GROSSE STAHLBAU-EXKURSION 2007
Autor: Dr.-Ing. Holger Flederer
Vom 30.05. bis 01.06.2007 fand die diesjährige große Stahlbau-Exkursion statt. Die 44-köpfige Gruppe aus Studierenden des 4. bis 10. Semesters und den Mitarbeitern des Lehrstuhls für Stahlbau startete pünktlich am 30.05. um 8 Uhr zu ihrer Busreise durch Ost- und Norddeutschland. Das erste Exkursionsziel war die Plauen Stahl Technologie GmbH, die wir nach 2-stündiger Fahrt erreichten.
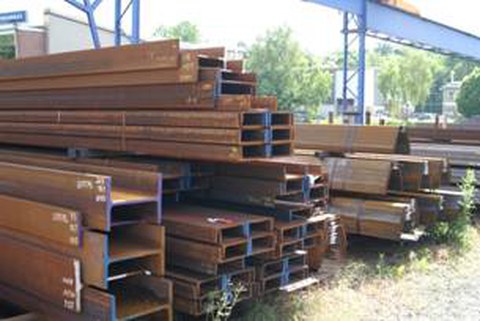
Lagerung
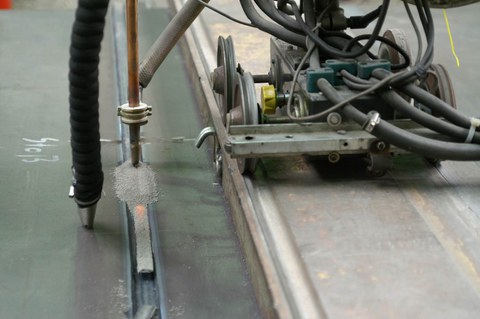
Unterpulverschweißen
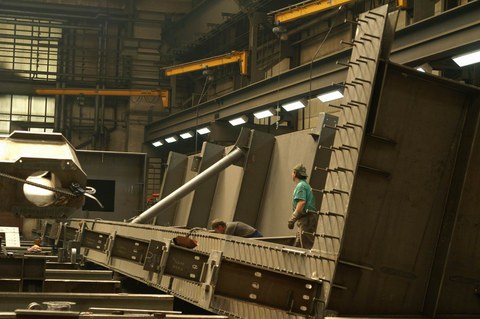
Teil des Überbaus der Schrägseilbrücke Niederwartha
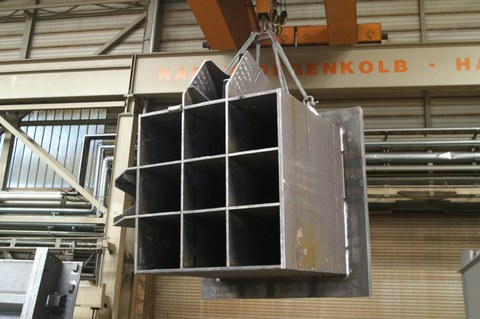
Stützenfuß für das Kraftwerk Boxberg
Einführend erläuterte uns Herr Rau, der Leiter der Hochbauabteilung, in einer Firmenpräsentation die Philosophie und den Aufbau von Stahlbau Plauen. Auch der Werdegang der Firma sowie aktuelle und bereits ausgeführte Projekte wurden vorgestellt.
Die Plauen Stahl Technologie GmbH ist ein leistungsstarkes Stahlbauunternehmen mit über 130 Mitarbeitern und einer Jahreskapazität von ca. 20.000 t Stahlkonstruktion. Die Firma bietet ein umfassendes Leistungsspektrum, beginnend mit dem Projektmanagement, der Projektierung bzw. Entwurfsunterstützung über Ingenieurleistungen und Fertigung bis hin zur Montage. Hierbei hat man sich auf die Produktgruppen architektonischer Stahlbau, Geschoss- und Verbundbau, Hallen, Kraftwerksbau und Brückenbau spezialisiert.
Der Stahlbau in Plauen entstand 1885 mit der Gründung der Firma F. Sachs, Plauen. 1947 wurde der VEB Stahlbau Plauen im Verbund des VVB Eisenkontor Land Sachsen, Dresden gegründet. Nach mehreren Umbenennungen wurde die Firma 1990 in eine GmbH umgewandelt, deren Geschäftsanteile häufig den Besitzer wechselten. Die Plauen Stahl Technologie GmbH als selbstständiges mittelständisches Unternehmen existiert seit Juli 2003.
Anschließend wurden wir zu einer Werksbesichtigung eingeladen, bei der wir einen guten Eindruck von der Arbeitsweise und dem Betätigungsfeld eines mittelständischen Stahlbauunternehmens bekamen. Von der Lagerung und Warenkennzeichnung über Zuschnitt und Schweißtechnik bis hin zum Korrosionsschutz konnten wir jeden Arbeitsschritt sehen, der zur Verarbeitung von Profilstahl und Stahlblechen zu bis zu 150 t schweren Stahlbauteilen notwendig ist.
Im Speziellen konnten wir die Fertigung von Bauteilen für die Schrägseilbrücke Niederwartha, das Kraftwerk Boxberg sowie letzte Arbeiten an einem Donauschleusentor beobachten.
Nach dem Mittagessen in der Werkskantine, zu dem uns die Firma einlud, ging es weiter Richtung Magdeburg.
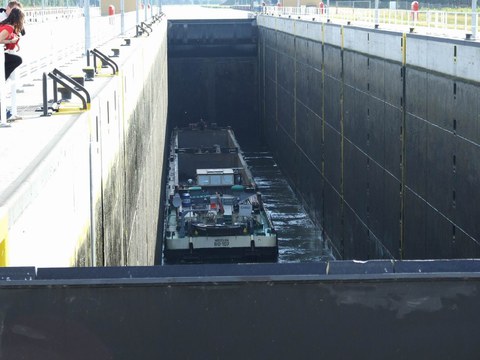
Schleuse in Betrieb
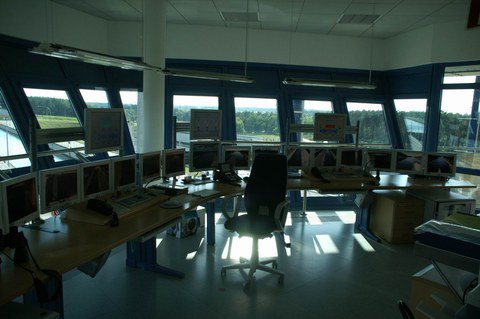
Kontrollraum der Schleusenanlage
Nach ca. 3 Stunden Busfahrt erreichten wir um 17.00 Uhr unser nächstes Ziel: Das Wasserstraßenkreuz Magdeburg. Hier erwartete uns bereits Herr Fiedler vom Wasserstraßen-Neubauamt Magdeburg und begann sogleich seine fachkundige Führung. Bereits 1934 wurde mit dem Bau der Kanalbrücke und des Schiffshebewerkes bei Hohenwarthe begonnen. Nur acht Jahre später mussten die Bauarbeiten allerdings kriegsbedingt eingestellt werden. Da die Elbe oft für die Schifffahrt unzureichende Wasserstände hat, entstanden neue Pläne, die Elbe mit einer Kanalbrücke zu queren und den bestehenden Höhenunterschied zwischen Elbe-Havel-Kanal und Mittellandkanal durch eine Schleuse bei Hohenwarthe auszugleichen. Vor der Fertigstellung des Wasserstraßenkreuzes (10. Oktober 2003) musste die Schifffahrt einen 12 km langen Umweg über die Elbe in Kauf nehmen. Dieser auf den ersten Blick harmlos erscheinende Mehraufwand vergrößerte sich noch, wenn man neben den schwankenden Elbwasserständen in Betracht zieht, dass der Trog des Schiffshebewerkes Rothensee auf 82 m lange Schiffe begrenzt ist.
An der Stelle des vor dem Zweiten Weltkrieg begonnenen Schwimmerhebewerkes Hohenwarthe wurde vom November 1998 bis zum Oktober 2003 die Doppelsparschleuse Hohenwarthe errichtet. Dazu mussten zunächst die Schächte des zurück gebauten Hebwerkes aufgefüllt und tiefenverdichtet werden, um Setzungen zu vermindern.
Am östlichen Ende der Mittellandkanalhaltung müssen Schiffe einen Höhenunterschied von ca. 18,5 m zum Elbe-Havel-Kanal überwinden. Um Wasser (Kanalwasserhaltung) und Pumpenergie zu sparen, wurden seitlich der Schleuse jeweils drei gestaffelt übereinander liegende Sparbecken für die Berg- und die Talschleusung angeordnet. Dadurch können 60 % des Schleusungswasserbedarfs eingespart werden. Im „regulären“ Betrieb müssen die übrigen 40 % des Kammerinhalts der oberen Haltung zurückgeführt werden. Aufgrund der Rekultivierung von Tagebaulandschaften besteht im Elbe-Havel-Kanal ein erhöhter Wasserbedarf, deshalb wird etwa bis zum Jahr 2010 auf eine Wasserrückführung verzichtet und zusätzlich durch Leerschleusungen eine tägliche Mindestanzahl an Schleusvorgängen sichergestellt.
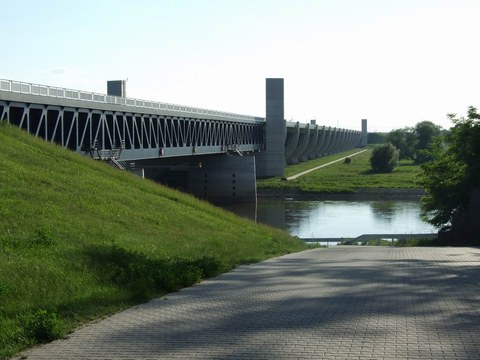
Kanalbrücke über die Elbe

Detail: Lager
Das Herzstück des Wasserstraßenkreuzes Magdeburg bildet Europas längste Kanalbrücke. Die 918 Meter der Trogbrücke verteilen sich zu zwei Dritteln auf die Vorlandbrücke (690 m, 16 Felder) und zu einem Drittel auf die Strombrücke (228 m, 3 Felder).
Der Entwurf der Strombrücke lehnt sich stark an die 1934 begonnene Kanalbrücke an. Bedenkt man die extreme Belastung der Brücke, so wirkt sie durch die als Fachwerke aufgelösten Hauptträger fast schon filigran. Die Lasten werden von den etwa 1,90 m hohen Querträgern in die Längsträger geleitet. Die einzelnen Lager der Strombrücke müssen eine Vertikallast von ca. 135 MN (entspricht 13.500 t) abtragen – bei einem Eigengewicht von 35 t.
Nach der ausführlichen und interessanten Führung ging unsere Reise weiter in Richtung Braunschweig, wo wir in einem gemütlichen Hotel (in Familienbetrieb) die Nacht verbrachten.
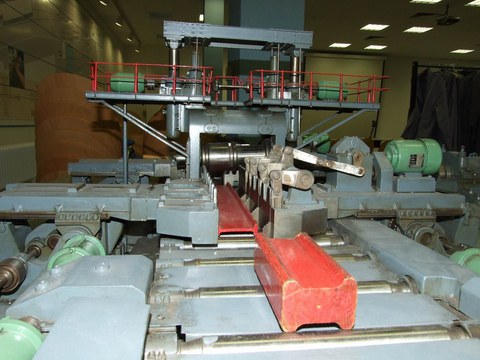
Modell zur Veranschaulichung des Herstellungsprozesses - horizontales Walzenpaar mit Träger
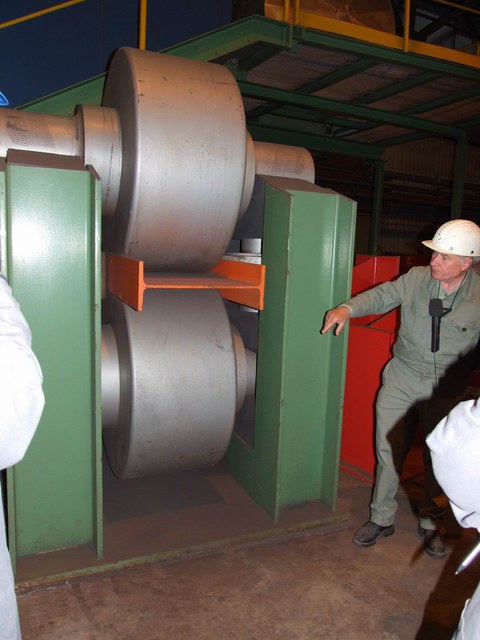
Modell zur Veranschaulichung des Herstellungsprozesses - Walzstraße
Der erste Programmpunkt des zweiten Tages unserer Exkursion war das Walzwerk der Salzgitter AG in Peine, das wir um 9:00 Uhr erreichten. Dort wurden wir im Besucherzentrum von Mitarbeitern des Unternehmens empfangen.
Nach einer kurzen Begrüßung wurde uns in sehr anschaulicher Art und Weise das Stahlwerk vorgestellt. Dabei erfuhren wir, dass es sich bei der »Peiner Träger GmbH« um ein Unternehmen der Salzgitter Gruppe handelt, das derzeit etwa 1240 Mitarbeiter beschäftigt.
Die Geschichte des Walzwerkes reicht zurück bis ins ausgehende 19. Jahrhundert. Einen Meilenstein der Firmengeschichte stellte das Jahr 1914 dar, in welchem das Patent für den Breitflanschträger erworben wurde, der seither als „Peiner Träger“ auch international vertrieben wird.
Im Verlauf einer wechselvollen Geschichte wuchsen die verschiedenen Standorte der Salzgitter AG zu einem innovativen und leistungsfähigen Stahlkonzern. Heute zählt die Salzgitter Gruppe zu den führenden Stahltechnologiekonzernen Europas.
Für die Stahlerzeugung stehen in Peine ein Elektrolichtbogenofen (700 V/130 kA), ein Pfannenofen, ein Spülstand und eine Stranggussanlage zur Verfügung, wobei als Ausgangsmaterial ausschließlich Schrott Verwendung findet. Zu Trägern oder Spundwänden können die so hergestellten Vorblöcke bzw. Beam Blanks, die zu einer Rationalisierung der Trägerproduktion beitragen, wahlweise auf der »Universalmittelträgerstraße« oder der »Schweren Trägerstraße« weiterverarbeitet werden.
Ein Film über die Firmengeschichte und die Technologien der Stahlherstellung rundete den ersten Teil der Besichtigung ab.
Nachdem sich die Mehrheit der Exkursionsteilnehmer für die Besichtigung der »Schweren Walzstraße« entschieden hatte, wurde die Gruppe zweigeteilt und jeder Einzelne mit Schutzkleidung, inklusive Helm und Brille, sowie Kopfhörern ausgerüstet.
Zu Beginn der Führung wurde uns am Modell die Herstellung der parallelflanschigen Breitflanschträger erklärt, wobei die Erzeugung der gewünschten Trägerformen im Reversierverfahren erfolgt. Üblicherweise werden so Profile zwischen 14 und 24 m Länge hergestellt. Wir konnten beobachten wie ein Vorblockeinsatz mit Abmaßen von 280 x 420 mm aus dem Hubbalkenofen kommend zuerst zum Vorprofil ausgewalzt wurde, um anschließend zum fertigen Profil geformt zu werden.
Vorbei an der Zuschnitteinheit und dem im Freien befindlichen Bereich zur Abkühlung der Träger bildete die Besichtigung der Rollrichtmaschine den Abschluss der Werksführung. Das Besondere an dieser Anlage, die zur Gewährleistung der Geradheit und geringer Winkelabweichungen der »Peiner Träger« beiträgt, war die stehende Anordnung der Rollen. Diese Orientierung der Rollen findet eher selten Verwendung, bietet aber viele Vorteile, so müssen zum Beispiel die Träger für die anschließende Prüfung nicht gedreht werden.
Den Abschluss des Besuchs im Walzwerk bildete ein gemeinsames Mittagessen in der Werkskantine, bei dem die Möglichkeit bestand, offen gebliebene Fragen zu klären.
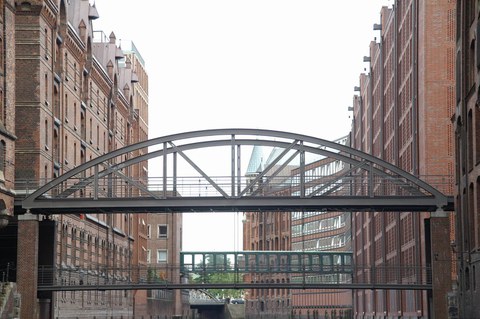
Speicherstadt Hamburg
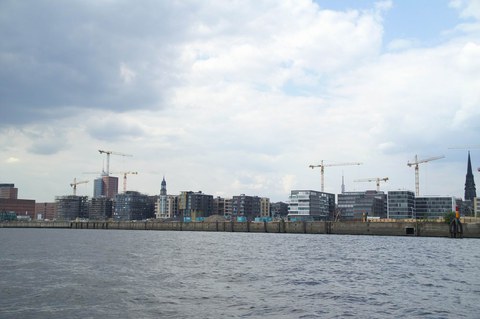
HafenCity Hamburg
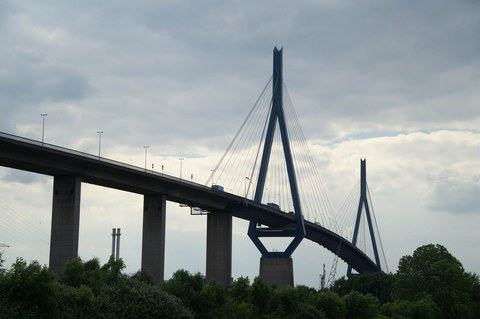
Köhlbrandbrücke
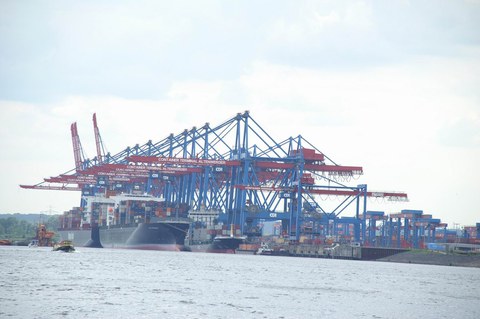
Container Terminal Altenwerder
Als der Hunger gestillt und alle Fragen beantwortet waren, setzten wir unsere Fahrt in Richtung Hamburg fort, wo wir am frühen Nachmittag eintrafen. Dort wurden wir zunächst von Herrn Dr. Schmitt, einem Mitarbeiter der HPA, begrüßt. HPA steht für die Hamburg Port Authority, die so genannte Hafenverwaltung, die vor allem für die Erstellung und Instandhaltung der Infrastruktur im Hamburger Hafen zuständig ist. Von unserem Treffpunkt aus ging es weiter auf eine der vielen Barkassen für die nun folgende Hafenrundfahrt. Zunächst fuhren wir durch die Speicherstadt, den größten auf Eichenpfählen gegründeten Lagerhauskomplex der Welt. In der Vergangenheit diente die Speicherstadt der Lagerung und Verladung von Stückgut wie Tee, Kaffee und Gewürzen. Heute sind vor allem Teppichhändler, Agenturen, Museen und Ausstellungen in den alten Backsteingebäuden ansässig. Weiter ging es auf dem Wasser in Richtung der Großbaustelle HafenCity, wo bis 2008 ein eigener Stadtteil mit Büroflächen und Wohnungen entstehen wird.
Am Ende der Rundfahrt galt unsere Aufmerksamkeit der Hafenstadt und den Landungsbrücken, dem Alten Elbtunnel sowie dem Hamburger Fischmarkt mit der Fischauktionshalle.
Zurück am Anleger hieß es, keine Zeit zu verlieren, denn unsere Reise sollte an diesem Tag noch nach Stralsund gehen.
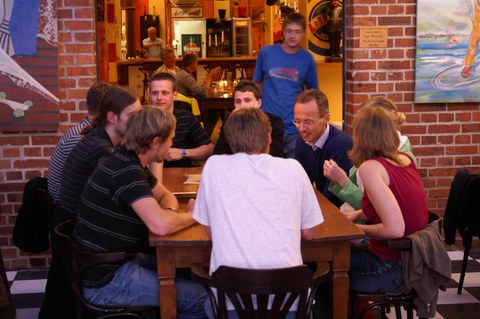
Im Restaurant Fisherman’s in Stralsund
Um ca. 21:00 Uhr in Stralsund angekommen, bezogen wir zügig unsere Quartiere im InterCity Hotel, denn es war noch ein gemeinsames Abendessen geplant. Dieses nahmen wir im Restaurant Fisherman’s ein, einer urigen Gaststätte mit Blick auf den Hafen.
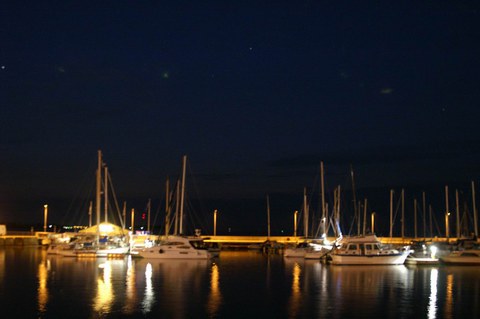
Blick auf den Hafen in Stralsund
Tag drei unserer Exkursion begann mit der Besichtigung der 2. Strelasundquerung in Stralsund.
Im Informationszentrum PYLONeum hörten wir zunächst einen ausführlichen Vortrag über den Rügenzubringer und die 2. Strelasundquerung.
Die Linienbestimmung mit weitreichenden Voruntersuchungen für dieses Projekt fand bereits im Juni 2000 statt, der erste Spatenstich war im August 2004. Die Strelasundquerung gehört zum Verkehrsprojekt Deutsche Einheit „Zubringer von der BAB 20 nach Bergen/Rügen“. Die 53,2 km lange Trasse wird voraussichtlich Ende 2008 fertig gestellt sein.
Das Kernstück der insgesamt 4.100 m langen Querung zwischen der Ortsumgehung Stralsund und der AS Altefähr bildet ein rund 2.830 m langer Brückenzug. Das parallel zum bestehenden Rügendamm verlaufende Gesamtbauwerk setzt sich aufgrund der variierenden Überbaukonstruktion aus sechs Einzelbauwerken zusammen, den Vorlandbrücken Stralsund, der Ziegelgrabenbrücke, den Vorlandbrücken Dänholm und Strelasund sowie der Strelasundbrücke.
Zur Freihaltung einer 42 m hohen und 126 m breiten Schneise für die Schifffahrt entschied man sich bei der Ziegelgrabenbrücke für eine Schrägseilvariante. Statisch wirkt diese als überspannter Balken, denn die 127,75 m hohen Pylonen ruhen auf Kalottenlagern. Der Stahlüberbau mit einer orthotropen Fahrbahnplatte wird von insgesamt 32 in Harfenform angeordneten gespannten Stahlseilen über den zwei Hauptöffnungen (126 m / 198 m) getragen. Bei einem Variantenvergleich erwies sich ein zweiteiliger Pylon in Tropfenform als optisch und statisch überzeugendste Lösung.
Nach dem aufschlussreichen Vortrag ging es auf die Brückenbaustelle. Am PYLONeum wurden uns noch die verschiedenen innovativen Neuerungen vorgestellt, wie das H4b-System was einen 38 „Tonner“ mit 60 km/h zurückhalten soll, oder die geräuschärmeren Fahrbahnübergänge.
Anschließend fuhren wir mit dem Bus den alten Rügendamm entlang, von dem aus man das gesamte Vorhaben überblicken kann, und erhielten fachkundige Erläuterungen zu allen Bauabschnitten.
Nach diesem Gesamteindruck durften wir die Baustelle bis zur Hauptöffnung zu Fuß besichtigen. Hierbei wurde uns eine weitere Innovation – in der Herstellung der Schrägseile – vorgestellt. Aufgrund eines Vogelschutzgutachtens war ein Mindestdurchmesser der Seile von 18 cm notwendig, was bei herkömmlichen Konstruktionen zu einem beträchtlichen Durchhang geführt hätte. So wurden die Schrägseile – in Deutschland einmalig – mit Einzellitzen ausgeführt, was den Vorteil der Austauschbarkeit einzelner Glieder aufweist.
Die interessanten Informationen zum Bauwerk wurden von einer wunderbaren Aussicht auf Stralsund und die Ostsee abgerundet.
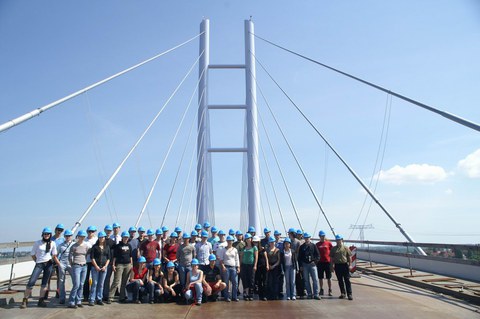
Gruppenfoto auf der Strelasundbrücke
Nach einem Mittagsimbiss am Hafen Stralsund fuhren wir weiter Richtung Warnemünde, zum letzten Programmpunkt unserer Exkursion: der Aker Warnow Werft.
Punkt 15:00 Uhr begrüßten uns Herr Kuchorzak und Herr Höffner mit einer kurzen Einführung in die Schiffbau-gruppe Aker Yards ASA und führten uns anschließend mit Hilfe zweier Kollegen in vier Gruppen über das Werftgelände.
Die Aker Yards ASA mit Hauptsitz in Oslo ist eine internationale Schiffbau-gruppe, die auf den Bau anspruchs-voller Schiffe ausgerichtet ist. Zu den Aker Yards zählen 17 Werften in 7 Ländern mit insgesamt 20000 Mitarbeitern. Neben Kreuzfahrtschiffen und Fähren umfasst die Produktpalette Handelsschiffe, Offshoreanlagen und Spezialschiffe.
Die Werft in Warnemünde und die Werft in Wismar sind die einzigen deutschen Standorte der Aker Yards ASA. Sie sind momentan auf den Bau von Handelsschiffen ausgerichtet. Mit insgesamt ca. 2.300 Mitarbeitern an beiden Standorten soll die Ablieferung in diesem Jahr zwischen 15 und 16 Containerschiffen betragen. Um jedoch auch in Zukunft die Auftragslage zu sichern, wird zunehmend der Spezialschiffbau und der Bau eisbrechender Containerschiffe in Betracht gezogen. Bemerkenswert ist die enge Zusammenarbeit der Werften in Wismar und Warnemünde. So wird in Warnemünde das komplett ausgerüstete Vorschiff gefertigt, in Wismar hingegen das mit dem Antriebsaggregat und Propeller ausgestattete Achterschiff. Die Endmontage erfolgt nach dem Verschleppen des Vorschiffes in Wismar.
Beide Werften wurden Mitte bis Ende der 90iger Jahre umfangreichen Modernisierungsmaßnahmen unterzogen. So musste in Warnemünde die Helling mit der weithin sichtbaren Kabelkrananlage zum Teil neuen Produktionshallen und einem um ein vielfaches leistungsfähigeren 600-t-Portalkran weichen. Heute gehören beide Werften zu den modernsten weltweit.
Der Bau des Vorschiffes in Warnemünde erfolgt sektionsweise und beginnt mit dem Zuschnitt der Bleche. Diese werden mit Hilfe von autogenen oder Plasma-Schneidanlagen bei einem Verschnitt von 15 – 20 % zugeschnitten. Anschließend erfolgt das partielle Fügen einzelner Bleche mittels UP-Einseitenschweißanlagen und Schweißroboterportalen, sowie das automatische Besteifen. Das Fügen von 200 bis 600 t Sektionen erfolgt vorwiegend manuell mit den Schweißverfahren MAG-Fülldraht (136) und Lichtbogenhandschweißen (111). Eine Gewichtsüberprüfung der Sektionen wird während des kompletten Fertigungsprozesses durchgeführt. Ebenso werden Schweißnähte nach einem Schweißnahtprüfplan geprüft. Zu den kritischen und somit zu prüfenden Schweißnähten im Schiffbau zählen beispielsweise Kreuzstöße in der Schiffsaußenhaut. Diese erhält ihre Formgebung durch das Aufspannen auf eine Pin-Jet-Lehre, wobei entstehende Eigenspannungen in Kauf genommen werden. Die gefertigten Sektionen werden auf Pallungen gelagert, welche vorrangig unter Querschotts und Längssteifen angeordnet werden, um ein Beulen der Außenhaut zu vermeiden. Nach dem Strahlen und Beschichten der einzelnen Sektionen in riesigen Beschichtungshallen werden diese vollständig ausgerüstet und zum kompletten Vorschiff verschweißt. Für den Transport zur Endmontage nach Wismar wird, sofern erforderlich, das letzte Querschott wasserdicht verschweißt und das komplette Vorschiff mittels Sektionsflutung getrimmt, damit es auf der Überfahrt nicht kentert oder gar sinkt.
Diese beeindruckende Präsentation des Einsatzes von Stahl bildete den krönenden Abschluss unserer Exkursion.
Ausklingen ließen wir unsere Fahrt mit einem Ausflug in die Innenstadt von Warnemünde. Diesen nutzten wir für einen halbstündigen Kurzurlaub am Strand, der einige Mutige sogar zum Baden in der eiskalten Ostsee motivierte.
Nach einem letzten gemeinsamen Abendessen im Restaurant Atlantic begannen wir unseren langen Rückweg nach Dresden. Gegen 2:00 Uhr erreichten wir müde und um viele Eindrücke bereichert unser Ziel.