Fully automated quality control system for CRC components
Table of contents
Project data
Titel | Title |
Report in the annual report 2022
Highest Precision required
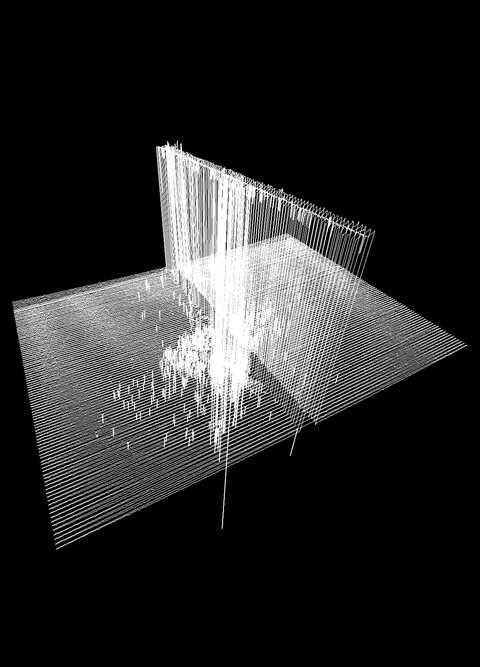
Surface scan of yarns
In concrete construction, terms such as climate neutrality, resource saving, shortage of skilled workers, serial construction and Industry 5.0 are no longer just buzzwords, but driving forces for innovation and progress. In order to meet these new requirements, significant changes are needed in terms of materials, designs and processes. One promising way to meet these challenges is the introduction of carbon-reinforced concrete, an innovative combination of materials that is already demonstrating in construction practice how thin and resource-saving building structures can be.
However, with the reduction in component thickness, the issue of precision is becoming increasingly important. Whereas in the past a 5 mm deviation in the reinforcement layer could still be tolerated in 20 cm thick components, today even minor deviations of 1–2 mm in 3 cm thick components can significantly impair the load-bearing capacity. Technologies must therefore be implemented or developed in concrete construction that enable very high accuracy in the industrial manufacture of mass products.
This is exactly where we come in: Our aim is to drastically reduce quality fluctuations in the production of finished and semi-finished carbon-reinforced concrete parts. By implementing comprehensive, continuous and fully automated process monitoring directly in the concrete plant, we not only want to improve quality, but also significantly increase the economic efficiency and ecology of these processes.
As a result of the initial work, it is now possible to record the exact position of the reinforcement with the help of area scanners. In addition, the type and position of built-in parts can be determined using a photogrammetry system. This means that positional deviations can be documented, analyzed and corrected. As part of extensive tests and analyses, the magnitudes and reasons for positional deviations were determined and the recording systems surface scanner and photogrammetry system were optimized. With the help of these results, the processes are currently being adapted so that the deviations can be reduced to a minimum.
Report in the annual report 2022
Quality of precast CRC elements
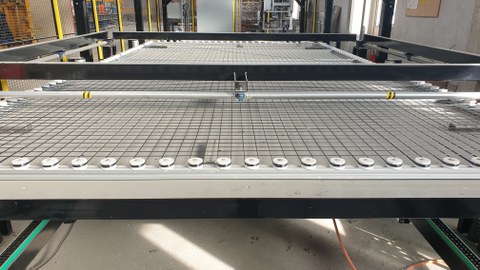
Reinforcement production in the precast concrete plant
Terms such as climate neutrality, resource conservation, shortage of skilled labor but also serial construction and Industry 5.0 are increasingly mentioned in connection with concrete construction. In order to meet the associated requirements, significant changes in materials, designs and processes are needed in some cases. Construction practice is already demonstrating that the new material combination carbon reinforced concrete can be used to create extremely thin and thus resource-saving building structures. However, the thinner components become, the more precisely they have to be manufactured. With 20 cm thick components, for example, 5 mm deviations in the component thickness or the position of the reinforcement are acceptable – but not with 3 cm thick components. Here, deviations of 1–2 mm already have a considerable influence on the load-bearing capacity. The increased demands on accuracy are not placed on a product of a manufactory, but on an industrially produced mass product. However, processes and machines in most precast plants that produce steel reinforced concrete components to date are not suitable for this in all production steps.
The aim of the project is to significantly reduce the quality fluctuations in the production of precast and semi-precast parts made of carbon reinforced concrete by using a holistic, continuous and fully automated process monitoring system directly in the concrete plant. At the same time, economic efficiency and ecology are to be greatly improved. This includes all process steps from formwork and paving installation, carbon reinforcement production, the concreting process, insertion of insulating materials and preparation for transport in a concrete plant following the example of other industries, e.g. the automotive industry. In addition, it should be possible to readjust the processes in the concrete plant in a fully automated manner in the event of deviations occurring.
The tasks of the Institute of Concrete Structures mainly comprise the analysis of the distribution of approval-relevant parameters for the carbon reinforced concrete construction method. It is to be answered in which way different process parameters during the production of reinforcement and concrete components influence the performance of the resulting components. Among other things, findings from component tests of the large-scale research project C3 – Carbon Concrete Composite will be analyzed. Finally, new test components from the project partners will be used to systematically investigate how quality is influenced during the production of reinforcement and carbon reinforced concrete components.