Jul 06, 2022
Carbon reinforced concrete bridge awarded: double honor for the structure by Fédération internationale du béton (fib)
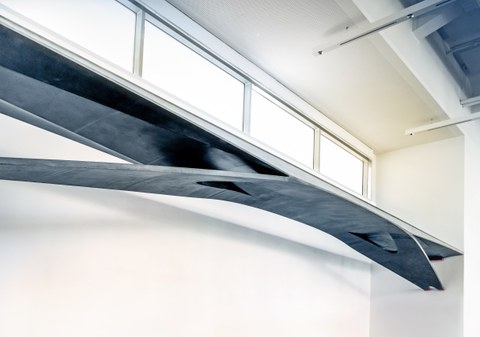
The CarboLight Bridge has taken its place in the bridge and hydraulic engineering department of the Deutsches Museum and presents the advantages of the innovative material combination
Oslo/Dresden: It bears the name CarboLight Bridge and combines slim design and resource conservation. The bridge made of carbon concrete and infra-red lightweight concrete was manufactured and designed especially for the Deutsches Museum by scientists from the Institute of Concrete Structures at the Technische Universität Dresden. The bridge has taken its place in the bridge and hydraulic engineering department of the Deutsches Museum and impressively presents the advantages of the innovative material combination. The fact that this is a very special construction was demonstrated during the fib Congress, which took place in Oslo from June 12 to 16, 2022.

The bridge was awarded the Exceptional Recognition special prize in the "Award for Outstanding Concrete Structures" competition
The renowned conference is considered an important meeting of scientists in the field of concrete research and offers insights into various aspects of construction with concrete. The bridge received two awards: the Exceptional Recognition special prize in the Award for Outstanding Concrete Structures competition and the 2022 Innovation Award in the Structures category for the paper "An ultra-light Carbon Concrete Bridge: From Design to Realisation" by authors Marc Koschemann, Iurii Vakaliuk and Manfred Curbach.
"The construction industry needs to change significantly so that in the future we can build in a way that conserves resources while reducing CO2 emissions. The use of innovative building materials and their combination, as well as the optimization of structures in terms of force flow, are essential components to achieve this goal" - says civil engineer Marc Koschemann, who planned and supervised the construction of the bridge.
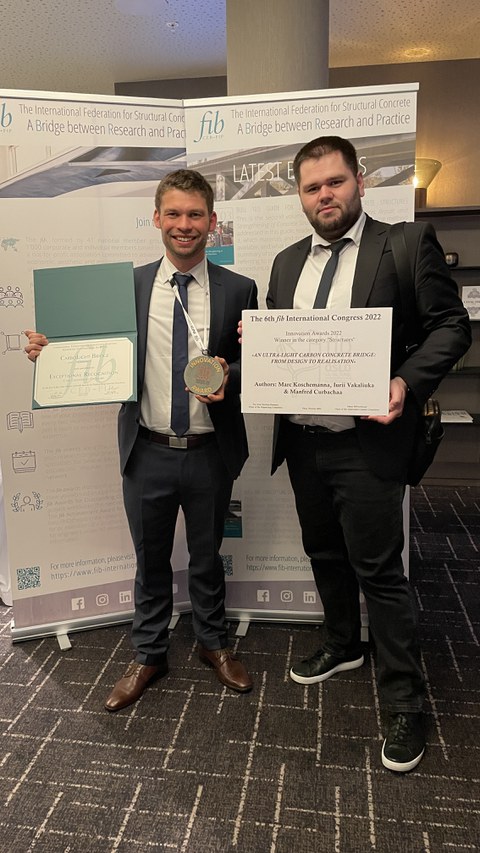
Marc Koschemann and Iurii Vakaliuk proudly presenting the certificates (f.t.l.r.)
The CarboLight Bridge has a length of 9.5 m and was designed as a filigree structure consisting of two slightly inclined V-columns, a three-part superstructure and a design weight of only 2.1 t. The force-flow-optimized shape and sandwich structure of the superstructure play a major role. The biaxially curved underside and the flat top layer are made of carbon concrete, while the layer in between is made of infralight concrete. This allowed material to be saved and weight to be reduced.
Parameterized 3D modeling was used to optimize the geometry in terms of load transfer and design. "By linking the 3D model with a structural analysis program, it was possible to optimize the bridge in terms of material use and load transfer quasi simultaneously. For this purpose, an interface to an FEM software was programmed, which makes it possible to determine the effects of a geometry change on the load transfer quasi simultaneously" - emphasizes the architect and scientist at the Institute of Concrete Structures Iurii Vakaliuk, who is responsible for the 3D modeling. Based on the final 3D model, the formwork was made of milled plywood. In order to test the assembly, appearance and load-bearing capacity of the bridge and its individual segments, a test sample of the bridge was manufactured and tested at the Otto Mohr Laboratory of the TU Dresden.
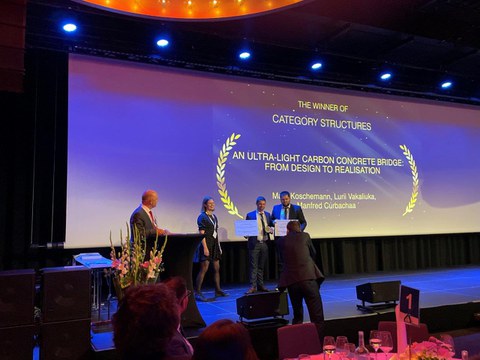
The second prize - the Innovation Award 2022 in the category "Structures" for the paper "An ultra-light Carbon Concrete Bridge: From Design to Realisation" went to the authors Marc Koschemann, Iurii Vakaliuk and Manfred Curbach.
The carbon concrete bridge was created as a demonstrator for Priority Program 1542 "Lightweight Construction with Concrete - Foundations for Building the Future with Bionic and Mathematical Design Principles," which was funded by the German Research Foundation (DFG). The project was also supported by the companies Heidelberger Beton GmbH and HICONFORM - Freitaler Modellwerkstätten eG as well as the Institute for Building Materials of the TU Dresden and the Institute for Concrete Structures of the TU Munich. Special thanks go to the staff of the Deutsches Museum for the exhibition opportunity and on-site support.
The images may be used free of charge for editorial purposes only, provided that the respective credits are given.
Download of the pictures under https://cloud.bauen-neu-denken.de/s/DgmnZEyeiYE6GAL
Your contact person:
Sandra Kranich
E-Mail:
Phone: +49 351 484 567 14