Studentenexkursion 2018
Table of contents
Zur jährlichen Studentenexkursion besuchten vom 22. bis 25. Mai 2018 31 Studierende des ITM aus den Studiengängen VTMB (Diplom-Studiengang Maschinenbau mit der Vertiefung Verarbeitungs- und Textilmaschinenbau), MaTK (Masterstudiengang Textil- und Konfektionstechnik), WING (Wirtschaftsingenieurstudiengang mit der Vertiefung Textiltechnologie) mit den Exkursionsleitern Frau Dr. Iris Kruppke und Herrn Dipl.-Ing. Martin Kern folgende renommierte Textilmaschinenhersteller, Textilhersteller sowie ein Forschungszentrum:
- Otto Bock HealthCare GmbH / Duderstadt,
- Trützschler GmbH & Co. KG Textilmaschinenfabrik / Mönchengladbach,
- Textechno Herbert Stein GmbH & Co. KG / Mönchengladbach,
- A. Monforts Textilmaschinen GmbH & Co. KG / Mönchengladbach,
- Schlafhorst, Zweigniederlassung der Saurer Germany GmbH & Co. KG / Übach Palingen und
- Deutsches Zentrum für Luft- und Raumfahrt / Braunschweig.
Die Studierenden des ITM bedanken sich bei dem ITM für die Organisation dieser Exkursion. Sie und das ITM selbst bedanken sich ebenfalls bei dem Freundes- und Förderkreis des ITM, bei der Fakultät Maschinenwesen der TU Dresden, sowie bei dem VDMA Fachverband Textilmaschinen für die fachliche und finanzielle Unterstützung der Exkursion.
Besuch der Otto Bock Healthcare SE & Co. KGaA
Die diesjährige Pfingstexkursion des ITM begann am 22. Mai 2018 in Duderstadt im Eichsfeld mit dem mittelständischen Unternehmen Otto Bock HealthCare SE & Co. KGaA (nachfolgend Otto Bock HealthCare genannt). Otto Bock HealthCare blickt mit seiner Gründung im Jahr 1919 auf eine bald hundertjährige Firmengeschichte zurück. Die Versehrten des 1. Weltkrieges erzeugten die Notwendigkeit einer schnellen und großflächigen Versorgung mit Prothesen. Durch den Firmengründer Otto Bock wurde die Passteilfertigung in der Firma eingeführt und so der erste Meilenstein der Firma gesetzt. Durch diesen Meilenstein sicherte sich Otto Bock HealthCare schon früh die Weltmarktführerposition im Bereich der Prothetik, da die Passteilfertigung ab den 60er Jahren als Standard gilt. Der Hauptsitz lag zur Zeit des Begründers in Königsee in Thüringen. Die zweite Ära der Firma, welche 1946 begann, wurde durch den Schwiegersohn Max Näder geprägt. Nach der Teilung Deutschlands wurde der Firmenhauptsitz in Duderstadt, Niedersachsen, angesiedelt, um zum Einen einer Enteignung der Firma sowie der Gründerfamilie in der sowjetischen Besatzungszone zu entgehen und zum Anderen die geografisch günstige Lage Duderstadts für den Interzonenhandel zu nutzen. Max Näder führte die Verarbeitung von Leichtmetallen und Schaumstoffen bei den Prothesenpassteilen ein. Im Gegensatz dazu wurden in der Zeit von Otto Bock Prothesen aus Holz gefertigt. In den 1960er Jahren setzte Otto Bock HealthCare einen weiteren Meilenstein mit der Entwicklung von myoelektrischen Armprothesen, bei denen schwache elektrische Spannungen, die im Muskel bei einer Kontraktion entstehen, auf der Hautoberfläche von Elektroden erfasst werden und von einem Prozessor in der Prothese zu Steuerungssignalen verarbeitet werden. 1990 übernahm Hans Georg Näder die Geschäftsführung, welcher für die Ära der Mikroprozessortechnik und Elektronik, sowie für die Internationalisierung des Unternehmens mit Auslandsgesellschaften in mehr als 50 Ländern steht. 1997 brachte Ottobock mit dem C-Leg die erste mikroprozessorgesteuerte Beinprothese auf den Markt und setzte somit einen weiteren Meilenstein in der Firmengeschichte.
Für die Betriebsführung bei Otto Bock HealthCare wurden wir von Herrn Goebel und Herrn Schuh empfangen. Im Showroom bekamen wir neben dem Einblick in die Unternehmensgeschichte einen Eindruck zu den aktuellen Produkten. Vornehmlich stellt Otto Bock HealthCare Prothesen mit einer ausgeklügelten Mechanik und Mikroprozessorsteuerung her. Dabei liegt der Schwerpunkt neben Arm- und Handprothesen auf Beinprothesen. Auch Orthesen und Rollstühle sind im Produktspektrum zu finden.
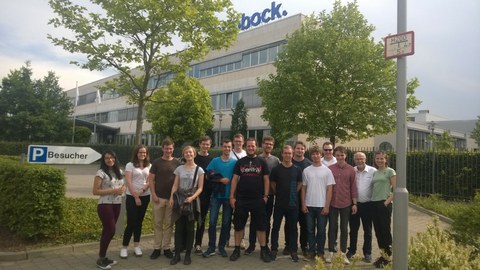
Studentengruppe des ITM vor dem Firmensitz der Firma Otto Bock HealthCare
Einige der Raffinessen - vor allem an den Beinprothesen - wurden uns im Showroom an Demonstratoren präsentiert. Diese wurden für spezielle Einsatzsituationen präpariert und zeigen die Möglichkeiten von Hightechprothesen auf. Die Herausforderungen und Anforderungen bei der Entwicklung der Prothesen bestehen darin, einen möglichst natürlichen Bewegungsablauf nachzuahmen. Dazu gehört auch das Vermeiden von Stolpern mit Hilfe von Sensorik, die mit Mikroprozessoren innerhalb der Prothese verarbeitet werden und in Ausgleichsbewegungen umgesetzt werden. Die Produkte werden in Mobilitätsklassen eingeordnet und werden je nach Bedarf des Kunden modular angepasst. Für alle Produkte gilt aber, dass sie wasserdicht sein sollten und mit einem Notlauf ausgestattet sind. Modularität spielt eine große Rolle, da Prothesen auch schon bei Kindern eingesetzt werden und entsprechend deren Wachstum anpassbar sein müssen.
Der Aufbau eines prothetischen Beines besteht aus einem Fuß mit einer lasttragenden Komponente und einem kosmetischen Überzug, an dessen Gelenk ein Titanrohr anschließt, auf dem verschiedene Kniegelenksausführungen befestigt werden können. Danach folgt ein weiteres Titanrohr mit dem darauf angebrachten Schaft, der vom Orthopädietechniker an den jeweiligen Patienten angepasst wird.
Lasttragende- und Verkleidungsteile werden manuell hergestellt. Hierzu werden die Prepregs in einem gekühlten Raum mittels CNC Schneidtechnologie zugeschnitten. Zu beachten ist, dass die Prepregs bei -16 °C gelagert werden müssen, um den Vernetzungsprozess des Harzes zu verzögern. Für den Zuschnitt wird ein klassisches Teppichmesser verwendet, da dieses die besten Schneideigenschaften aufweist. Im Anschluss werden die geschnittenen Halbzeuge von den Mitarbeitern per Hand auf eine Form geklebt. Dabei sind das Know-how und das Geschick der Mitarbeiter von immanenter Bedeutung für die Qualität der Bauteile. Im Anschluss werden die komplizierten Freiformflächen, für Schienbeine und Abdeckungen, in einem Konsolidierungslabor mittels Autoclave-Technologie konsolidiert. Das Unternehmen Ottobock setzt nicht nur auf neue Hightech-Materialien. Es wird ein passender Mix aus Man-Made-Fibers und Naturprodukten wie Holz verwendet, so zum Beispiel im Fuß einer Prothese. Für den Fuß wird ein Holzblock hergestellt, wobei dieser aus einem künstlichen Verbund mit einem leichten formgebenden Holz und einer härteren Holzart als Rippenstruktur zur Lastaufnahme besteht. Die Form erhält der Block mittels CNC-Frästechnik. Otto Bock HealthCare stellt einen der wenigen Standorte in Europa dar, in dem Titanfreiformen schmiedbar sind. Dieses Know-how wird zur Reparatur und Herstellung von kleinen Teilen verwendet.
In der Kunststofffertigung werden Strukturbauteile, kosmetische Überzüge, und Schutzliner inhouse gefertigt. Die Fertigungstiefe ist so stark ausgeprägt, dass sogar die Spritzgussformen im Werk in Duderstadt hergestellt werden. Dies ermöglicht es, einen durchgehend hohen Qualitätsstandard zu erhalten, bei gleichzeitiger Maximierung der Flexibilität.
Um die Qualitätsansprüche der Medizinprodukte zu erreichen, setzt Otto Bock HealthCare in der Montage auf qualifizierte Handwerker. Dabei führt jeder Mitarbeiter für sein Produkt die komplette Montage durch und prüft anschließend die Endprodukte selbstständig. Dies geschieht bei Gelenken messtechnisch. Dabei werden Körper-, Luftschall und wirkende Momente erfasst, ausgewertet und deren Ursache bei Bedarf durch Nacharbeitung abgestellt. Somit finden nur einwandfreie Prothesen den Weg zum Endkunden.
Im Inneren der gefertigten Pro- und Orthesen verstecken sich allerdings nicht nur Vorrichtungen zur mechanischen Bewegung der Glieder, sondern auch die Ergebnisse vieler anderer Disziplinen wie Mechanismentechnik, Mechatronik, Elektronik, Informatik und schließlich technisch-optisches Design. Doch auch abseits des technischen Metiers zeigen sich Hans Georg Näder und die Otto Bock Health Care SE & Co. KGaA engagiert. Während einer kurzen Stadtführung in Duderstadt stießen wir an mehreren Stellen auf geförderte soziale oder kulturelle Einrichtungen.
Wir danken der Firma Otto Bock HealthCare für die Möglichkeit des geführten Besuches am Standort Duderstadt und für die vielen tieferen Einblicke in den sehr umfangreichen Prothesenbau.
Besuch der Truetzschler – it’s true!
Am 23. Mai besuchten die Studenten des ITM den Konzern Trützschler GmbH & Co. KG (nachfolgend Trützschler genannt). Die als Familienunternehmen geführte Textilmaschinenbaufirma beschäftigt sich mit Maschinen für die Spinnereivorbereitung. Ansässig in Mönchengladbach liegt der Ursprung in der Faserreinigung. Im Laufe der Zeit hat das Unternehmen weitere Bereiche erschlossen und baut nun Ballenöffner, Reiniger, Karden, Krempel und jüngst auch Kämmmaschinen.
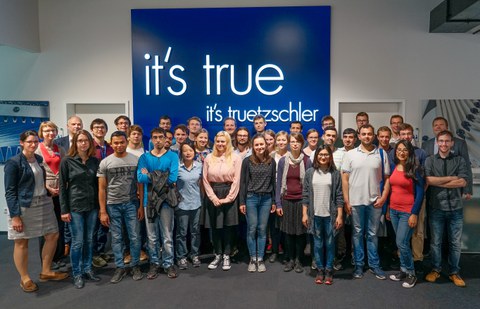
Studentengruppe des ITM bei der Firma Trützschler in Mönchengladbach
Das Unternehmen ist in vier Geschäftsbereiche gegliedert:
- Card Clothing,
- Nonwovens,
- Manmade-Fibres und
- Spinning (Standort Mönchengladbach).
Eine Besonderheit des Unternehmens ist, dass es viele Komponenten selbst entwickelt und produziert. Beispielsweise stellt Trützschler die Steuerungen für ihre hochspezialisierte Maschinentechnik selbst her. Damit wird auf den Einsatz teurer Basislösungen von Steuerungsherstellern verzichtet, und so Kosten eingespart. Ein weiterer Vorteil ist die Aneignung von Technologiewissen und die volle Kontrolle über den Prozess. Außerdem kann somit das Kopieren erschwert werden, indem die Steuerungen durch das proprietäre Verfahren nicht ohne Weiteres auslesbar sind.
In den letzten Jahren hat sich der Markt, in dem Trützschler aktiv ist, deutlich verändert; mehr als die Hälfte der Anteile haben sich von Amerika und Eurasien nach Asien verlagert. Dabei hat sich durch die steigende Produktivität der Maschinen die Nachfrage verringert, sodass ein Verdrängungswettbewerb z. B. in der Kardenindustrie stattfindet, obwohl die Branche stetig wächst.
Trützschler hat deswegen seine Produktion in den letzten Jahrzehnten zu weiten Teilen globalisiert. Unter anderem liege das daran, dass seit der letzten Wirtschaftskrise fast alle europäischen, sämtliche japanische und alle amerikanischen Konkurrenten ausgeschieden seien. Trützschler konnte seine Marktanteile durch seine Strategie, seine Maschinen in den treibenden Ländern des asiatischen Raumes zu produzieren, stabilisieren und teilweise sogar ausbauen.
Der Firmenbesuch wurde von zwei Vorträgen eingeleitet. Zuerst stellte die Marketingabteilung die Unternehmensgeschichte, -philosophie und die Marktentwicklung vor. Der zweite Vortrag war speziell auf uns Studenten abgestimmt und lieferte einen Überblick über die Arbeitsbereiche, die für Textilingenieure interessant sein könnten. Mit ein paar Tipps zur Bewerbung wurde der erste Teil abgerundet. Danach gingen wir zum Fertigungsrundgang über.
Trotz der geringen Auftragslage im europäischen Raum, ist der Fertigungsstandort in Mönchengladbach vergleichsweise groß. Damit wird sichergestellt, dass die hochtechnischen Schlüsselkomponenten den hohen Anforderungen der Kunden von Trützschler gerecht werden. Die von uns besuchten Fertigungsabteilungen waren:
- Steuerungseinheitenproduktion
- Blechbearbeitung
- Komponentenmontage
- Maschinenmontage
Für uns überraschend war der Teil der Eigenfertigungen enorm umfangreich, was zwar Teils dem Schutz des Knowhows aber auch zu großen Teilen aus Kostengründen und großen Anforderungen an Fertigungsgenauigkeit geschuldet ist. Trützschler verfolgt ein Konzept, bei dem jede Sparte von mindestens zwei Standorten bedient wird, um Engpässe ausgleichen zu können. Im Technikum konnten wir anhand von präparierten Maschinenmodellen die Wirkprinzipien der jeweiligen Maschinentechniken nachvollziehen. Zum Abschluss wurden wir großzügig in der Kantine verköstigt. Dabei konnten wir uns mit den Mitarbeitern unterhalten und erhielten wertvolle Einblicke in das Unternehmen Trützschler.
Wir danken der Firma Trützschler für die Möglichkeit des geführten Besuches am Standort Mönchengladbach und für die vielen tieferen Einblicke in den sehr umfangreichen Textilmaschinenbau. Darüber hinaus bedanken wir uns auch für die sehr hilfreichen Tipps, die uns bezüglich einer erfolgreichen Bewerbung gegeben wurden.
Besuch der Textechno H. Stein GmbH & Co. KG.
Am 23. Mai 2018 besuchten wir die Firma Textechno H. Stein GmbH & Co. KG (nachfolgend Textechno genannt). Die Firma wurde im Jahr 1949 von Herbert Stein ins Leben gerufen. Diese Firma setzt sich hauptsächlich mit der Herstellung von Textilprüfanlagen auseinander.
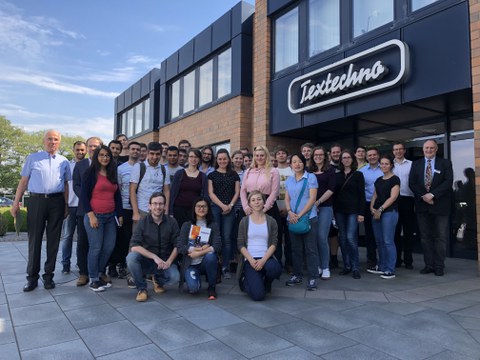
Studenten des ITM am Standort der Firma Textechno
Nach einer kurzen Präsentation von Herrn Dr. Stefan Fliescher (stellvertretender Geschäftsführer) begann der Besuch in vier Gruppen. Auch der Beiratsvorsitzende und ehemalige Geschäftsführer der Firma, Herr Dr. Wolfgang Stein, hatte sich für den Besuch der Studenten des ITM die Zeit genommen, um Gemeinsamkeiten und gemeinsame Entwicklungen von Textechno und ITM zu beleuchten. Auf dem Rundgang wurde zunächst der Gerätetyp FAVIMAT+ vorgestellt. Dieses Prüfgerät wird für verschiedene Anwendungen einschließlich Zugprüfungen, Kräuselungs- und Restkräuselungsbemessung an der Einzelfaser verwendet. Durch das Vibroskop-Verfahren kann zudem die Faserfeinheit bestimmt werden. Im Anschluss wurde der STATIMAT DS angeschaut, der für Messungen an allen Arten von Garn eingesetzt wird. Dieses Gerät verfügt über konstruktive Besonderheiten, wodurch Garneigenschaften wie Feinheit, Festigkeit und Ungleichmäßigkeit automatisch im gleichen Gerät gemessen werden können. Zur Prüfung von Composites und Technischen Textilien gibt es die Möglichkeit, weitere Prüfmaschinen, wie den ROVINGTEST, zu verwenden.
Danach wurde die Kombination von zwei Prüfgeräten, FIMABOND und FAVIMAT+, vorgestellt. Diese können zur Bestimmung der Haftung eingebetteter einzelner Fasern in Matrizen in Anspruch genommen werden. Wie eine Vorspannungsklemme mit einem Gewicht von 10 Milligramm manuell per Hand hergestellt wird, war das Nächste, was die Studenten erfuhren. Das letzte Gerät war der DRAPETEST, das mittels einer Kamera die Drapierfähigkeit von Textilflächen bestimmen kann.
Während unseres Rundganges fiel uns die Anzahl an Neuentwicklungen auf. Diese große Anzahl und das Bestreben des Unternehmens alle Bestandteile der Maschinen selbst herzustellen sind für uns Studenten interessante Informationen von einem innovativen Maschinenbauunternehmen, in dem Entwicklungskompetenzen, die wir im Studium erlernen, auch praktisch benötigt werden.
Schließlich versammelten sich die Studenten nochmal im Konferenzraum und wurden mit Kaffee und Keksen in einer freundlichen Umgebung bedient.
Wir danken der Firma Textechno für die Möglichkeit des geführten Besuches am Standort Mönchengladbach und für den umfassenden und sehr interessanten Einblick in die vielfältigen Textilprüfanlagen.
Besuch der A. Monforts Textilmaschinen GmbH & Co. KG
Am 24. Mai 2018 besuchten die Studenten der TU Dresden die Firma A. Monforts Textilmaschinen GmbH & Co. KG (nachfolgend Monforts genannt) in Mönchengladbach.
Es ist ein Traditionsunternehmen, das im Jahre 1884 von August Monforts gegründet wurde. Der Firmenhauptsitz befindet sich in Mönchengladbach. Hier sind auch die Kompetenzzentren Konstruktion, Maschinenentwicklung, Ersatzteilservice, Teleservice, Spedition, Rechnungswesen, Einkauf, Marketing und Vertrieb lokalisiert.
Die Firma beschäftigt sich im Bereich Textilmaschinen um die Entwicklung von Textil-Veredelungsmaschinen. Monforts ist heute Mitglied der CHTC Fong‘s Group, einer der größten Textilmaschinenhersteller der Welt.
Die Firma ist in Deutschland (Mönchengladbach), Österreich (Montex in St. Stefan) und in China (Zhongshan) tätig, und deckt einen großen Teil des Weltmarktes ab. Hauptmärkte sind Pakistan, Bangladesh, Indien und Südamerika. Dabei wächst der Bereich Technische Textilien und Beschichtung bei Monforts seit einigen Jahren stark an.
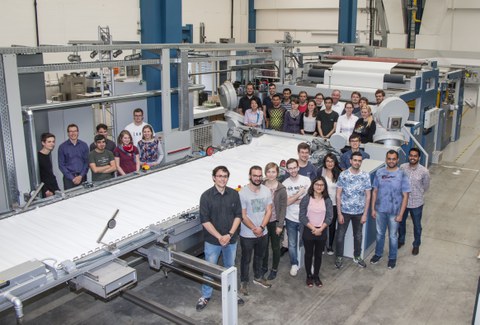
Studentengruppe des ITM bei der Firma Monforts
Ziele der Firma
- Verringerung des Energieverbrauchs ihrer Maschinen
- Verringerung des Einsatzes von Chemikalien
- Zeit- und Kosteneinsparung durch die Entwicklung von Maschinen mit gekürzter Prozesskette
Anwendungsspektrum der Monforts Maschinen
- Heimtextilien
- Technische Textilien
- Denim
- Bekleidungstextilien
- Funktionale Textilien
Beschichtung M/C für Technische Textilien
Nicht nur Technische Textilien, sondern auch beschichtete Textilien stellen große Anforderungen an die Flexibilität der Maschinen der Firma Monforts. Die Firma Monforts bietet innovative Lösungen dafür an. Momentan sind die folgenden Beschichtungs- und Drucksysteme verfügbar.
- Luftrakel-Beschichtung
- Walzenrakel-Beschichtung
- Schaum-Beschichtung
- Walzenauftragssysteme
- Tiefdruck-Verfahren
- Hochdruck-Verfahren (Flexodruck)
- Durchdruck-Verfahren (Siebdruck)
- Druckrakel (Squeegee)
- Magnetwalzen-Antrag, direkt und indirekt
Um eine hohe Qualitätsanforderung zu erfüllen, bietet diese vollautomatisierte Anlage ein homogenes Beschichten der Oberflächen.
Monforts Visualisierung Q800
Zur besseren Visualisierung der Maschinenparameter bietet Monforts ein eigens entwickeltes Steuerungssystem mit Touchscreens für die Kontrolle der Maschinen an. Dieses ermöglicht die Einspeisung der aktuellen Daten der individuellen Maschinen in ein Netzwerk. Somit ist es möglich, jederzeit den aktuellen Maschinenzustand abzurufen, egal ob man Zuhause oder auf der Dienstreise ist.
Den sehr interessanten und informativen Vorträgen folgte das Mittagsessen in entspannter Atmosphäre, bei dem die Studierenden mit allen an der Firmenführung beteiligten Mitarbeitern sowie dem Prokuristen bei einem erfrischenden Getränk und hausgemachten Sandwiches ins Gespräch kommen konnten.
Wir bedanken uns recht herzlich bei der Firma A. Monforts Textilmaschinen GmbH & Co. KG und ihren Mitarbeitern für die sehr interessante und entspannte Führung durch ihr Unternehmen.
Besuch der Schlafhorst Saurer Germany GmbH & Co.KG
Am dritten Tag der Exkursion wurden wir am Nachmittag zur Besichtigung der Firma Saurer Schlafhorst Germany GmbH & Co.KG (nachfolgend Saurer Schlafhorst genannt) eingeladen.
Wir wurden von Herrn René Bucken, dem Leiter der zentralen Funktionen von Saurer Schlafhorst, begrüßt. Nachdem wir in zwei Gruppen aufgeteilt waren, wurden wir durch die riesigen Werkhallen am Standort Übach-Palenberg geführt. Die Firma produziert am Standort verschiedene Maschinen, unter anderem Ringspinnmaschinen (Zinser), Spulmaschinen (Autoconer) und Rotorspinnmaschinen (Autocoro).
Der Ablauf innerhalb der textilen Prozesskette sieht dabei vor, dass zunächst die Ringspinnmaschinen die Streckenbänder zu Garnen spinnen und anschließend die Spulmaschinen die Garne zu Kreuzspulen weiterverarbeiten. Die Rotorspinnmaschinen hingegen sind in der Lage, die Streckenbänder direkt in Spulenform ohne Zwischenstufe mit Maschinendrehzahlen bis zu 200.000 Umdrehungen pro Minute auszuspinnen.
Im Technology Center von Saurer Schlafhorst gibt es drei verschiedene Klimazonen. Eine für die Ausspinnungen an den Ringspinnmaschinen, eine für die Tests an den Spul- und Rotorspinnmaschinen und eine weitere für das Prüflabor, in dem die herstellten Fasern, Garne und Spulen hinsichtlich der erreichten textilphysikalischen Eigenschaften geprüft werden.
Im Montagebereich der Maschinen kann in bis zu drei Schichten gearbeitet werden. Am Tag können mehrere Hundert Spinn- sowie Spuleinheiten produziert werden. Das Knowhow der Firma liegt unter anderem in der Herstellung ihrer eigenen Faden-Führungs-Trommel (FF-Trommel oder Yarn Guide Drum) für die Spulmaschinen. Diese wird im Werk so bearbeitet, dass sie eine höchstmögliche Garn- und Spulenqualität gewährleistet.
Das Unternehmen verfügt über ein vollautomatisiertes Lager (auf Kanban-Basis) um die zahlreichen für die Assemblierung der Maschinen benötigten kleinen und großen Teile systematisch zu lagern.
Nach dem Firmenrundgang wurden wir in einem Konferenzraum empfangen, wo ein reichhaltiges Buffet auf uns gewartet hat, und wo wir eine Präsentation zum Unternehmen Saurer bekommen haben. Die Firma stellte sich dabei mit einem umfassenden Personenkreis aus den Bereichen Marketing, Entwicklung, Technologie sowie HR vor. Allein die Anzahl an Personen zeigte den Studierenden die Bedeutung des Besuchs und sorgte für erstaunte Gesichter.
Wir danken der Firma Saurer Schlafhorst für die Möglichkeit des geführten Besuches am Standort Übach-Palenberg und für die vielen tieferen Einblicke in den sehr umfangreichen Textilmaschinenbau.
Besuch des Deutschen Zentrums für Luft- und Raumfahrt e.V. (DLR)
Am Freitag, den 25. Mai besuchten wir den Standort Braunschweig des Deutschen Zentrums für Luft- und Raumfahrt (DLR). Nach unserer Ankunft begann das Programm mit einem einführenden Vortrag zu der Struktur und den Instituten des DLR in Braunschweig. Das DLR befasst sich mit den Forschungsbereichen Luftfahrt, Raumfahrt, Verkehr, Energie und Sicherheitsfragen in den genannten Bereichen. Das DLR beschäftigt in Braunschweig ca. 1200 Mitarbeiter und wurde 1936 als DFL (Deutsche Forschungsanstalt für Luftfahrt) gegründet.
Im Anschluss an den Einführungsvortrag wurden wir in zwei Gruppen eingeteilt, die im Wechsel das Institut für Aerodynamik und Strömungstechnik und das Institut für Faserverbundleichtbau und Adaptronik besichtigten.
Die Mitarbeiter des Instituts für Aerodynamik und Strömungstechnik, Fabian Lange und Sven Geisbauer, haben in einer Kurzpräsentation ihre Tätigkeitsfelder und aktuelle Forschungsgegenstände beschrieben. Dazu gehört beispielsweise die numerische Simulation der Umströmung von Luftfahrzeugen und Windkraftrotoren. Zur Simulation und Berechnung werden die Hochleistungsrechner, C²A²S²E II und SCART 2 verwendet. Ein weiteres Forschungsfeld ist die akustische Untersuchung von Luftfahrzeugen im Windkanal. Der hierzu verwendete Windkanal ist ein Niedergeschwindigkeitswindkanal der in dieser Art seinesgleichen sucht. Außerdem werden im Auftrag des Instituts Forschungsflüge mit den Testflugzeugen des DLR durchgeführt, wie zum Beispiel der Überziehversuch HINVA, der in Kooperation mit Airbus durchgeführt wurde und bei dem der über 40 Tonnen schwere Airbus A320 des DLR (ATRA) unter Versuchsbedingungen zum Strömungsabriss gebracht wurde. Um uns dies visuell darzustellen, wurden uns zwei Filme gezeigt, einer davon in 3D.
Im Anschluss besuchten wir die Fertigung und das Wickellabor des Instituts für Faserverbundleichtbau und Adaptronik. Die Führungen wurden durchgeführt von Matthias Bock und Philipp Hillmer. In der Fertigung wurden uns ein CNC-Cutter, die Autoklaven zur Textilkonsolidierung sowie die Legung von Verbundteilen gezeigt und erläutert. Anschließend wurden uns im Wickellabor Prototypen und Versuchsobjekte gezeigt, die am DLR entweder nass- oder trockengewickelt wurden. Diese Bauteile waren faserverbundbasierte, rotationssymmetrische Objekte, die über beeindruckende mechanische Eigenschaften verfügen.
Zum Abschluss versammelte sich die Gruppe vor einem alten Kompressorgehäuse für den Windkanal für ein gemeinsames Erinnerungsfoto und machte sich wieder auf den Weg nach Dresden.
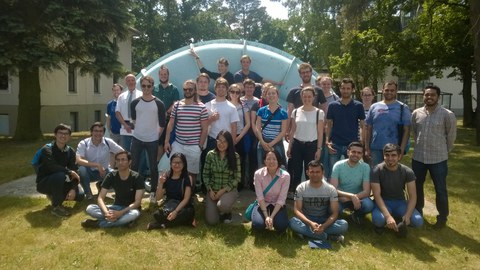
Studentengruppe des ITM auf dem Gelände des DLR in Braunschweig
Wir danken dem DLR für die Möglichkeit des geführten Besuches am Standort Braunschweig und für die vielen tieferen Einblicke in die Zusammenhänge zwischen Textil und Luftfahrt.
(Gesamtbericht verfasst von den teilgenommenen Studierenden des ITM der TU Dresden)