerst nützlich und praktikabel.
Die erste Produktion umfasste selbst entwickelte Schützenwebmaschinen und Trocknungsanlagen für die Papp- und Papierindustrie. Mit der 1967 entwickelten Greiferwebmaschine erklomm die Firma Dornier den Weltrang.
1985 spaltete sich die Sparte von der Dornier Unternehmensgruppe ab und wurde von Peter Dornier als eigenständige Firma, der Lindauer DORNIER GmbH, weitergeführt.
Die heutige Produktpalette siedelt sich ausschließlich im textilen Bereich an. Es werden Webmaschinen für konfektionelle sowie technischen Anwendung von Textilien gebaut. Das heißt, die Endprodukte haben eine breite Einsatzpalette von Anzügen, über Airbags, bis hin zu Filtern. Dabei platziert sich die Firma auf dem heutigen Markt mit dem Anspruch Weltmarktführer zu werden. Die drei Standbeine des Unternehmens werden im Folgenden kurz angerissen.
- Die aktuelle Maschinenplattform P2, als Nachfolger der P1-Plattform, bietet mit verschiedenen Modulen individuelle und auf den Kunden zugeschnittene Lösungen.
- Die zweite Kernkompetenz stellen die Sondermaschinen dar, die zur Herstellung von Folien benutzt werden. Zum Beispiel werden TV Bildschirme oder Verpackungen hergestellt.
- Seit 2014 gibt es außerdem den neuen Bereich der Composite-Systeme. Hier werden Spreizanlagen für Carbonfasergarne hergestellt. Des Weiteren werden sogenannte Tapes verwoben, um Flächen zu bilden. Auch 3D-Webmaschinen in Kombination mit einer Jacquard-Maschine werden erforscht und hergestellt, um dreidimensionale Gewebe zu erzeugen.
Früher sowie heute sind die Produkte stets „Made in Germany“. Das höchste Gut des Unternehmens ist das Know-How. Aufgrund des starken Wettbewerbes, gilt es dieses Wissen zu schützen, ohne die Produkte der eigenen Kundschaft unzugänglich zu machen. Deshalb forscht das Unternehmen ständig weiter und investiert in die gute und grundlegende Ausbildung seiner Mitarbeiter.
90 % aller gewebten Carbonfaser-Produkte stammen von Maschinen der Firma Lindauer DORNIER GmbH. Die Materialen, die auf den Maschinen verarbeitet werden sind so vielfältig wie die Endprodukte selbst. Neben Carbonfasern können genauso Aramid-, Basalt- oder Glasfasern auf den Maschinen verarbeitet werden.
Wir bedanken uns recht herzlich bei der Firma Lindauer DORNIER GmbH und insbesondere bei Herrn Karcier für die Durchführung des Rundganges mit so vielen Teilnehmern und für die außerordentlich überzeugende Vorstellung der Firma sowie deren Produkte.
Besuch der Groz-Beckert KG
Die Firma Groz-Beckert KG wurde 1852 in Albstadt-Ebingen als Produktionsfirma für Strickmaschinennadeln gegründet. Heute umfasst ihr Produktprogramm die Bereiche Knitting, Weaving, Felting, Tufting, Carding und Sewing mit etwa 70.000 verschiedenen Produkttypen. Bis auf den Bereich Tufting war die Firma auf der Techtextil 2017 mit allen Produktbereichen vertreten. Die firmeneigenen Produkte waren in verschiedenen Demonstratoren aus Acryl für die Besucher gut sichtbar und teilweise zum Anfassen und Herausnehmen präsentiert.
Aufgrund der breiten Produktpalette war die Firma sowohl auf der Techtextil, als auch auf der Texprocess vertreten, wobei der eigentliche Stand sich im Bereich der Techtextil befand. Die für den Bereich der Technischen Textilien wichtigste Produktsparte stellt der Bereich Knitting dar. Technische Textilien gewinnen in allen Produktbereichen des Unternehmens seit Jahren an Relevanz. Dabei spielen auch feinste Feinheiten eine entscheidende Rolle.
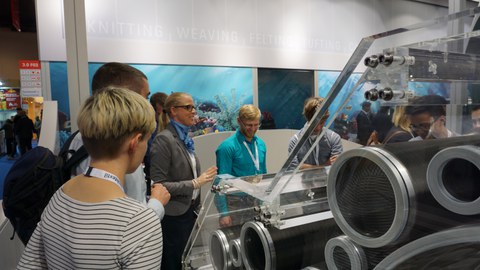
Studierende des ITM am Messestand der Firma Groz-Beckert
So führte der eigene Anspruch des Unternehmens führte zur Entwicklung der feinsten Strickmaschinennadeln E66 im Jahre 2007. Nur vier Jahre später brach das Unternehmen diesen eigenen Weltrekord erneut, indem sie es Produkte präsentierten, mit denen eine Gestrickfeinheit von E90 produziert werden kann.
In den Produktionslinien der Kunden von Groz-Beckert im Bereich Sewing werden vor allem aus versicherungstechnischen Gründen alle Nadelschäden protokolliert und archiviert. Hierbei werden ausnahmslos alle Bruchstücke der Nadel gesammelt und aufgeklebt, entsprechende Informationen zu den Umständen beigefügt und das Ganze in Ordnern archiviert. Derartig genaue Protokollierung ist notwendig und sinnvoll für die Produktion, die vielen Ordner verursachen jedoch auch hohe Lagerkosten. Das Ziel von Groz-Beckert ist es, an dieser Stelle im Sinne der Industrie 4.0 eine Digitalisierung der Schadensaufnahme zu implementieren und so die aufwändige analoge Archivierung zu reduzieren.
Seit 2015 gibt es den neuen Produktbereich Carding, aus dem sich 2016 überdies der Produktzweig Spinning entwickelte, der die beiden Industriezweige Nonwovens und Spinning bedient. Auf der Messe wurden entsprechend auch Kardierwalzen mit den Beschlägen von Groz-Beckert präsentiert.
Kundenzufriedenheit ist eines der wichtigsten Merkmale, an denen sich die Firma Groz-Beckert orientiert. So wird beispielsweise auf der Homepage des Unternehmens nicht nur ein Webshop angeboten, sondern auch ein umfassendes „Kundenportal“, welches auch bspw. ein eigenes Wiki beinhaltet. Darüber hinaus wird die App „myGrozBeckert“ für Smartphones und Tablets angeboten, womit den Kunden nicht nur Informationen, sondern auch Berechnungsfunktionen und Kommunikationshilfen zur Verfügung gestellt werden.
Der Besuch der Präsentationsfläche von Groz-Beckert auf der Techtextil 2017 für die Studierenden des ITM war sehr gut organisiert und informativ gestaltet. Die große Delegation von mehr als 50 Personen wurde für die Besichtigung in drei Gruppen unterteilt, die nacheinander von Frau Kleefisch über den Stand geführt wurden. Den Studierenden wurde ein Eindruck über die Firmengeschichte, die Produktpalette und die aktuellen Entwicklungen vermittelt. Im Anschluss an die Präsentation konnten die Studierenden sich eigenständig auf dem Messestand umschauen und sich mit den Produkten vertraut machen. Das Fachpersonal von den verschiedenen Produktbereichen der Firma hat noch offene Fragen anschaulich beantwortet. Als Erinnerung an den Besuch hat jeder Studierende ein Handyladekabel bekommen. Wir danken der Firma Groz-Beckert für die Möglichkeit des Besuchs Ihres Standes auf der Techtextil und bedanken uns auch für die sehr anschauliche und hochinformative Führung sowie für die freundliche Betreuung.
Besuch der MAGEBA Textilmaschinen GmbH & Co. KG
Die Firma MAGEBA Textilmaschinen GmbH & Co. KG wurde im Jahr 1957 in Wuppertal-Barmen durch Hans-Josef Stang gegründet. Ursprünglich wurden Färbe- und Ausrüstanlagen für Schmalgewebe hergestellt. Heutzutage stellt die Firma Schär- und Webmaschinen her, genauso wie Maschinen zur Veredlung, Beschichtung und Aufmachung von Textilien. Das Unternehmen ist in dritter Generation familiengeführt.
Während der Exkursion zur Techtextil hatten wir das große Vergnügen die Firma und einige ihrer neuesten Innovationen kennenzulernen. Vorgestellt wurden uns zwei Schützenwebmaschinen zur Herstellung technischer und medizinischer Textilien.
Erstere Maschine hatte einen Schützen zur Herstellung von ein- und mehrlagigen Bandgeweben mit aufgesetzter Schlaufe und einer maximalen Maschinendrehzahl von 120 Schuss pro Minute.
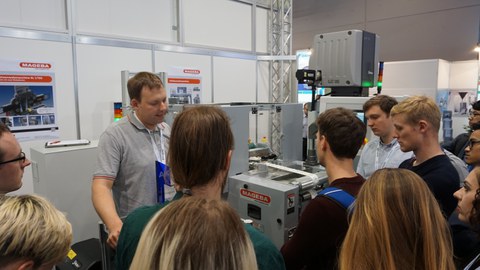
Besuch des Messestandes der Firma MAGEBA Textilmaschinen GmbH & Co. KG auf der Techtextil
Das fabrizierte Muster, ein Schlaufengewebe, entsteht durch das Weben eines dünnen Bandes und durch das nachfolgende Zurückziehen des Bandes in Ausgangsposition. Danach wird an der Ausgangsposition ein breiteres Band angewebt. Das uns vorgestellte Muster ist jedoch nicht das einzige, auf dieser Maschine produzierbare, es können auch mehrlagige Gewebe, wie zum Beispiel T-Stücke, hergestellt werden. Für die Umsetzung derartiger mehrlagiger Gewebe ist jedoch ein Linearabzug von Vorteil, damit die gewebten Stücke ohne Strukturverzerrung hergestellt werden können. Die Kettfäden werden an der ausgestellten Maschine über einzelne steuerbare Kettbäume zugeführt, wodurch die Herstellung der Struktur erst ermöglicht wird. Mithilfe der Servosteuerung des Abzugsmotors der Webmaschine kann die Gewebedichte unter anderem durch die Veränderung der Abzugsgeschwindigkeit und des Abzugszeitpunktes bei konstant laufender Webmaschine beeinflusst werden. Die Kettfadenspannung wird bei dieser Maschine über ein tänzerwalzenindiziertes Kettablasssystem realisiert. Mit diesem System ist es möglich die Kettfadenzugkraft innerhalb des Webprozesses relativ konstant zu halten. Die Tänzerwalze belastet den Kettfaden direkt mit einer Federspannung, während der Auslenkwinkel und die Auslenkrichtung des Tänzersystems über einen Näherungssensor die Drehgeschwindigkeit sowie die Drehrichtung der Kettablassmotoren bestimmt. Aus der Kombination dieser beiden Kräfte ergibt sich die reale Kettfadenzugkraft. Dieser Tänzer ist individuell einstellbar. Eine andere Möglichkeit der Kettfadenüberwachung bzw. -steuerung ist ein Servomotor.
Die zweite ausgestellte Webmaschine, die den Studierenden des ITM vorgestellt wurde, war eine Bandwebmaschine, die einen Single-Tube, also einen Schlauch, der sich in zwei Schläuche verzweigt erzeugt. Dieser kann zum Beispiel in der Medizintechnik als Aterienersatz genutzt werden und wird im Anwendungsfall an das organische Material angenäht. Bei dieser Maschine sind drei Spulenschützen im Einsatz, die drei Schussebenen bilden. Ein Schützen ist für den Single-Tube zuständig, die anderen beiden Spulenschützen für die Verzweigung des Schlauches, die den Schlitz bildet. Die Bandwebmaschine kann mit einer Geschwindigkeit von bis zu 250 Schuss pro Minute laufen. Praktisch wird es jedoch nicht genutzt, da das feine Fadenmaterial solch hohen Belastungen nicht standhalten kann. In dem uns gezeigten Fall lief sie deswegen mit 150 Schuss pro Minute. Die Fertigungsgeschwindigkeit verringert sich automatisch auf 120 Schuss pro Minute, sobald der Schlitz gefertigt wird, damit die Kettfadenzugkraft so konstant wie möglich bleibt und ein gleichmäßiger Abzug mit 20 Schuss pro Zentimeter erfolgen kann. Da das Endprodukt sehr zuverlässig und reproduzierbar gefertigt werden muss, ist das Halten der Kettfadenzugkraft besonders wichtig. Die Maschine besitzt eine Steuerung der Kettfadenzugkraft von Schuss zu Schuss, sodass der Single-Tube fehlerfrei gefertigt werden kann. Dieser Kontrollmechanismus besteht aus einer Walze, die mit Kraftmessdosen verbunden wird. So kann der Kettfadenzugkraftverlauf während des Webvorganges nachvollzogen und bedarfsgerecht nachgestellt werden. Diese Schaltung wird mithilfe einer SPS realisiert, die permanent einen Soll-Ist-Vergleich durchführt. Aufgrund der Schwankungen, die sich im Bereich von 0,5 N befinden, bewegt sich die Walze vor und zurück.
Durch den Besuch des Messestandes der Firma MAGEBA hat sich der Wissensstand der Studierenden bezüglich des Webprozesses, der damit verbundenen Möglichkeiten sowie der steuerungstechnischen Voraussetzungen um ein Vielfaches erweitert. Es ist sehr aufschlussreich die Maschinen laufen zu sehen und einen Fachmann zur Verfügung zu haben, der alle Fragen, die auftreten beantworten kann. Der Besuch hat in jedem Fall unser Interesse an der Firma MAGEBA geweckt und wir verfolgen mit großem Interesse und großer Neugier weitere Entwicklungen und Innovationen des Unternehmens.
Wir danken der Firma MAGEBA und vor allem Herrn Roth für die Möglichkeit eines geführten Besuches auf dem Stand und für die vielen tieferen Einblicke in den Maschinenbau am Beispiel der Schützenwebtechnik.
Besuch der KARL MAYER Textilmaschinenfabrik GmbH
Der Besuch der Entwicklungs- und Produktionsstätte der Firma KARL MAYER in Obertshausen fand am 11.05.2107 statt. Anfangs begrüßten uns die KARL MAYER -Mitarbeiter bei einem kleinen Frühstücksbuffet und stellten uns das Firmenprofil sowie das Produktportfolio dar. Besonders interessant für Studierende ist das Angebot ein Fachpraktikum sowie weitere wissenschaftliche Arbeiten bei KARL MAYER durchzuführen. Anschließend folgte eine Rundführung über das Firmengelände.
KARL MAYER wurde 1937 gegründet und zeichnet sich daher dieses Jahr durch 80 Jahre erfolgreiche Unternehmensgeschichte aus. Die von der Firma KARL MAYER produzierten hochwertigen Textilmaschinen werden weltweit nach Bedarf kundenspezifisch gefertigt. KARL MAYER ist Weltmarktführer in den Bereichen Wirkerei und Technische Textilien. Die Entwicklung und Fertigung der hochpräzisen Textilmaschinen wie Wirkmaschinen und Multiaxial-Kettenwirkmaschinen findet in Deutschland an den Standorten Obertshausen, Chemnitz und Naila statt. Seit 1956 ist Karl Mayer auch weltweit durch Service-Niederlassungen vertreten.
Entsprechend vielseitig ist die Bandbreite der Produkte, die von Kunden auf KARL MAYER -Maschinen produziert werden können: von Natur- bis Synthesefasern, von herkömmlicher Bekleidungstechnik bis hin zu individuellen Geotextilien aus Hochleistungsfasern und medizinischen Textilien. Beispielhaft wurden Produkte vorgestellt, die mit Hilfe von KARL MAYER -Maschinen hergestellt werden. Besonders erwähnenswert sind dabei Abstandsgewirke, die zunehmend in Sportschuhen, Matratzen oder Rucksäcken Verwendung finden. Auch das Zukunftsprodukt der Bauindustrie, der mehrfach prämierte Textilbeton, wird durch Biaxialgelegestrukturen realisiert.
Bei standardisierter Umgebungstemperatur werden die Maschinen seit Januar 2017 in Fließbandarbeit gefertigt. Um thermischen Verzug während der Montage vorzubeugen, werden die Maschinen mit Öl auf eine bestimmte Temperatur erwärmt und konstant gehalten. Dies ist vor allem bei den hohen Maschinenfeinheiten dringend erforderlich. Eine Modularisierung der Arbeitsschritte gewährleistet einen kontinuierlichen Arbeitsprozess. Die Zerlegung der komplizierten Gesamtmontage in einfache Schritte ermöglicht es, die „Anlernphase“ der Arbeiterinnen und Arbeiter auf ein Minimum zu verkürzen und die Auswirkungen beispielsweise krankheitsbedingter Ausfälle zu verringern. So dauert der Montageprozess für eine Maschine i.d.R. zwischen 10 und 14 Tagen. Dabei ist einzig das Ausrichten der Wirkelemente, insbesondere der Lochnadeln, eine Aufgabe, die nur einigen wenigen Arbeitern mit besonders langer Erfahrung vorbehalten ist.
In Obertshausen werden hauptsächlich Kettenwirkmaschinen hergestellt, mit denen eine enorme Variationsmöglichkeit zur Herstellung von gewirkten Maschenwaren umsetzbar ist. Die textilen Erzeugnisse können 0,3 mm dünn bis 60 mm dick sein und zeichnen sich mit einer hohen Reißfestigkeit von bis zu 100 t Tragfähigkeit aus. Je nach Anwendungsbereich schwankt das Flächengewicht der Gewirke zwischen 4 g/m² und 10 kg/m².
Die entwickelten Kettenwirkmaschinen haben eine Maschinenfeinheit von bis zu E50. Das bedeutet, dass auf einem englischen Zoll (25,4 mm) 50 Nadeln angeordnet sind. Eine Maschine kann mit bis zu 100 Legebarren arbeiten, wobei bereits mit drei Legebarren bis zu 40 Millionen unterschiedliche Muster hergestellt werden können.
Insbesondere blieb die Vorführung einer Maschine zur Herstellung von Kartoffelsäcken und einer vorgelagerten Folienzuschnitt-Maschine nachhaltig in Erinnerung. Dabei werden die typisch orangenen Monofile aus Folienballen zurechtgeschnitten und im weiteren Arbeitsprozess verwirkt. Es ist bei der Verarbeitung von Kunststofffilamente besonders bei relativ hoher Luftfeuchtigkeit auf die elektrostatische Aufladung zu achten. Aufgrund dessen müssen die Arbeitsmaschinen geerdet werden.
Nach einer letzten Fragerunde, der Verabschiedung und einem Gruppenfoto trat die Gruppe des ITM den Rückweg zur Messe Frankfurt an.
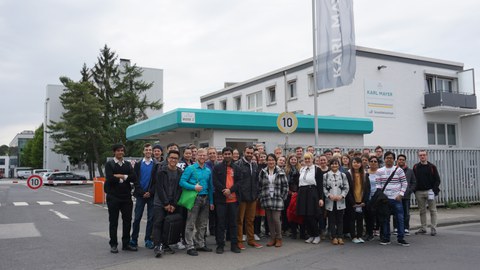
Studentengruppe vor dem Firmenstandort der Firma KARL MAYER in Obertshausen
Wir danken der Firma KARL MAYER und vor allem Herrn Jung für die Möglichkeit eines geführten Besuches im Werksgelände in Obertshausen und für den damit verbundenen sehr interessanten Einblick in die Welt eines großen Textilmaschinenbauers.
Besuch des VDMA Textile Care, Fabric and Leather Technologies
Am dritten Tag der Exkursion wurden wir am Nachmittag zu einem Vortrag des VDMA Textile Care, Fabric and Leather Technologies eingeladen.
Der VDMA Textile Care, Fabric and Leather Technologies ist ideeller Partner der Texpocess sowie der Messe Texcare.
Empfangen wurden wir in einem Konferenzraum auf der Messe von Herrn Elgar Straub, Geschäftsführer des VDMA Textile Care, Fabric and Leather Technologies, Frau Veronika März, Frau Rita Neumann und einem reichhaltigen Buffet an Snacks, Getränken und Kaffee.
Herr Straub gab uns einen Gesamtüberblick zu seinem Bereich und dem Verband allgemein. Der Verband finanziert sich ausschließlich über Mitgliedsbeiträge und berät sowie unterstützt die Mitglieder beim Netzwerken in der Branche und branchenübergreifend. Zum Bereich Textile Care, Fabric and Leather Technologies zählen Maschinen aus dem Bereich Näh-und Bekleidungstechnik, Schuh- und Ledertechnik sowie Wäscherei- und Textilreinigungstechnik. Da Industrie 4.0 das Thema der Zeit ist, hat der VDMA Textile Care, Fabric and Leather Technologies ein Leitprojekt ins Leben gerufen, welches sich mit folgenden Inhalten beschäftigt:
- Gründung einer Task Force
- Strategische Ausrichtung der Bekleidungsbranche, Schuh/Lederbranche, Branche Verarbeitung Technischer Textilien zu diesem Thema
- Positionsbestimmung
- Entwicklung Projektskizze
- Leitprojekt
Passend dazu ist auch der Leitspruch des VDMA Textile Care, Fabric and Leather Technologies für die Texprocess: „Individualisierung treibt“.
Die Vortragende Veronika März, verantwortlich für Marketing und Messen, gab uns einen Überblick über den Aufbau und die Arbeit des VDMA. Wesentliches daraus wird im Folgenden zusammengefasst.
Der VDMA als führender Wirtschaftsverband des europäischen Maschinen- und Anlagenbaus gliedert sich in 37 verschiedene Fachverbände, 11 Querschnittsabteilungen und 6 Landesverbände. Als Experten für Produktspezifische Themen unterstützt der VDMA seine hauptsächlich kleinen und mittelständischen Mitgliedsunternehmen in Fachfragen, Rechtsberatung, verschiedenen Foren und organisiert ein Netzwerk als Kommunikationsplattform für die Mitglieder. Darüber hinaus steht der VDMA aber auch immer im Dialog mit Kundenbranchen, Partnerverbänden, Forschungseinrichtungen und Hochschulen.
Der Fachverband Textile Care, Fabric and Leather Technologies, aus dem die Vortragenden kommen, bietet seinen Mitgliedern unter anderem die Mitarbeit in folgenden Arbeitskreisen an: Auslandsmarketing, Technik-Entwicklung-Konstruktion, Verarbeitung Technischer Textilien und Technik-Wäscherei-Textilreinigung. Im Bereich Auslandsmarketing sind u. a. neue Märkte ein Thema für den Verband. Wenn bei den Mitgliedern Informationsbedarf zu einem neuen Markt besteht werden über den VDMA für die Mitglieder z. B. Weiterbildungen in Form von Unternehmerreisen angeboten.
Zudem gestaltet der Fachverband im Rahmen der beiden Leitmessen Pressekonferenzen, mit Informationen, über die Branche. Auf wichtigen Branchenmessen weltweit bietet der Fachverband Mitgliedsunternehmen Plätze auf Gemeinschaftsständen an. Er betreut zudem die Bundesbeteiligungen auf Auslandsmessen und betreibt Messemonitoring im In- und Ausland.
Zur Information der Mitglieder führt der Verband Analysen und Prognosen der Branchenmärkte weltweit durch und informiert in Branchen- (monatlich) und Kundenbranchennewslettern (zweiwöchentlich). Für die Automotive-Branche gibt es zusätzlich noch die wöchentlichen Autonews.
Ihren Vortrag schloss Veronika März mit den Branchentrends der Texprocess. Diese sind für 2017:
- Individualisierung
- Digitalisierung der gesamten Wertschöpfungskette
- Digital Printing
- Funktionstextilien/Smart Textiles – neue Herausforderungen in der Produktion
- Verlagerung der Produktion
- Nachhaltige Produktion von nachhaltigen Produkten
Im zweiten Teil des Vortrags referierte Rita Neumann, verantwortlich im Bereich Technik, Umwelt Forschung und Normung.
In dem besonders wichtigen Bereich Technik und Umwelt stehen z. B. die Themen Produktsicherheit und -haftung, Maschinenrichtlinie, Funkanlagenrichtlinie, produktbezogene Umweltanforderungen, EMV, Stoffverbote, Chemikalien, Recycling, Energieeffizienz, technische und umweltbezogene Marktzugangsanforderungen (EU und NON EU) und auch die Begleitung von relevanten Forschungsprojekten im Mittelpunkt. Der Verband ist Plattformgeber bei der Interessenvertretung, wie beispielsweise der Europäischen Umweltgesetzgebung. Über die Europäische Arbeitsgemeinschaft ETCT „European Textile Care Technology“ haben sich europäische Hersteller von industriellen Wäschereianlagen zusammengeschlossen um die Gesetzgebung zu europäischen Umweltrichtlinien aktiv zu begleiten
Neben diesen Themen, von ist der Verband zusätzlich im Bereich der Normungsarbeit tätig. Frau Neumann hält zwei internationale Sekretariate im Bereich Industrienähmaschinen und Industrielle Wäschereianlagen. Dabei stehen auch hier Normen über Produktsicherheit und produktspezifische Umweltanforderungen im Vordergrund.
Wir danken recht herzlich dem VDMA und den genannten Personen für die ausgezeichnete Betreuung sowie die Vorstellung des VDMA und der mit dem VDMA verbundenen Möglichkeiten für Studierende und auch für die sehr informative „Standparty“.
Besuch der Brother Internationale Industriemaschinen GmbH
Der weltweit agierende Konzern Brother Industries Ltd., zeigte auf der Texprocess sein breit aufgestelltes Angebot an Stick- und Nähsystemen sowie Textildruckern. Die 1908 gegründete Firma entwickelte sich zu einer der weltführenden Hersteller auf diesem Gebiet, wobei die Industrie-Nähmaschinen und Textildrucker von einer Tochterfirma in Deutschland vertrieben werden.
Der Messestand des Unternehmens bot einen Überblick zur aktuellen Produktvielfalt, sowie den neuesten Stand der Technik. Neben innovativen Nähmaschinen und Textildruckern wurde eine umfangreiche Produktionslinie für Jeanszuschnitte präsentiert.
Die Hauptleitmotive der Messe waren auch in der Produktpalette der Firma Brother eindeutig erkennbar. Durch Digitalisierung des gesamten Produktionsprozesses vergrößern sich die Möglichkeiten zur Produktindividualisierung. Dies ermöglicht ein variables Lösungsangebot für Kundenwünsche. Die Kontrolle und Überwachung der ablaufenden Prozesse jeder Näh- und Stickmaschine wird durch eine Computerunterstützung sichergestellt. Zudem lässt sich durch frei programmierbare Abläufe und diverse Programme eine sehr hohe Auftrags- und Kundenorientierung erreichen.
Eines der Standhighlights war der Textildrucker, welcher in wenigen Minuten T-Shirts, Mützen, Schuhe, Handtücher, Taschen und Kissen mit Wunschmotiv direkt vor Ort bedruckt hat. Dieser Drucker bringt die Farben direkt auf die Fasern auf und garantiert somit einen klaren Farbauftrag und verhindert ein Verwaschen des Motivs. Individuelle Kundenwünsche können somit schnell umgesetzt werden. Ebenfalls möglich sind verschiedene Formate, durch eine unkomplizierte Umrüstung der Maschine.
Eindrucksvoll waren auch die drei größeren Flächenstickmaschinen. Auf der ersten Maschine wurde die Herstellung von Airbags für die Automobilbranche vorgeführt. Die Zweite nähte zwei verschiedene, rechteckige Faserverbundwerkstoffe und richtete dabei mittels Kamera die Werkstücke perfekt zueinander aus. Auf dem dritten Ausstellungsstück wurde gezeigt, wie automatisch Kanten auf der Fläche erkannt und passgenau vernäht wurden. Insgesamt lässt sich an diesen Maschinenbeispielen gut erkennen, wie intelligente Maschinenlösungen eine effiziente und exakte Verarbeitung ermöglichen. Aus dem hohen Anspruch an Qualität und Genauigkeit resultiert die führende Position und Innovation von Brother.
Ein weiterer Bereich des Standes bezog sich auf eine Kooperation mit der italienischen Firma SIP-Italy, die zusammen Technologien und Maschinen zur effizienten Produktion von Jeans entwickelt haben. Damit können umweltschonend und kosteneffizient Jeanszuschnitte gefertigt werden. Teile der Produktionslinie, wie zum Beispiel das Annähen des Bundes oder der Gürtellaschen, oder auch das Aufbringen der Innennaht, wurden direkt am Stand vorgeführt.
Wir danken recht herzlich der Firma Brother und speziell Herrn Finke für die ausgezeichnete Betreuung sowie die Vorstellung der Firma.
Die Studierenden des ITM bedanken sich bei dem ITM für die Organisation dieser Exkursion. Sie und das ITM selbst bedanken sich bei dem Freundes- und Förderkreis des ITM, bei der Fakultät Maschinenwesen der TU Dresden, sowie bei den VDMA Fachverbänden Textilmaschinen und Textile Care, Fabric and Leather Technologies für die fachliche und finanzielle Unterstützung der Exkursion.
Gesamtbericht zur Studentenexkursion 2017 (verfasst von den Studierenden des ITM der TU Dresden)